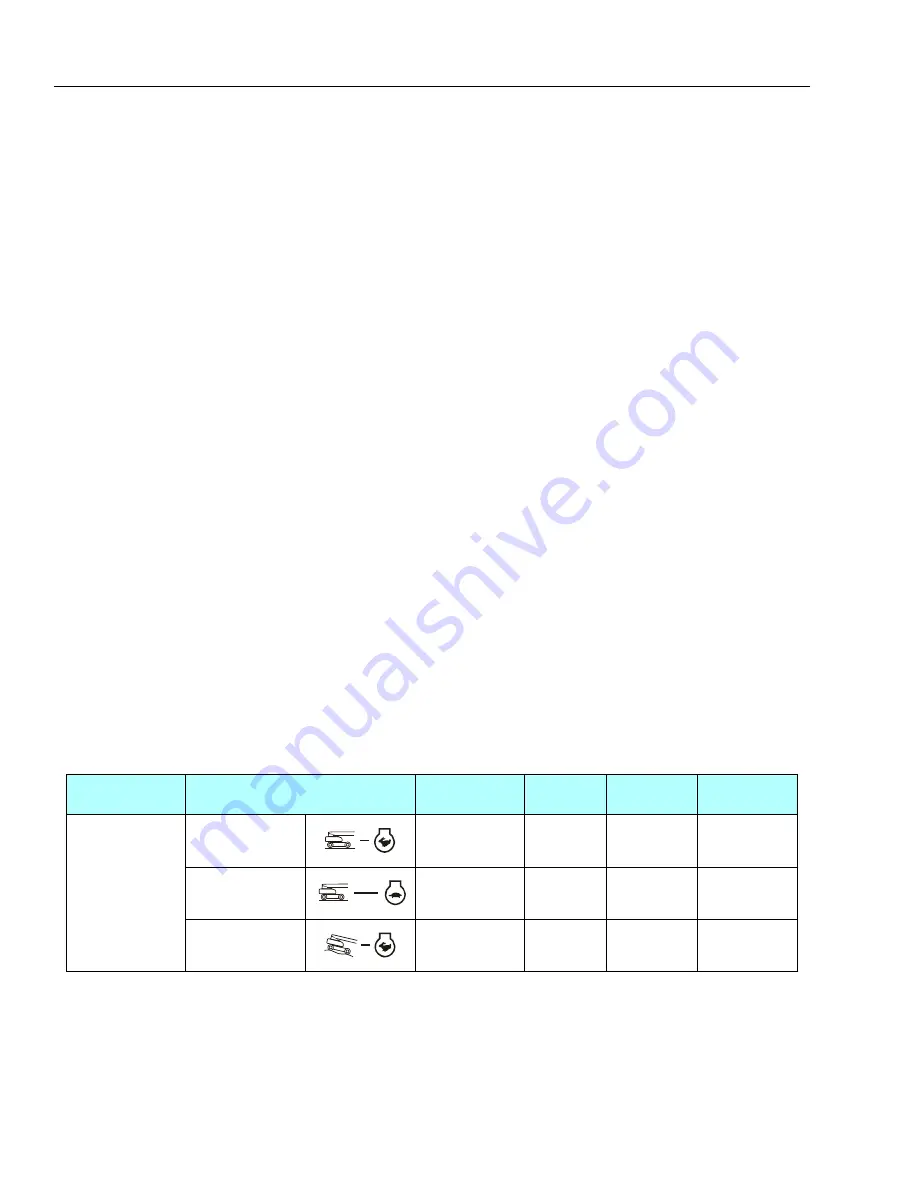
SECTION 3 - CHASSIS & TURNTABLE
3-2
– JLG Lift –
3121259
3.2
DRIVE ORIENTATION SYSTEM
The Drive Orientation System (DOS) is intended to indicate to
the operator conditions that could make the direction of
movement of the chassis different than the direction of move-
ment of the drive/steer control handle. The system indicates to
the operator the need to match the black and white direc-
tional arrows on the platform control panel to the arrows on
the chassis. The system uses a limit switch mounted on the
underside of the turntable, an indicator light and an override
switch on the platform display panel. The limit switch trips
when the turntable is swung +/- 42 degrees off center of the
normal driving position. This occurs approximately when the
boom is swung past a rear tire. When the turntable is in the
normal drive position with the boom between the rear tires,
no indications or interlocks are made. When the machine is
actively driving when the turntable is swung past the switch
point, the system is ignored until drive/steer is released. When
drive is initiated with the boom swung past the switch point,
the DOS indicator will flash and the drive/steer functions will
be disabled. The operator must engage the DOS override
switch to enable drive/steer (High Speed drive will remain dis-
abled). When the DOS is enabled, the DOS indicator will be
illuminated continuously and a 3-second enable timer will be
started and will continue for 3 seconds after the end of the last
drive/steer command. If the timer expires, the DOS override
switch must be re-engaged to enable drive/steer.
3.3
BEYOND TRANSPORT POSITION - DRIVE SPEED
CUTBACK SYSTEM
When the boom is positioned beyond the Transport Position
as described in the Transport Position Sensing System in Sec-
tion 4, the drive pump is automatically restricted to approxi-
mately 0.75 mph (1.2 kph). See Drive System in this section for
more detail on the drive speeds, and see Chassis Tilt Indicator
System in this section for interaction with the tilt sensor.
3.4
DRIVE/STEER - BOOM FUNCTION INTERLOCK
SYSTEM (CE ONLY)
The Drive/Steer - Boom Function Interlock System uses the
Transport Position Sensing System to sense when the boom is
out of the transport position. Drive and Boom functions are
simultaneously functional when the booms are within the
transport position, as on the standard machine. When the
boom is beyond the transport position, the control functions
are interlocked to prevent simultaneous operation of any
boom function with drive/steer functions. While operating
drive/steer functions the boom functions are inoperable, like-
wise, while operating boom functions drive/steer functions
are inoperable.
3.5
DRIVE SYSTEM
The Drive system consists of a variable displacement closed
loop pump, four low speed high torque orbital type motors,
directional control valves, and a series of flow dividers.
Drive Speed is controlled by a combination of engine RPM and
drive pump displacement. Traction and torque are controlled
through the flow divider system which is engaged or
bypassed depending on the drive mode selected. There are
three drive modes selectable at the platform control box, and
the functionality of the drive system is dependent on the posi-
tion of the boom (in or out of transport, see Transport Position
Sensing System in Section 4 and Beyond Transport Position -
Drive Cutback System in this section). The following chart
describes how the system works in each drive mode.
Table 3-2. Drive System Mode Chart
Boom Position
Drive Selection
Engine Speed when
Drive is Actuated
Drive Pump
Displacement
Flow
Dividers
Max. Speed
MPH (kph)
In Transport
Max Speed
High-3000 RPM
91%
Bypassed
3.1 (4.9)
Mid Engine
Mid-1800 RPM
58%
Engaged
0.96 (1.5)
Max Torque
High-3000 RPM
44%
Engaged
1.5 (2.4)
Summary of Contents for 340AJ
Page 1: ...Service and Maintenance Manual Model 340AJ P N 3121259 June 27 2017...
Page 2: ......
Page 10: ...vi JLG Lift 3121259 TABLE OF CONTENTS SECTION NO TITLE PAGE NO Thispageleftblankintentionally...
Page 15: ...3121259 JLG Lift xi LIST OF FIGURES FIGURE NO TITLE PAGE NO Thispageleftblankintentionally...
Page 18: ...xiv JLG Lift 3121259 LIST OF TABLES TABLE NO TITLE PAGE NO Thispageleftblankintentionally...
Page 42: ...SECTION 2 GENERAL 2 12 JLG Lift 3121259 NOTES...
Page 69: ...SECTION 3 CHASSIS TURNTABLE 3121259 JLG Lift 3 27 Figure 3 24 Bearing Pressing Tool...
Page 71: ...SECTION 3 CHASSIS TURNTABLE 3121259 JLG Lift 3 29 Figure 3 27 Bearing Nut Wrench...
Page 134: ...SECTION 3 CHASSIS TURNTABLE 3 92 JLG Lift 3121259 NOTES...
Page 157: ...SECTION 4 BOOM PLATFORM 3121259 JLG Lift 4 23 Figure 4 8 Rotator Counterbalance Valve...
Page 218: ...SECTION 5 HYDRAULICS 5 58 JLG Lift 3121259 Figure 5 32 Fasteners and Plugs Sheet 1 of 2...
Page 219: ...SECTION 5 HYDRAULICS 3121259 JLG Lift 5 59 Figure 5 33 Fasteners and Plugs Sheet 2 of 2...
Page 236: ...SECTION 5 HYDRAULICS 5 76 JLG Lift 3121259 Figure 5 39 Gear Pump Cutaway...
Page 246: ...SECTION 5 HYDRAULICS 5 86 JLG Lift 3121259 Figure 5 40 Oil Sampling Port...
Page 256: ...SECTION 6 JLG CONTROL SYSTEM 6 10 JLG Lift 3121259 Figure 6 3 Ground Module Sheet 1 of 4...
Page 273: ...SECTION 6 JLG CONTROL SYSTEM 3121259 JLG Lift 6 27 Figure 6 16 Analyzer Machine Setup Menu...
Page 274: ...SECTION 6 JLG CONTROL SYSTEM 6 28 JLG Lift 3121259 Figure 6 17 Analyzer Calibrations Menu...
Page 336: ...SECTION 6 JLG CONTROL SYSTEM 6 90 JLG Lift 3121259 NOTES...
Page 368: ...SECTION 7 BASIC ELECTRICAL INFORMATION SCHEMATICS 7 32 JLG Lift 3121259 NOTES...
Page 369: ......