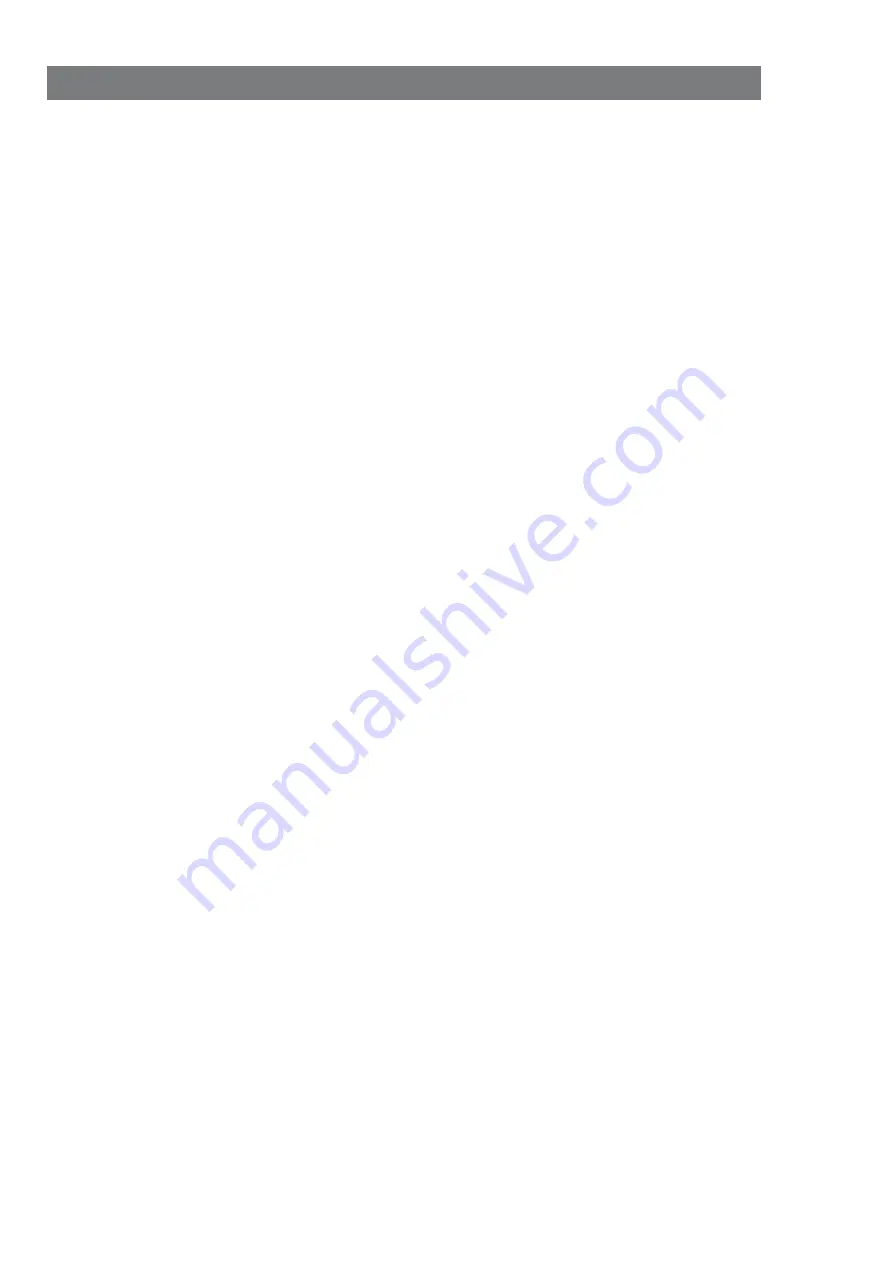
www.johnsonandstarley.co.uk
6
3
26
4.
DUCT SYSTEM
4.1
RETURN AIR
4.1.1
All return air shall be POSITIVELY ducted from outside the compartment to the top of the unit via a return air
duct, and mechanically secured. It is recommended that the return air duct be not routed directly from the main
living area, but from a convenient central area serving the remainder of the dwelling.
4.1.2 The return air system should be constructed of fire-resistant material. The flue shall not be run through an area
serving as a return air path. It is extremely important that the correct size of return air grilles and ducting is used.
For heaters on maximum output the return air duct size should not be less than the equivalent of 300mm x 300mm
(12" x 12"). If flexible duct is used the duct diameter should not be less than 350mm (14") dia. The return air
grille should have a free area of not less than 1593cm
2
(247in
2
).
4.1.3
An adequate and unobstructed return air path is essential from areas not served by a directly ducted return and to
which warm air is delivered. All such rooms should be fitted with relief grilles which have a free area of
0.0088m
2
/kW (1in
2
/250Btu/h) of heat supplied to the room. The only exceptions are kitchens, bathrooms and
WC.’s.
4.1.4 The return air duct should allow for ease of removal for access to the flue.
4.1.5 All duct work in the room or internal space in which the heater is installed shall be mechanically secured, and
sealed with ducting tape.
4.2
WARM DELIVERED AIR
4.2.1
All duct work, including riser ducts, should be fully insulated with 50mm (2in) fibreglass or similar. If short extended
duct runs are taken below floor level these should be similarly insulated, and in addition wrapped with a sound
vapour proof barrier, and protected from crushing.
4.2.2
The duct system should be carefully designed (as given in the guidelines in the British System Design Manual) to
suit the needs of its specific heating requirements and building layout. The type of duct system, (i.e. radial/
extended plenum/stepped) should be installed using the least number of fittings to minimise airflow resistance.
The base duct, which equalises the air pressure to supply ducts, shall be constructed to support the weight of the
heater, which shall be secured to the plenum with screws on at least two sides, and sealed using self-adhesive
foam strip, ducting tape or sealing compound. All ducting and blanking plates shall be mechanically secured and
sealed.
5.
INSTALLATION REQUIREMENTS
Note: For ELJAN 6 circulator Installation Instructions, see separate instructions ZZ778.
5.1
FLUES
(see British Standards BS 5440 Pt. 1 Flues)
5.1.1
All joints shall be soundly sealed.
5.1.2
The flue should be kept as short and warm as possible.
5.1.3
Sufficient support brackets shall be installed to bear the weight of the total flue system.
5.1.4
The spigot connection of the heater draught diverter will accept internally the spigot end of a non-asbestos flue
to BS 567 or twin wall metal flue to BS 715 of nominal 125mm (5in) diameter.
5.1.5 A split collar should be fitted to provide for flue maintenance or inspection.
5.1.6 The flue shall be in accordance with the Building Regulations and British Gas Materials and Installations
specification 3rd edition) with regard to clearance and shielding from combustible materials.
5.1.7 All materials shall be in accordance with Building Regulations requirements.
5.1.8 The flue should run as vertically as possible. Horizontal runs should be avoided if at all possible and any
directional change should be as gentle as possible. If there is any doubt about the flue configuration, the
equivalent flue height should be determined (see 5.1.11).
5.1.9
If the appliance to be fitted is a replacement, the old appliance should be checked for signs of spillage prior to
commencement of the installation and appropriate action taken, (i.e. check flue system and renew as necessary).
10.
SHORT LIST OF SPARES
ITEM G.C.
MAKER’S
DESCRIPTION
QTY
No
No
No
1
245-176 J650-0525000
Fan assembly
1
2
E02-430 J652-0182000
Filter tray assembly
1
3
244 985 CL3S
Time control CL3
1
4
244 986 1000-0000040
Time control cover
1
5
384 739
BOS00105
Limit Switch
1
Honeywell L4069C
6
393 412
BOS01301
Multifunctional Control
1
Honeywell V8600C
7
232 903 BOS02061
Sealing ring (for item 6)
2
8
244 880 BOS02397/4
Pilot assembly
1
9
392 935 1000-0701260
Pilot Injector
1
10
E02-431 1000-0705390
Pilot Feed Pipe
1
11
386-820 1000-0703870
Thermocouple
1
12
386 775 BOS01970
Electrode
1
13
397 819 BOS02394
Electrode lead
1
14
244 898 BOS02406
Electrode Nut
1
15
E02-554 J652-0391000
Spillage switch (TTB) Assembly
1
16
E02-555 J652-0700000
Burner and Controls Assembly
1
17
E02-432 1000-0705290
Burner and Cross Lighter Assembly
1
18
398 353 208S711
Main Injector Bray Cat 23/850
2
19
E02-422 1000-0705340
Cross Lighting Injector (Bray)
1
or
E02-423 1000-0705310
Cross Lighting Injector (Stereomatic)
1
20
E02-556 J652-0350005
Heat Exchanger exchange kit
1
21
395 945 1000-0700570
Piezo Unit
1
22
244 971 B300-0706000
Igniter Bracket
1
23
230-394 BOS 00836
Gasket (for heat exchanger cap)
2
24
E02-557 J652-0161000
Lower Compartment Door
1
MODAIRFLOW MODELS
25
E02-559 J652-0156000
Fan Compartment Door
1
26
245 174 J650-0530005
Control Panel with Transformer
1
27
245 137 J650-0519000
Wiring Harness
1
28
245 178 R010
Electronics Module
1
29
245 170 1000-0505690
Airflow Sensor
1
30
E02 428 1000-0514230
Fuse 1A, (T)
2
31
386 475 BOS01242
Thermista-stat
1
32
E02-433 1000-0516875
Transformer
1
NON-MODAIRFLOW MODELS
33
E02-560 J652-0157000
Fan Compartment Door
34
245 142 1000-0501910
Control Panel
1
35
245 094 J650-0520005
Wiring Harness
1
36
385 159 BOS00104
Fan Delay Control Honeywell L4068C 1
37
244 938 1000-0513820
Fuse 3.15A, (T)
1
38
245 322 1000-0500910
Relay 24V
1
4
25
5.1.10 It is recommended that at least 600mm of vertical flue should be provided from the top of the draught diverter
(for new installations this shall be incorporated into the flue design). However, when carrying out replacement
installations, an existing flue system may be encountered, where the vertical flue above the appliance to the first
bend is less than 600mm. In the first instance, the installer must judge whether this distance can be achieved
practicably by some means. Where this is not practicable, the existing flue system may be used, providing there is
no evidence of spillage from the old appliance (see 5.1.9 above). Every effort must be made, however, to ensure
that the existing flue complies in every other way to BS 5440 Part 1, including the visual inspection, flue flow and
spillage test described in 4.3.2 of the above standard. Flue configurations may be assessed in terms of equivalent
vertical height - details are given in 5.1.11. For air heaters, the minimum equivalent vertical height is 1 metre. The
installer must make a judgement based on his knowledge and experience and the examination and testing
described above as to whether an existing flue system can be used.
Note:
Ventilation of the compartment, room or internal space in which the appliance is to be installed must be checked
for compliance with the requirements of BS 5440 Part 2 ( Ref. Section 3 of these instructions) and upgraded as
necessary.
5.1.11
Calculation method for flue sizing: ( from BS 5440: Part 1, Appendix A)
a.
This appendix provides a procedure for estimating whether a given flue design is likely to ensure full
clearance of combustion products.
b.
The procedure is based on calculating the ‘equivalent height’ of the flue under consideration, i.e. that
height of the straight vertical circular flue pipe of specific size which will produce the same flow rate as
the flue under consideration. The equivalent height is calculated from the formula:
(K
i
+ K
o
)
e
H
e
= H
a
x ____________________
(K
i
+ K
o
)
a
- K
e
H
a
+ Sum K
where:
H
e
is the height of the equivalent flue;
H
a
is the vertical height of the actual or proposed flue;
K
i
is the inlet resistance of the flue;
K
o
is the outlet resistance from the flue;
subscript e refers to the equivalent flue diameter;
subscript a refers to the actual or proposed flue diameter;
K
e
is the resistance per unit length of the equivalent flue;
Sum K is the resistance (other than the inlet and outlet resistance) of the actual or proposed flue.
Note:
K and Sum K are obtained from Table 2. K
o
and K
i
are obtained from Table 3.
c.
Table 2 gives resistance factors for common flue components for use in the formula. Table 3 contains the
appropriate inlet and outlet flue resistances. (
the flue is likely to be satisfactory if its equivalent height
exceeds 1m
).
Component
Internal Size
Resistance
Component
Internal Size
Resistance
(mm)
Factor
(mm)
Factor
Flue Blocks
197 x 67
0.85 per meter
45
O
Bend
100 mm pipe
0.61 per
231 x 65
0.65 run
125 mm pipe
0.25 fitting
317 x 63
0.35
150 mm pipe
0.12
140 x 102
0.60
197 x 67
0.30
200 x 75
0.60
231 x 65
0.22
183 x 90
0.45
317 x 63
0.13
Pipe
100
0.78
Raking block
Any
0.30 per block
125
0.25
150
0.12
Adaptor block
Any
0.50
Chimney
213 x 213
0.02
Terminal
100 mm ridge
2.5
125 mm ridge
1.0
90
O
Bend
100 mm pipe
1.22 per
150 mm ridge
0.48
125 mm pipe
0.50 fitting
100 mm GCI
0.6
150 mm pipe
0.24
125 mm GCI
0.25
150 mm GCI
0.12
Table 2
Resistance factors for use in calculating equivalent heights
Fig. 7, PRINCIPAL DIMENSIONS (mm)
SIDE VIEW
PLAN VIEW
FRONT VIEW
BASE VIEW
KNOCKOUTS FOR
WATER CONNECTION
(BOTH SIDES)
GAS ENTRY
ELECTRICAL ENTRY
42.5
42.5
400
485
12
82
832
61
1
576
300
42
67
85
74
610
38
448
25
648
137
Ø125
33
3
127
18
0
41
1
40
1
85
30
25
243
37
37
5. INSTALLATION INSTRUCTIONS
Summary of Contents for 42-451-14
Page 24: ...www johnsonandstarley co uk 24 11 WIRING DIAGRAMS Fig 5a MODAIRFLOW CIRCUIT DIAGRAM...
Page 25: ...25 Sales Spares Replacement Help Line 01604 762881 Fig 5b Non MODAIRFLOW CIRCUIT DIAGRAM...
Page 26: ...www johnsonandstarley co uk 26 12 FUNCTIONAL DIAGRAMS Fig 6a Non MODAIRFLOW FUNCTIONAL DIAGRAM...
Page 27: ...27 Sales Spares Replacement Help Line 01604 762881 Fig 6b MODAIRFLOW FUNCTIONAL DIAGRAM...
Page 28: ...www johnsonandstarley co uk 28 13 DIMENSIONS Fig 7 HI SPEC J65 DIMENSIONS...
Page 29: ...29 Sales Spares Replacement Help Line 01604 762881 14 NOTES...