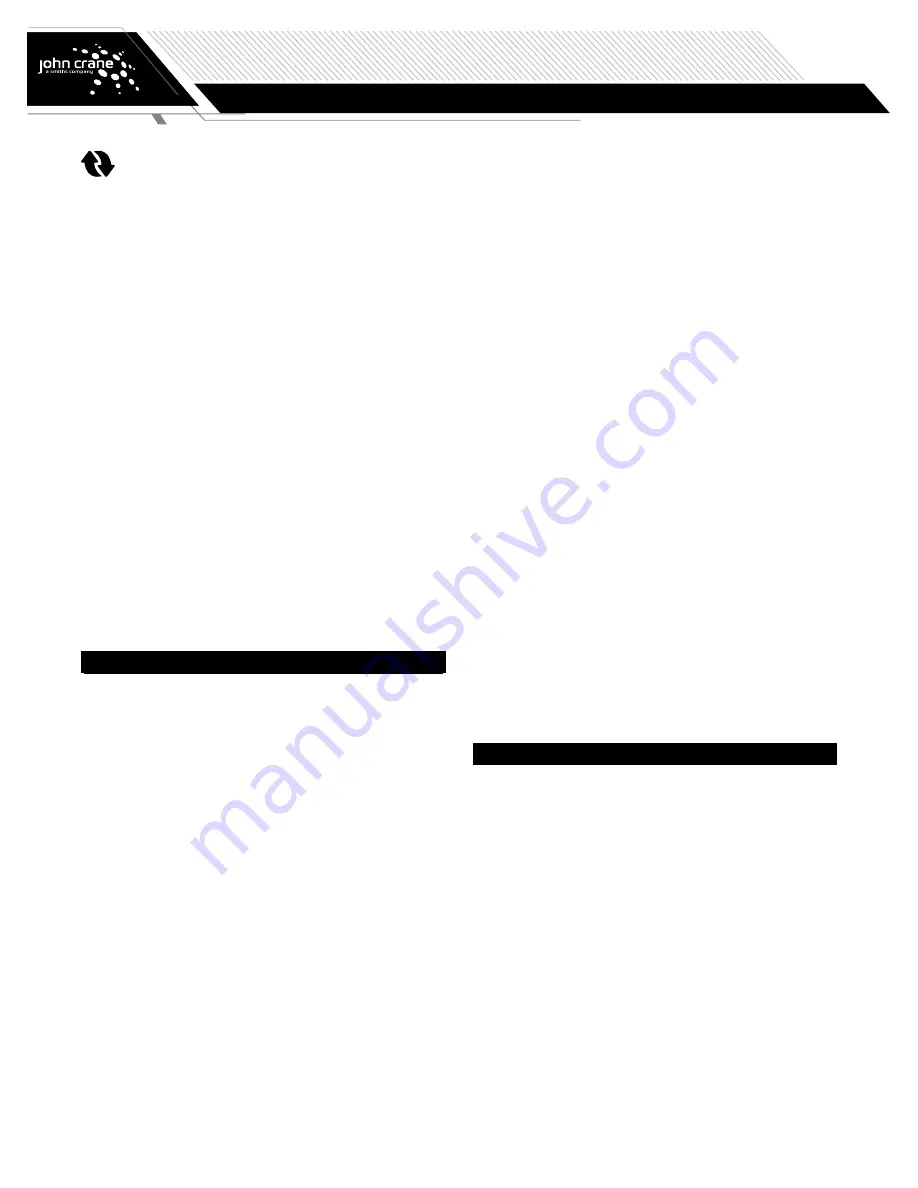
Installation, Operation & Maintenance Instructions
2
API PLAN 74 STEAM
SEAL SYSTEMS - STEAM
John Crane adopts the
‘Design For the Environment’ (DFE)
principle in making this product. Using this product will benefit
the environment
directly
by:
•
Reducing waste
of precious resources through decreasing
the risk of leakage and minimizing energy consumption
•
Preventing pollution
through controlling harmful
emissions to the atmosphere and ground contamination
•
Preserving valuable materials
through the use of high
quality durable materials.
2.3.2 Recycling
Product refurbishment
This product has been designed for long life.
Disposal
When the product is considered to be beyond economical repair and
potential reuse, it should be disposed of by
environmentally beneficial
means. The product can be disassembled with ease.
Scrapped components
These should be handled with extra care due to possible contamination.
They should be
recycled
through
local
industrial recycling plants.
Packaging
All packaging materials used are made from
recyclable
,
environmentally friendly materials.
When in doubt or for further information and advice on this subject,
please consult
John Crane
.
3. Transportation and Storage
Transport and store the system where possible in its original packaging.
It is necessary to protect and preserve the integrity of the equipment
between shipment and installation/start-up at site. This is particularly
important when extended periods of storage are envisaged.
Plan 74 Steam control panel systems may be shipped first to the rotating
equipment vendor to be mounted on the rotating equipment baseplate
complete with the connecting pipework. In this event follow the
instructions as given in the rotating equipment IOM.
Plan 74 Steam control panel systems, which are to be mounted off the
rotating equipment baseplate, shall be shipped directly to site and shall
be packed in suitable crates or cases to protect them from damage
during shipment. All openings to the system are closed and sealed for
shipping. In this event follow the following instructions.
On arrival at site and before unloading for storage, a visual inspection
of the crate/case should be carried out for signs of damage during
shipment. In the event of any damage the crate/case must be opened,
and the contents thoroughly examined for signs of equipment damage.
If any seals are broken, then the system is assumed to be contaminated
and shall be cleaned accordingly.
If the parts are considered acceptable with no visual signs of damage,
the crate/case should be properly closed again prior to storage.
After checking for shipment damage, the following recommendations
should be undertaken to prevent deterioration arising from long term
storage.
•
Plan 74 Steam control panel system should be replaced in their
original packaging and if possible the crate/case should be stored
away from direct sunlight, in a well-ventilated building with a hard
floor.
•
Temperature control is not normally necessary, but large temperature
fluctuations (>40°C/72°F) should be avoided.
•
If stored outdoors, it is recommended that the crate/case be placed on
square timber bearers resting on a concrete or similar hard surface.
•
The crate/case must then be wrapped with waterproof tarpaulin to
prevent ingress of water and dirt.
•
Loose components or accessories in the case should be stored as
above, after proper itemization.
•
A weekly visual external inspection of the protection and preservation
should be undertaken and any deficiencies noticed should be corrected
without delay.
•
The system must be stored far from backwater to avoid the MIC
phenomenon (microbial corrosion).
NOTE
Should water, condensation, sand, dirt or other contaminant
enter the system, through package/tarpaulin damage or
improperly positioned covers, the cause of the problem must
be eliminated and the equipment thoroughly dried and cleaned
before re-storing.
If used system parts are to be transported to the manufacturer or a third
party they have to be cleaned, decontaminated and require safe handling
instructions externally attached.
ATTENTION
The system normally does not require any preservatives;
it is resistant against most environmental conditions.
Ensure preservatives and cleaning agents do not affect
the elastomers.
4. Description of the System
4.1 Function of the system
Where rotating machines (pumps, fans or mixers) work with hazardous
fluids, it is common practice to install double mechanical seals which
prevent leakage of the process fluid escaping into the surrounding
environment.
Non contacting dry running gas seals are frequently used for this
purpose.
The barrier fluid is clean dry steam, constantly supplied to the
mechanical seal inter-space from a reliable source at a pressure greater
than 2 bar (30 psi) above the product pressure. The Plan 74 Steam
control panel is specifically designed for using steam as this barrier gas.
The Plan 74 Steam control panel must maintain the correct pressure for
the steam, and condition it to separate any condensate before delivery to
the seal, and prevent condensate forming within the seal.
The Plan 74 Steam control panel consists of two panels, one upstream
of the mechanical seal, and one downstream of the mechanical seal.
The upstream panel includes a separating chamber to ensure that the
steam supply to the seal is free of condensate particulates. A steam trap
is present at the lowest point of the panel to release any condensate
from the separation chamber. A check-valve between the upstream panel