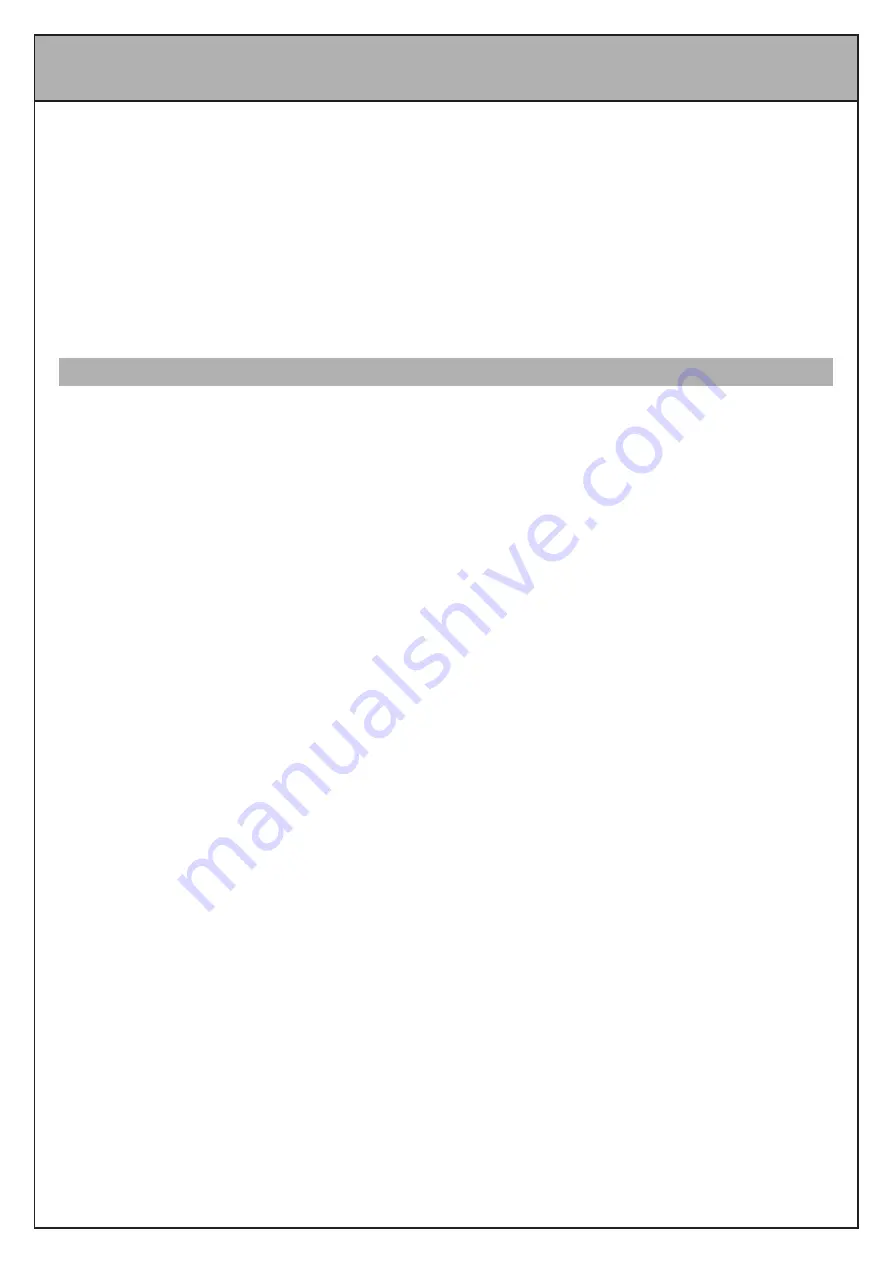
7
294000.10040 Rev A
SERVICE & MAINTENANCE
TOOLS REQUIRED
• 21mm A/F Spanner
(for the rear castors)
• 17mm A/F Spanner
(for the front castors)
• 19mm or ¾ inch A/F Spanner
(for the mast and support arm fixing bolts)
• 9/16 inch A/F S ¼ Hex Key
(for the mast/boom pivot bolt)
• 17mm A/F + 14mm Spanner
(for the sling/actuator retaining boss bolt)
• ½ inch A/F S 3/16 Hex Key
(for the mast end lift and leg actuator bolts)
• 4mm Hex Key
(for the screws on the handle bar base plate and all other fixings)
• 8mm Hex Key
(for the screws securing the loadcell to mast)
• Calibrated Torque Wrench
• Medium Strength Thread lock (BLUE) Type
SUPPORT ARM
1
The support arm is a two-piece assembly that is secured to the mast pivot by an arm pivot casting. The arm pivot casting is
secured to the end of the arm by two hexagon headed bolts.
2
Remove the grey plastic covers from the bottom of the support arm, the covers are a push on fit. Remove the covers by
gently levering a thin blade or screwdriver between the boom and the covers.
3
Check that the two M12 hexagon headed bolts, are
fully tightened to 15 Nm
.
4
Remove the end caps from the black sling retaining bosses on the arm to reveal securing set pin.
5
Check that the set pin is
fully tightened to 5 Nm
.
6
Examine the actuator mounting point. Without taking the mounting point apart check for signs of wear on the fulcrum pin.
Check for excessive vertical and horizontal movement in the mounting. This will give a good indication of wear but if there is any
doubt the assembly should be stripped down as follows:
7
Remove the set pin from the actuator bracket.
8
Examine the pin for signs of wear. The diameter of the fulcrum pin is 9.5mm. Reduction in diameter due to
wear must not
exceed 1mm
, before replacement.
9
Remove the outer sleeve bush from the support arm bracket and actuator top while holding the actuator, carefully lower the
actuator to the ground. (Take care not to loose the sling bosses and the sling retainers and nylon spacers on either side of the
actuator on the inside wall of the boom).
10
Examine the outer sleeve bush for wear
this should not exceed 1mm
.
11
Examine the actuator mounting on the support arm for wear on the bore of the bracket
this should not exceed 2mm
.
12
Examine the actuator top for wear
this should not exceed 1mm
.
13
Examine the split bushes for wear
this should not exceed 0.5mm
.
14
Reassemble the actuator to the boom bracket by replacing the sleeve, plastic washers, sling bosses and the sling retainers
set pin and nut.
15 Tighten the nyloc nut to 5 Nm
.
16
Replace the end caps for the sling bosses.