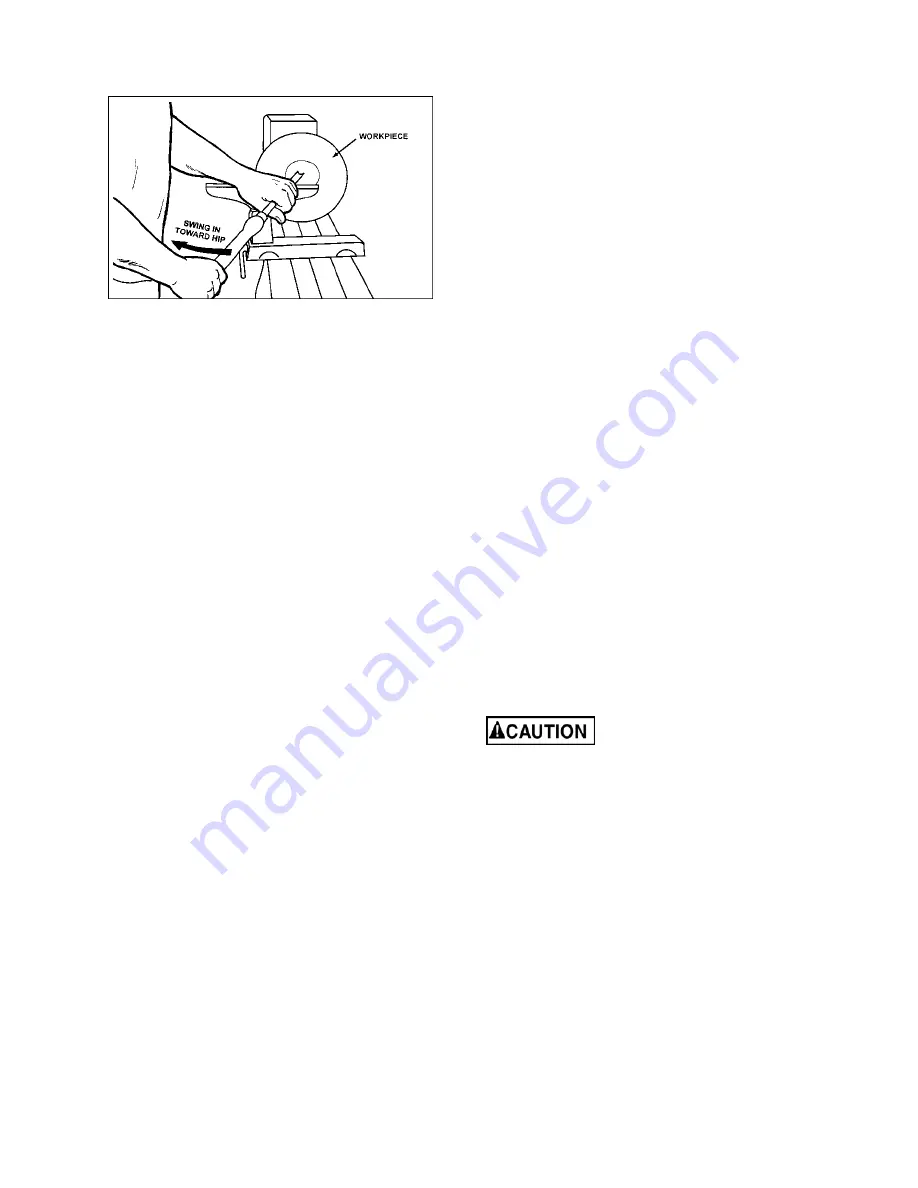
19
and pointed toward the four o'clock position, as
shown in Figure 28.
Figure 28
6. Use the left hand to control cutting edge of
gouge, while right hand swings tool handle
around toward your body (Figure 28). The flute
should start out facing top of workpiece, and
rotate upward as it moves deeper into the bowl
to maintain a clean even curve. As the tool
goes deeper into the bowl, progressively work
out toward the rim. It may be necessary to turn
the tool support into the piece as you get
deeper into the bowl.
(NOTE: Try to make one, very light continuous
movement from the rim to the bottom of the
bowl to ensure a clean, sweeping curve
through the piece. Should there be a few small
ridges left, a light cut with a large domed
scraper can even out the surface.)
7. Develop wall thickness at the rim and maintain
it as you work deeper into the bowl (Once the
piece is thin toward the bottom, you cannot
make it thinner at the rim). When the interior is
finished, move the tool support to exterior to
re-define bottom of bowl. (General rule of
thumb: the base should be approximately 1/3
the overall diameter of the bowl).
8. Work the tight area around faceplate or chuck
with 1/4" bowl gouge.
9. Begin the separation with a parting tool, but do
not cut all the way through yet.
Sanding and Finishing
1. Remove the tool support and adjust lathe
speed to approximately 500 RPM. High speed
can build friction while sanding and cause heat
check in some woods.
2. Begin with fine sandpaper (120 grit) and
progress through each grit, using only light
pressure. Coarser sandpaper tends to leave
deep scratches that are hard to eliminate. Use
power-sanding techniques to avoid concentric
sanding marks around your finished piece.
Avoid rounding over the rim and foot with
sandpaper; try to keep details crisp. Finish
sanding with 220 grit.
3. Remove sanding dust with tack rags or
compressed air and, with lathe turned off,
apply first coat of finish. Let stand for several
minutes, wipe off excess. Allow to dry before
sanding again with 320 or 400 grit sandpaper.
4. Turn lathe back on and continue the
separation cut almost all the way through the
base. Stop at about 3" and use a small fine
tooth saw to separate the bowl from the waste.
Apply second finish coat and allow to dry before
buffing.
12.0
Maintenance
12.1
General maintenance
Periodically inspect lathe for loose fasteners, worn
electrical cables, proper belt tension, belt wear, or
any other situation that might affect operation or
create a safety risk.
Wipe down the lathe after each use, and blow out
chips and dust using compressed air (
wear eye
and respiratory protection!
).
Periodically apply a light coat of oil to headstock
spindle, tailstock quill, bed surface, and tool rest
post. Protect the bed from rust by applying paste
wax or a commercially available rust protectant.
Bearings are permanently lubricated and sealed.
They do not require further lubrication.
12.2
Motor Brushes
Periodically inspect the two carbon brushes located
at each side of the motor. If brushes need
replacing, replace both at the same time.
A heavily worn or damaged
brush, if allowed to remain, may eventually
cause damage to internal motor elements.
1. Disconnect lathe from power.
2. Unscrew cap (Figure 29) using a screwdriver
or coin, and withdraw brush.
3. Inspect brush. Replace brush if any of the
following are seen: Brush is worn 1/4" (6mm)
or more, collapsed spring, broken lead in
spring, abnormal discoloration, signs of
breakage, burning or crumbling.
4. Reinsert brush, or install new one, and screw
in cap.
5. Repeat inspection for brush on opposite side
of motor.
Summary of Contents for JWL-1015
Page 8: ...8 6 1 Hole pattern JWL 1015 1015VS lathes Figure 2 Clearance hole spacing for mounting lathe ...
Page 26: ...26 16 2 1 JWL 1015VS Lathe Exploded View ...
Page 29: ...29 17 0 Electrical Connections JWL 1015 JWL 1015VS variable speed model LED Light MAX ...
Page 30: ...30 This page intentionally left blank ...
Page 31: ...31 This page intentionally left blank ...
Page 32: ...32 427 New Sanford Road LaVergne Tennessee 37086 Phone 800 274 6848 www jettools com ...