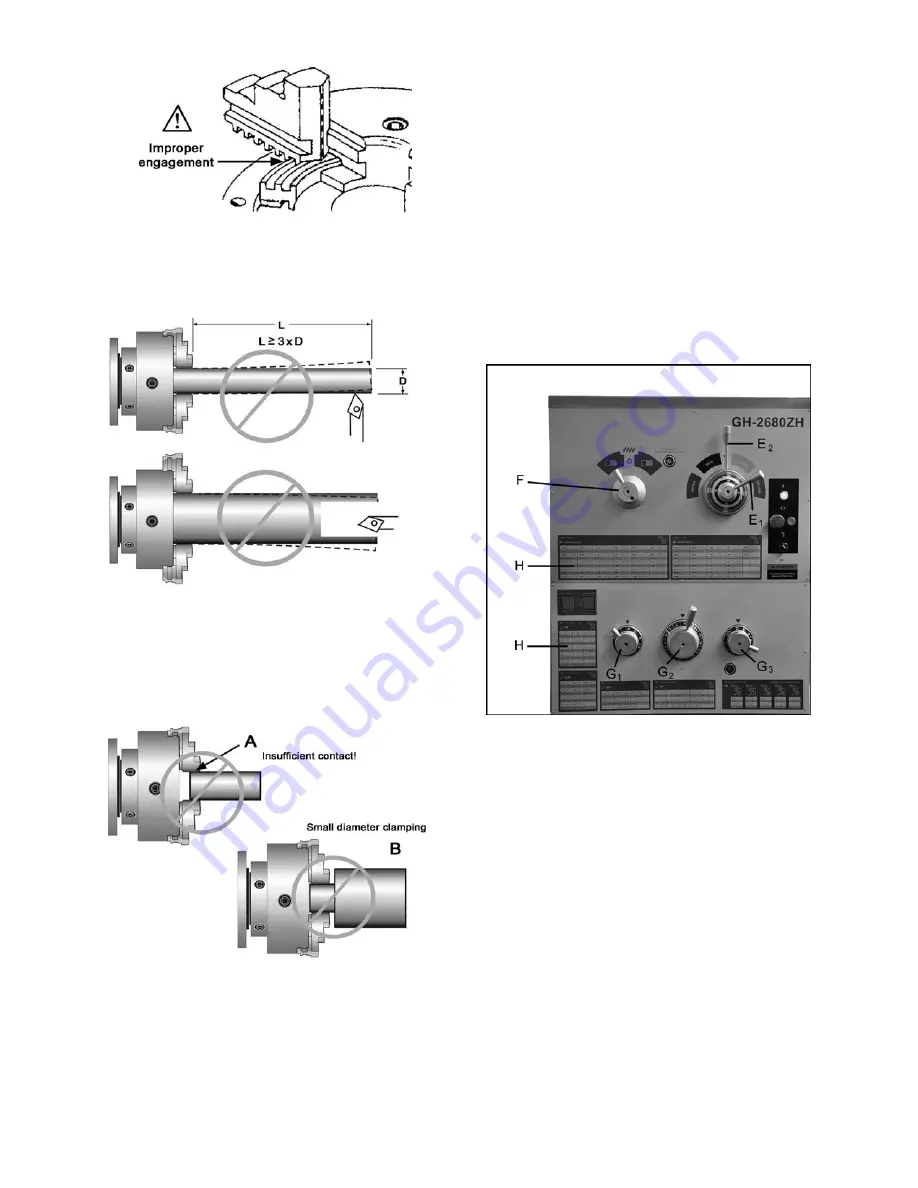
21
Figure 28 – Insufficient jaw tooth engagement
•
Avoid long workpiece extensions, as parts may
bend or fly off (see figure 29). Use rests or the
tailstock for support.
Figure 29 – Improper setups
•
Avoid short clamping contact (Figure 30, A) or
clamping on a minor part diameter (Figure 30,
B). Face-locate the workpiece for added
support.
Figure 30 – Improper setups
12.1
Tool Setup
The cutting angle is correct when the cutting edge
is in line with the center axis of the workpiece. Use
the point of the tailstock center as a gauge and
shims under the tool to obtain the correct center
height.
Use a minimum of two clamping screws to secure
each tool.
12.2
Spindle Speed
Twelve speeds are available by placing the first
speed lever (E
1
, Figure 31) in one of four positions,
and placing second lever (E
2
) in a position that
matches the color for the range you desire. These
selections are identified on the lever hub, as well
as in Table 6,
section 16.3
.
You may need to turn the chuck by hand to assist
engagement of the gears.
Never change speed while spindle is turning.
Figure 31
12.3
Feed and Thread Selection
To obtain various feed settings and thread pitches,
the four levers (F,G
1
,G
2
,G
3
) are used conjunctively.
1. Refer to the
Feed and Thread Chart
on the
front of the headstock (H, Figure 31). The
chart is also shown in
section 16.10
of this
manual.
2. Any gear changes should be made in
accordance with the chart.
3. Move levers (G
1
,G
2
,G
3
, Figure 31) to the
appropriate position according to the Feed and
Thread Chart.
TIP: When selecting feed/speed correlations,
remember the general principal that high speeds
complement fine feeding, and low speeds are
better for coarse feeding.
Summary of Contents for ZH Series
Page 34: ...34 18 0 Change Gear Diagram Figure 54...
Page 35: ...35 This page intentionally left blank...
Page 40: ...4 1 1 Bed Assembly I Exploded View...
Page 41: ...5 1 2 Bed Assembly I for 120 ZH only Exploded View...
Page 44: ...8 2 1 Bed Assembly II Exploded View...
Page 45: ...9 2 2 Bed Assembly II for 120 ZH only Exploded View...
Page 48: ...12 3 1 Headstock Assembly I Exploded View b b Z Z Z...
Page 51: ...15 4 1 Headstock Assembly II Exploded View...
Page 54: ...18 5 1 Headstock Assembly III Exploded View...
Page 56: ...20 6 1 Headstock Assembly IV Exploded View b...
Page 59: ...23 7 1 Headstock Assembly V Exploded View b...
Page 62: ...26 9 1 Gear Box Assembly I Exploded View...
Page 64: ...28 10 1 Gear Box Assembly II Exploded View...
Page 67: ...31 11 1 Gear Box Assembly III Exploded View...
Page 70: ...34 12 1 Brake Assembly Exploded View...
Page 72: ...36 13 1 Saddle and Cross Slide Assembly Exploded View...
Page 75: ...39 14 1 Tool Post and Compound Rest Assembly Exploded View...
Page 77: ...41 15 1 Apron Assembly I Exploded View...
Page 80: ...44 16 1 Apron Assembly II Exploded View...
Page 83: ...47 17 1 Apron Assembly III Exploded View...
Page 85: ...49 18 1 Apron Assembly IV Exploded View...
Page 87: ...51 19 1 Tailstock Assembly I Exploded View...
Page 89: ...53 20 1 Tailstock Assembly II Exploded View...
Page 91: ...55 21 1 Steady Rest Assembly Small and Large Exploded View...
Page 95: ...59 24 1 Travel Stop Assembly Exploded View...
Page 100: ...64 27 2 Electrical Diagram...