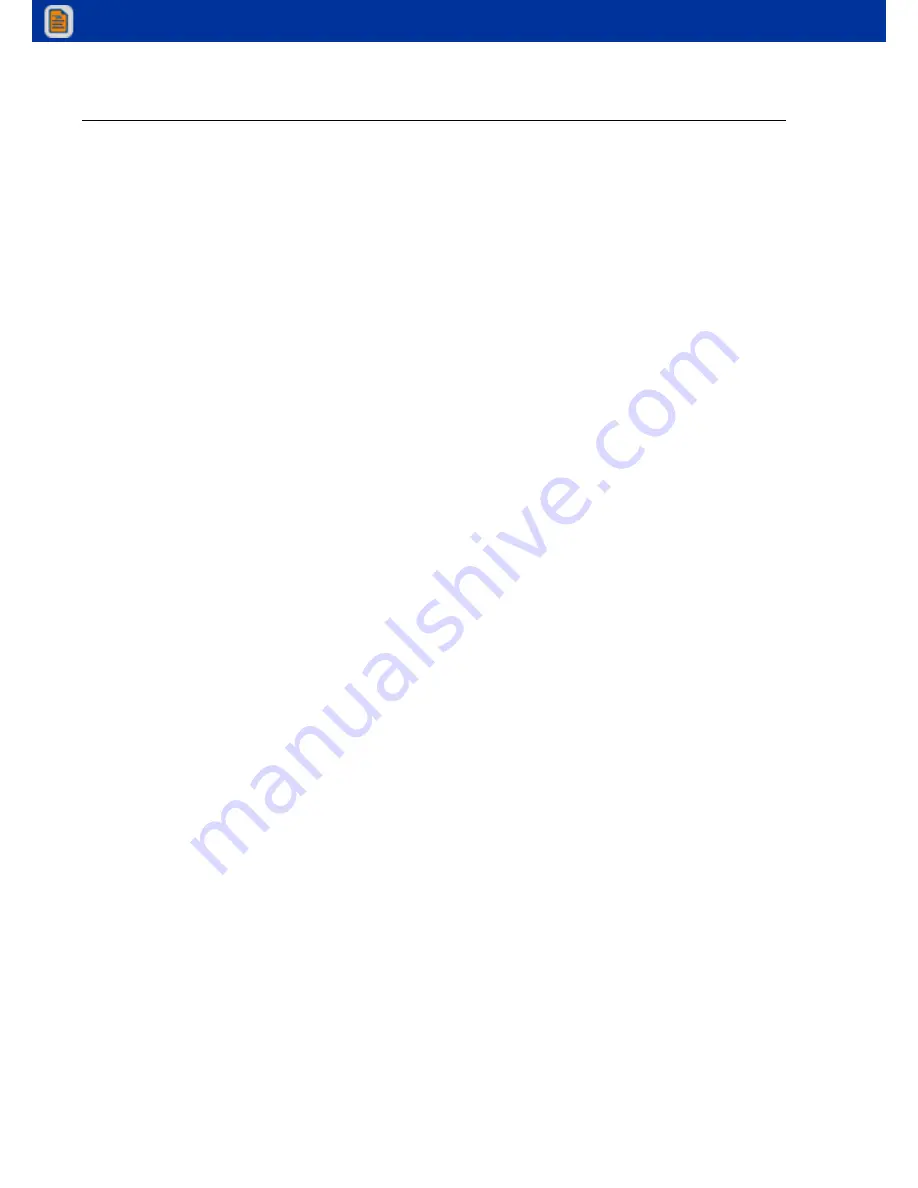
SECTION 2 - PROCEDURES
2-42
– JLG Lift –
3120686
a. Using a suitable hydraulic press, install bearing
cups (23 and 27) into hub (24).
b. Using the hydraulic press, install bearing cone
(28) onto output shaft (30).
c. Correctly position shaft (30) into hub (24) with
cone (28) in cup (27).
d. Using a suitable shaft support in the hydraulic
press, install bearing cone (22) on shaft (30)
until cone abuts bearing cup (23).
e. Position spacer shim (21) on shaft (30) between
retainer ring groove and bearing cone (22).
f. Using suitable snap ring pliers, install retaining
ring (20) on shaft (30).
g. Using the hydraulic press, install a new seal (29)
over shaft and into hub (24). Ensure that seal is
installed squarely.
h. Check that output shaft (30) rotates freely in the
hub. The oil seal will create a small amount of
drag. By tapping the outside of the shaft with a
soft headed mallet, any excessive tightness will
be reduced.
2.
If necessary, assemble planet carrier assembly (10)
as follows:
a. Apply a light coating of petroleum jelly or multi-
purpose grease to flanged surface of thrust
washers (12).
b. Position thrust washers (12) in carrier (10) with
tang in appropriate carrier cutaway portion.
Ensure that washers are flat against surface on
both sides of carrier.
c. Apply a liberal coating of petroleum or multi-pur-
pose grease to inner diameter of cluster gear
(11).
d. Position spacer (14) at the approximate midpoint
of the gear diameter.
e. On each side of spacer (14), position needle roll-
ers (13) in inner diameter of gear.
f. Position assembled cluster gear (11) into carrier
(10) between the two thrust washers (12).
Ensure that larger gear is on the roll pin side of
carrier.
g. Position planet shaft (15) into carrier hole, with
shaft roll pin hole on same side as carrier roll pin
hole.
h. Continue inserting shaft through thrust washers
(12) and cluster gear (11). Ensure that needle
rollers (13) are not displaced.
i.
Align roll pin holes in both shaft (15) and carrier
(10) with chamfered portion of shaft hole upper-
most.
j.
Position new roll pin (16) in hole in carrier (10)
and drive pin into hole until end of pin is flush
with carrier surface.
k. Repeat steps (a) through (j) for remaining two
cluster gears.
3.
Position internal gear (19) on inner end of output
shaft (30).
4.
Time carrier cluster gears as follows:
a. Place carrier assembly on a flat surface, posi-
tioning two top gears at ten o’clock and two
o’clock, and one bottom gear at six o’clock as
shown in Figure 2-8.
b. Find marked (punch mark) teeth on large gears.
Rotate gears until punch mark is located in a
straight up, 12 o’clock, position. Punch marks at
ten o’clock and two o’clock will be located just
under edge of carrier and not readily visible.
5.
Place ring gear (7) over cluster gears (11), with
raised shoulder of ring gear facing down.
6.
While holding ring gear (7) in position, invert carrier
assembly (10) so that ring gear and larger diameter
of cluster gears (11) are facing down.
7.
Apply a light coating of petroleum jelly or multi-pur-
pose grease to inner thrust washer (8) and thrust
bearing (9).
8.
Position thrust washer (8), thrust bearing (9), and
thrust washer (8) into applicable groove of carrier
assembly (10).
9.
Apply a light coating of petroleum jelly or multi-pur-
pose grease to new inner o-ring (6).
10.
Position o-ring (6) in groove in hub (24).
11.
While holding ring gear (7) and carrier assembly
(10), insert smaller diameter of cluster gears (11)
into internal gear (19).
12.
Rotate ring gear (7) until hole marked “X” is located
over hub shaft assembly (24).
13.
Insert input gear (18) into carrier assembly (10) so
that input gear and larger diameter of cluster gears
(11) are in mesh. Check that carrier assembly (10)
rotates freely.
14.
Position thrust washer (17) on shaft of input gear
(18).
15.
Apply a light coating of petroleum jelly or multi-pur-
pose grease to new outer o-ring (6).
16.
Position o-ring (6) into groove of cover (1).
17.
Apply a light coating of petroleum jelly or multi-pur-
pose grease to outer thrust washers (8) and thrust
bearing (9).
View thousands of Crane Specifications on FreeCraneSpecs.com
View thousands of Crane Specifications on FreeCraneSpecs.com