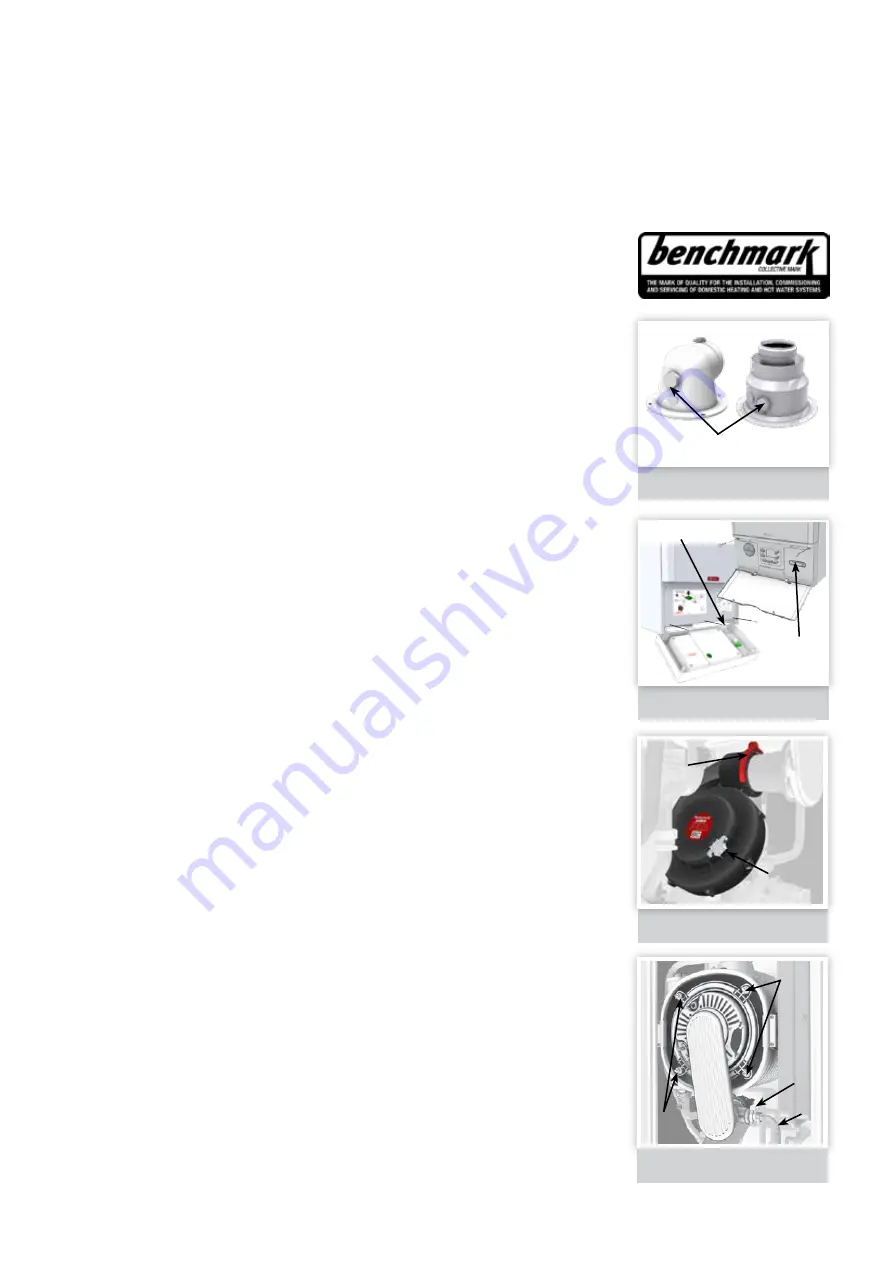
www.johnsonandstarley.co.uk
28
FIGURE 31.
DOOR REMOVAL
FIGURE 30.
FLUE GAS TEST POINTS
FLUE GAS TEST POINTS
FIGURE 32.
FAN REMOVAL
CLIP
MAINS
ELECTRICAL
CONNECTION
FIGURE 33.
BURNER ARM & HEAT EXCHANGER
FIXING
NUTS
FIXING
NUTS
GAS
PIPE
CLIP
SCREWS
CAP &
SCREW
17.3.2
Clean the heat exchanger & condensate trap/siphon.
17.3.3 Check the main injector for blockage or damage.
17.3.4 Check that the flue terminal is unobstructed and that the flue system is sealed correctly.
17.3.5 After completing the servicing or exchange of components always test for gas tightness.
17.3.6
When work is complete the front panel MUST be correctly refitted, ensuring that a good seal is made.
17.3.7
Check the gas consumption.
17.3.8
Check combustion by connecting the flue gas analyser to the flue gas sampling point and measure the
CO & CO
²
. See Figure 30.
If the CO/CO
²
ratio is greater than 0.004 and the integrity of the complete flue
system and combustion circuit seals have been verified and the inlet gas pressure
(and gas rate) have been verified, then contact Johnson & Starley Ltd.
17.3.9 Once the service is complete, fill in the relevant section in the Benchmark
Checklist located at the back of this book
17.4
FLUE INSPECTION & CHECKS
PLEASE NOTE:
During routine servicing, and after any maintenance or change of part of
the combustion circuit, the following must be checked:
• The integrity of the flue system and the flue seals
• The integrity of the boiler combustion circuit and the relevant seals
• The operational (working) gas inlet pressure at maximum rate.
• The gas rate.
• The combustion performance.
Competence to carry out the check of combustion performance.
PLEASE NOTE:
BS 6798 Specification for installation and maintenance of gas-fired
boilers of rated input not exceeding 70kW net advises that:
• The person carrying out a combustion measurement should have been assessed as
competent in the use of a flue gas analyser and the interpretation of the results.
• The flue gas analyser used should be one meeting the requirements of BS 7927 or
BS EN 50379-3 and be calibrated in accordance with the analyser manufacturers
requirements.
• Competence can be demonstrated by satisfactory completion of the CPA1 ACS
assessment, which covers the use of electronic portable combustion gas analysers in
accordance with BS 7967, Parts 1 to 4.
GAINING ACCESS TO THE BOILER
17.5
CONTROL PANEL & FRONT DOOR REMOVAL
17.5.1 Lower the flip door and remove the 2 screws cover plugs and unscrew the 2
screws. See figure 31. Drop down and move the control panel assembly. See
figure 31.
17.5.2. To remove the door remove the 5 screws. Lift up forward and remove.
17.5.3
Refit in reverse order.
17.6
FAN REMOVAL
Refer to paragraph 17.5
17.6.1
Disconnect the front mains electrical connection.
17.6.2 Remove the red securing clip, noting its correct position. Slide the fan
backwards off the venturi.
17.6.3
Remove the second electrical cable from the rear of the fan.
17.6.4
Replace with new and refit by aligning the grooves on the side of the fan and
slot back into place.
17.5.5
Refit in reverse order.
17.7
BURNER ASSEMBLY REMOVAL
Refer to paragraphs 17.5 and 17.6
17.7.1
Remove the gas pipe securing clip. Undo the gas pipe.
17.7.2
Remove the ignition/detection and earth leads.
17.7.3
Remove the 4 burner fixing nuts using a 10mm spanner.
17.7.4
Lift out the burner from the combustion chamber.
17.7.5
Brush off any deposits that may be on the burner with a soft brush. Inspect the
ignition/detection electrode and check the electrode gaps. See Figure 38.
17.7.6 Inspect the black rubber sealing gasket around the burner for any signs of
damage. Replace if necessary. The blue rope braid seal should not be removed
under any circumstances and it is not a serviceable item.
17.7.7
Refit in reverse order.