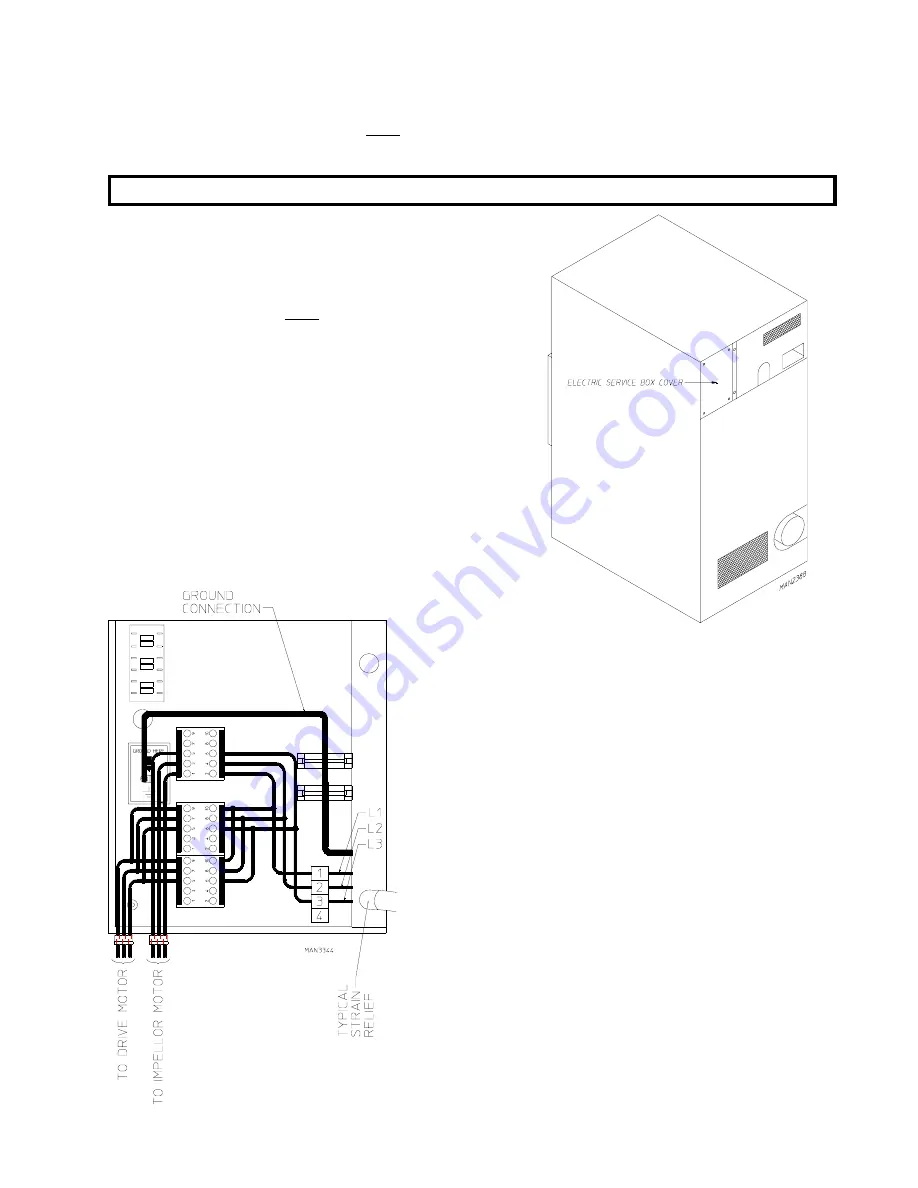
23
c. 3-Phase (3ø) Wiring Connections (hookup) - For Reversing Models Only
The electrical connections on
ALL
3-phase (3ø) gas model dryers are made into the rear service box
located at the upper left area of the dryer.
NOTE: A CIRCUIT SERVICING EACH DRYER MUST BE PROVIDED
.
If local codes permit, power to a gas dryer can be
made by the use of a flexible U.L. listed power cord/
pigtail (wire size
must conform
to rating of dryer), or
the dryer can be hard wired directly to the service
breaker panel. In
ALL
cases, a strain relief
must be
installed where the wiring enters the dryer.
The only electrical input connections to the dryer are
the 3-phase (3ø) power leads (L1, L2, L3, and
sometimes neutral) and ground. Single-phase (1ø)
power for the control circuit is done internally to the
dryer. No single-phase (1ø) input connection is
required on a 3-phase (3ø) dryer.
For gas model dryers manufactured for operation at 3-phase
(3ø), the electrical connections are made at the power
distribution block located in the service box at the rear, upper
left corner of the dryer. The ground connection is made to the
copper lug also provided in this box. To gain access to the
service box contactor, the service box cover
must be
removed.