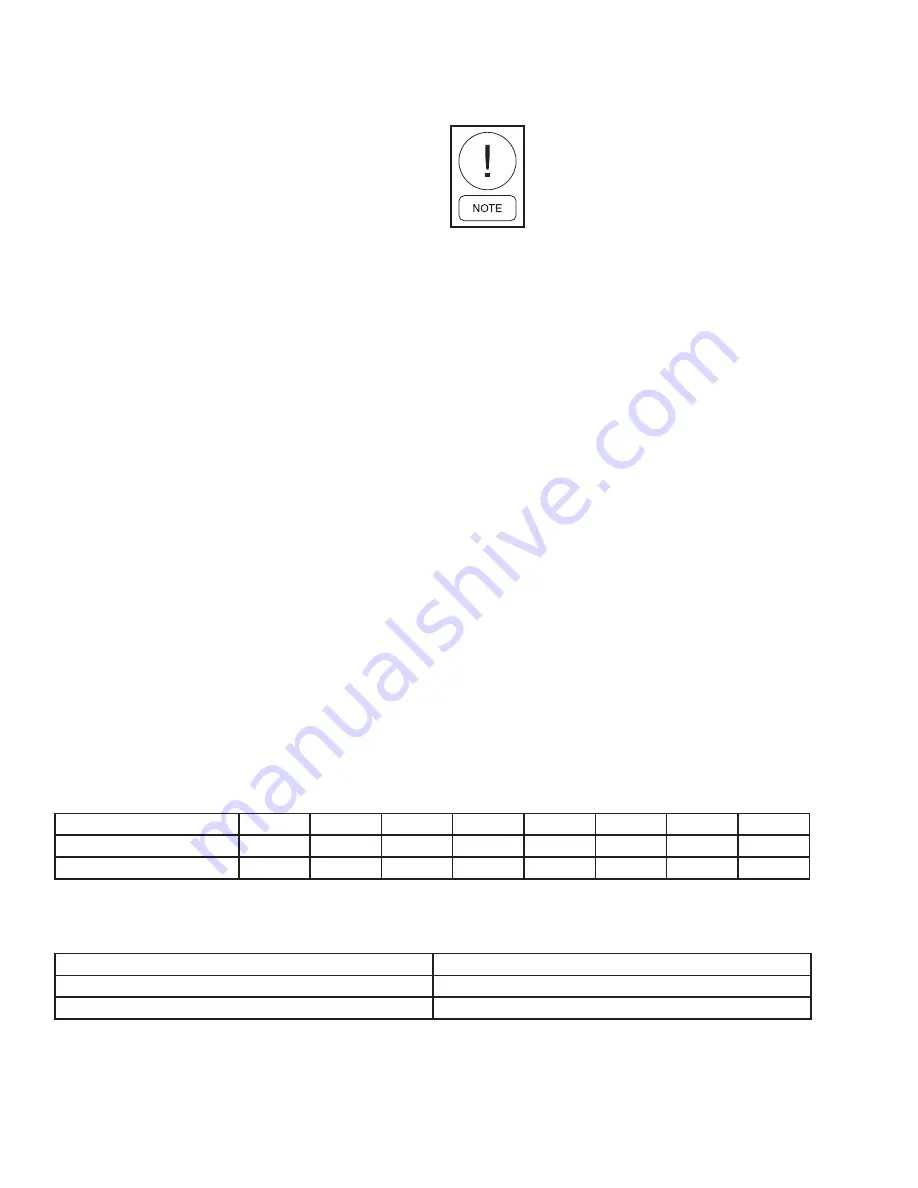
Vibration Causes
1. Wheel imbalance.
a. Dirt or debris on wheel blades.
b. Loose setscrews in wheel hub or bearing-to-
shaft.
c. Wheel distorted from over-speed.
d. Wheel balance weight missing.
2. Bent blower shaft.
3. Drive faulty.
a. Variable pitch sheaves - Axial and radial run-
out of flanges; uneven groove spacing; out of
balance. Also similar fault in driven sheave.
b. Bad V-belts; lumpy, or mismatched belts.
c. Belt tension too tight or loose.
4. Bad bearings, loose bearing hold-down bolts.
5. Motor imbalance.
6. Fan section not supported evenly on foundation.
7. Fan shaft not parallel with motor shaft.
Periodic Service and Maintenance
1. Check all moving parts for wear every six months.
2. Check bearing collar, sheave, and wheel hub set-
screws, sheave capscrews, and bearing hold-down
bolts for tightness every six months.
TABLE 7 -
FORWARD CURVE FAN DATA
DIAMETER
9 X 4
9 X 6
10 X 7
12 X 9
12 X 12
15 X 11
18 X 13
18 X 18
Maximum RPM Class I
2200
2200
2000
1800
1700
1600
1200
1200
Maximum RPM Class II
N/A
N/A
N/A
N/A
N/A
1700
1475
1450
Note: Maximum air temperature through fan section is 225°F (107°C)
TABLE 8 -
VIBRATION LEVELS
FAN SPEED (RPM)
VIBRATION
800 or less
5 mils maximum displacement
801 or greater
.20 in/sec. Maximum velocity
Note: Excessive vibration from any cause contributes to premature fan and motor bearing failure. Overall, vibration levels should be monitored
every six months of operation. An increase in levels is an indication of potential trouble.
APPLICATION RECOMMENDATION FOR
COILS
Observe all local codes and industry
standards
General
Piping design, sizing, and installation information
presented in the ASHRAE Handbooks should, be fol-
lowed in the design and installation of piping.
Water Cooling Coils
1. Water supply, water return, drain and vent con-
nections are labeled on the end panel.
2. Water supply and water return connections are
checked.
3. Avoid undue stress to the connection extending
through unit panel. Use backup pipe wrench to
avoid breaking the weld between coils connection
and header.
4. Follow recommendations of the control manufac-
turer regarding types, sizing and installation of
control valves.
Direct Expansion Coils
1. The coil suction connection extended through the
end panel of the coil section. The coil distributor
is located inside the cabinet on the same side as
the suction connection.
JOHNSON CONTROLS
30
FORM ET102.19-NOM1
ISSUE DATE:08/26/2013
SECTION 4 - PERIODIC MANINTENANCE AND SERVICE