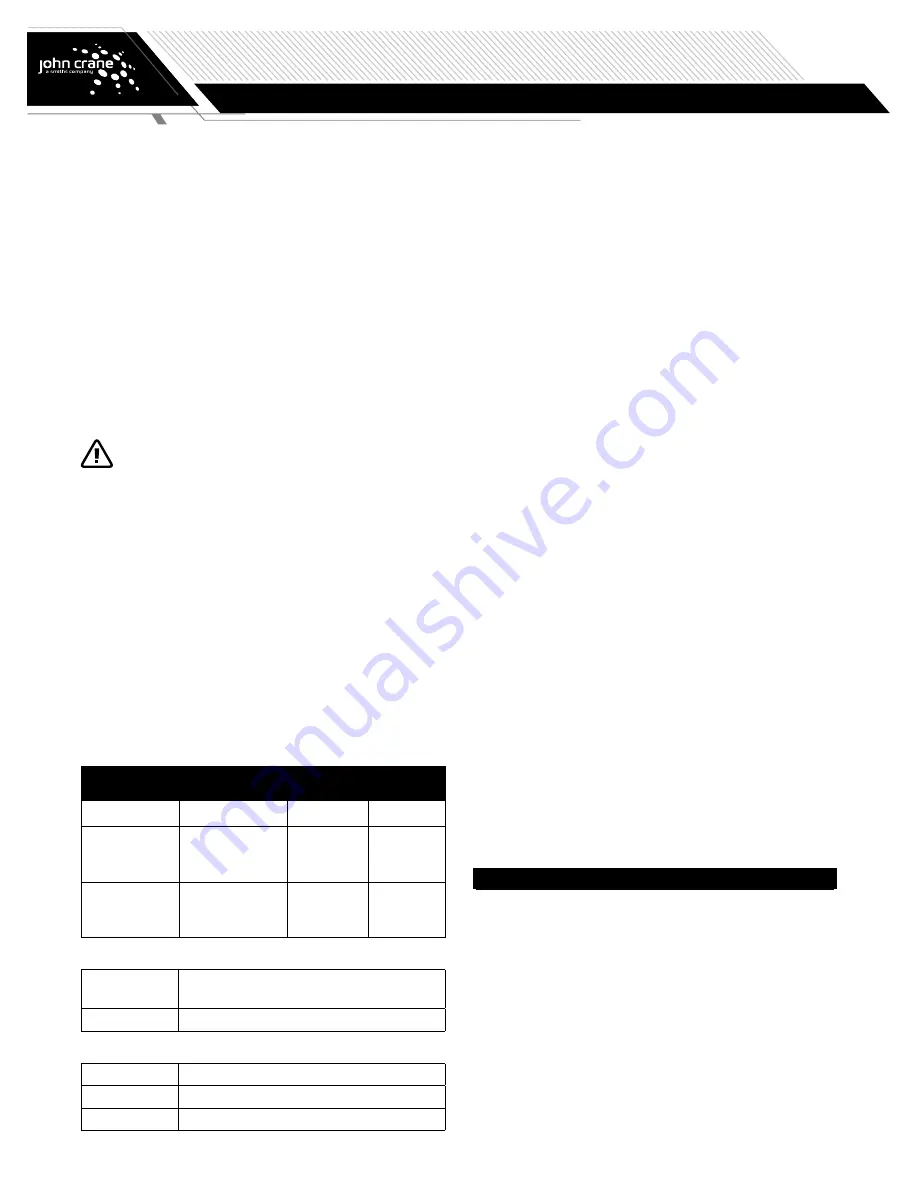
Installation, Operation & Maintenance Instructions
5
API PLAN 74 STEAM
SEAL SYSTEMS - STEAM
•
Check the condition of the steam traps (see Section 7.2).
•
Barrier pressure. Compare with the operating pressure on the
nameplate.
•
Condition of alarm signals (see Section 7.3)
7.2 Steam traps
Steam traps have a finite life, the duration of which is determined by the
quantity of condensate to be released from the system. If a steam trap
has reached the end of its life, it will no longer operate, and condensate
will begin to build up in the system.
To check the operation, visually check for signs that condensate is being
released, and then slightly crack open the manual steam drain valve. If
condensate is released, this indicates that the steam trap is no longer
operating and liquid is building up inside the system. The steam trap(s)
should then be replaced at the earliest opportunity.
While operating the manual drain, the system is
pressurized with high temperature steam. Correct PPE
must be worn, the drain must be directed to a safe
location for the release of hot steam, and the valve
should be opened by the absolute minimum to reduce
the quantity of steam released, for personnel safety,
and to prevent a loss of pressure in the Plan 74 Steam
control panel.
It is recommended that the steam traps are checked after the first month
of operation and thereafter at monthly intervals.
Irrespective of visual condition, it is recommended that the steam traps
are replaced annually.
7.3 Signals and alarms
The instrumentation on the system has the specific purpose of signalling
eventual malfunction of the mechanical seals. Possible alarm signals
indicating a malfunction are as shown in Table 2.
TABLE 2. Possible Alarm Signals Indicating a Malfunction
Effect
Instrument
Action
Cause
Falling Pressure
Pressure Gauge (PG)
or Pressure Indicating
Transmitter (PIT)
A
C to E
Low Pressure/
Shutdown Required
Pressure Indicating
Transmitter (PIT) or
Pressure Switch (PS)
B
C to E
Actions
A
Investigate cause and monitor to ensure values do not breach
safe limits
B
Shut down machine to prevent damage or loss of containment
Causes
C
Excessive leakage across the inboard seal or outboard seal
D
Pipe work/joint failure
E
Drop in the barrier gas supply pressure/flow
The signal from the pressure transmitter can be used either:
•
LOCALLY (with a Klaxon and/or beacon)
•
REMOTELY (in the control room)
Consult the specific instrument manufacturers manual should there be a
malfunction.
If necessary for safety, the alarm signals could be used as a
trip function.
7.4 Instrument maintenance
All instruments require regular calibration, following local processes
and regulations. See the supplier's instruction manual for and additional
instructions for maintenance of electrical instruments.
7.5 Spare parts
Spare parts must conform to the established technical specifications of the
manufacturer. This is guaranteed with John Crane spare parts.
You are advised to stock the most important wear parts on site.
The following data is necessary for spare part orders:
•
John Crane code/part number
•
John Crane order/ref no.
•
Part description
•
Quantity
7.6 Annual maintenance checks
Disconnection shall be made by plant person in charge of authorization.
Before any maintenance operation the system, the machine must be
stopped and depressurized, the barrier pressure must be fully discharged,
and the equipment allowed to cool to ambient temperature.
A suitable container should be available to contain any liquid drained
from the barrier system.
All parts requiring maintenance must be thoroughly decontaminated prior
to any work commencing.
All joints should be checked for tightness and signs of steam barrier
leakage. If present, all flange joints should be checked for tightness and,
if necessary, gaskets changed using replacements available from John
Crane.
8. Accompanying Documents
Installation Drawing (job specific) or Typical Drawing and Operational
Data Sheet.
A name and data plate is fitted to each Plan 74 Steam control panel.
It contains references and part numbers which must be quoted in any
communication.
For replacement parts please contact your local John Crane
office, quoting the system code number.