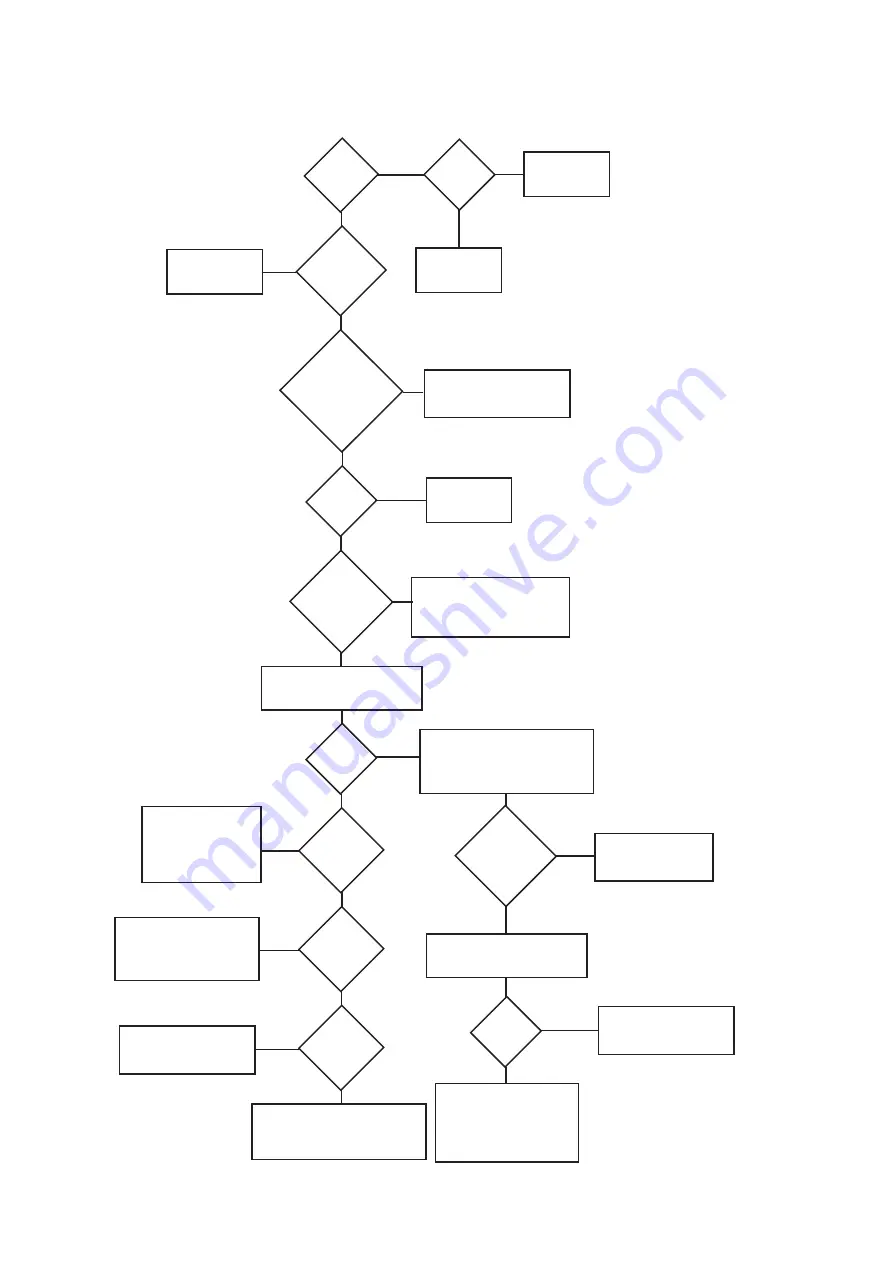
21
Sales/Spares & Replacement Help Line 01604 762881
12
17
8.3
BURNER AND CONTROL ASSEMBLY CLEANING:
8.3.1
Remove Burner and Controls Assembly as detailed in 8.2.
8.3.2
Clean burner thoroughly both inside and out with a soft brush.
DO NOT ENLARGE, DISTORT OR DAMAGE
BURNER HOLES
.
8.3.3
Reassemble in reverse order.
8.4
MAIN INJECTORS REMOVAL, CLEANING AND REPLACEMENT:
8.4.1
Remove the Burner and Controls assembly as details in 8.2
8.4.2
Unscrew the 2 x Main injectors, and 1 x cross lighter injector from their housings.
8.4.3
Clean as necessary.
DO NOT ENLARGE, DISTORT OR DAMAGE MAIN INJECTOR HOLES.
8.4.4
If the injectors are to be replaced, ensure that they are correctly marked, referring to the Data Badge for details.
8.4.5
Refitment or replacement of injectors in reverse order.
8.5
PILOT BURNER, THERMOCOUPLE AND ELECTRODE, REMOVAL AND REPLACEMENT:
8.5.1
Remove the Burner and Controls Assembly as detailed in 8.2
8.5.2
Disconnect the Igniter lead from the Piezo unit.
8.5.3
Disconnect the Thermocouple from the Thermocouple adapter on the Multifunctional Control, taking care to
avoid damage to the thermocouple capillary.
8.5.4
Release the Pilot Feed Pipe from the Multifunctional Control.
8.5.5
Remove 2 x 4mm screws securing the Pilot Burner assembly to the Burner arm, and withdraw the Pilot Burner
Assembly.
8.5.6 Release the Thermocouple securing nut from the Pilot Burner assembly and withdraw the Thermocouple, taking
care to avoid damage to the Thermocouple capillary.
8.5.7 Release the Electrode securing nut from the Pilot Burner assembly and withdraw the Electrode.
8.5.8 Release the Pilot Feed Pipe securing nut from the Pilot burner assembly and withdraw the Pilot Feed pipe and
Pilot Injector from the Pilot Burner assembly, and disconnect the Pilot Injector from the Pilot Feed Pipe hook.
8.5.9 Release 2 x 5mm screws securing the Pilot Burner Bracket to the Pilot Mounting bracket, and remove the Pilot
Burner Bracket.
8.5.10 Refitting or replacement is in reverse order.
NOTE: When refitting or replacing Thermocouple, tighten only to FINGER TIGHT + 1 FLAT.
8.6
MULTIFUNCTIONAL CONTROL REMOVAL:
8.6.1
Remove the Burner and Controls Assembly as detailed in 8.2
8.6.2
Disconnect the Thermocouple at the Multifunctional Control including adapter, avoiding damage to the capillary.
8.6.3
Disconnect the Pilot gas supply pipe from the Multifunctional control.
8.6.4
Disconnect the Multifunctional control input and output supply feeds.
8.6.5
Refitting or replacement is in reverse order.
8.7
PIEZO UNIT REMOVAL:
8.7.1
Disconnect 2 x conductors from Piezo unit.
8.7.2
Unscrew the Piezo retaining nut and remove the unit from its mounting bracket.
8.7.3
Refitting or replacement is in reverse order.
8.8
AIR CIRCULATING FAN, REMOVAL AND CLEANING:
8.8.1
Ensure that the electrical supply is isolated.
8.8.2
Remove the Air Filter and air heater cabinet doors.
8.8.3
Disconnect the Overheat limit device at the terminal block plug situated on the right hand side of the fan
chamber floor.
8.8.4 Disconnect the 230V connections (L/N/E) from the Fan Assembly.
8.8.5 Release the 2 x Fan Assembly securing screws and withdraw the Fan Assembly from the Heater cabinet.
8.8.6 Remove and discard the screw securing the Overheat limit device ‘P’ clip to the side of the Replacement Fan
Assembly, and discard the ‘P’ clip.
8.8.7 Remove the screw securing the Overheat limit device terminal block socket to the right hand side of the
Replacement Fan Assembly.
8.8.8 Refitting or replacement is in reverse order.
MAIN BURNER NOT OPERATING
IS
PILOT
LIT ?
IS 230V
SUPPLY
ON ?
IS TIME
CONTROL &
THERMISTA-STAT
CORRECTLY
SET ?
CHECK
TERMINAL
D9 IS
18V
CHECK
TERMINAL
C8 IS
230V
CHECK
TERMINAL
C10 IS
24V
REPLACE
ELECTRONIC
MODULE
IS
GAS
ON ?
N
TURN GAS
ON
N
LIGHT
PILOT
Y
Y
SWITCH ON
230 V
N
Y
N
Y
REPLACE
FUSE
N
Y
REPLACE
MULTIFUNCTIONAL
CONTROL
SET CONTROLS
CORRECTLY
Y
N
CHECK POLARITY OF
THERMISTA-STAT
CONNECTIONS
Y
IS
POLARITY
CORRECT ?
N
RECTIFY
DEFECT
Y
BRIDGE THERMISTA-STAT
TERMINALS AT HEATER
BRIDGE THERMISTA-STAT
TERMINALS AT HEATER
IS
BURNER
LIT ?
IS
BURNER
LIT ?
WIRING DEFECT
BETWEEN HEATER
&
THERMISTA-STAT
N
Y
N
N
Y
N
CHECK TTB,
LIMIT SWITCH
&
CONNECTIONS
Y
N
CHECK 230V I/P
& TIME CONTROL
OPERATION
REPLACE
THERMISTA-STAT
REPLACE
TRANSFORMER
Y
IS
FUSE
OK ?
CHECK
24V AT
MULTIFUNC-
TIONAL
CONTROL
Summary of Contents for 42-451-14
Page 24: ...www johnsonandstarley co uk 24 11 WIRING DIAGRAMS Fig 5a MODAIRFLOW CIRCUIT DIAGRAM...
Page 25: ...25 Sales Spares Replacement Help Line 01604 762881 Fig 5b Non MODAIRFLOW CIRCUIT DIAGRAM...
Page 26: ...www johnsonandstarley co uk 26 12 FUNCTIONAL DIAGRAMS Fig 6a Non MODAIRFLOW FUNCTIONAL DIAGRAM...
Page 27: ...27 Sales Spares Replacement Help Line 01604 762881 Fig 6b MODAIRFLOW FUNCTIONAL DIAGRAM...
Page 28: ...www johnsonandstarley co uk 28 13 DIMENSIONS Fig 7 HI SPEC J65 DIMENSIONS...
Page 29: ...29 Sales Spares Replacement Help Line 01604 762881 14 NOTES...