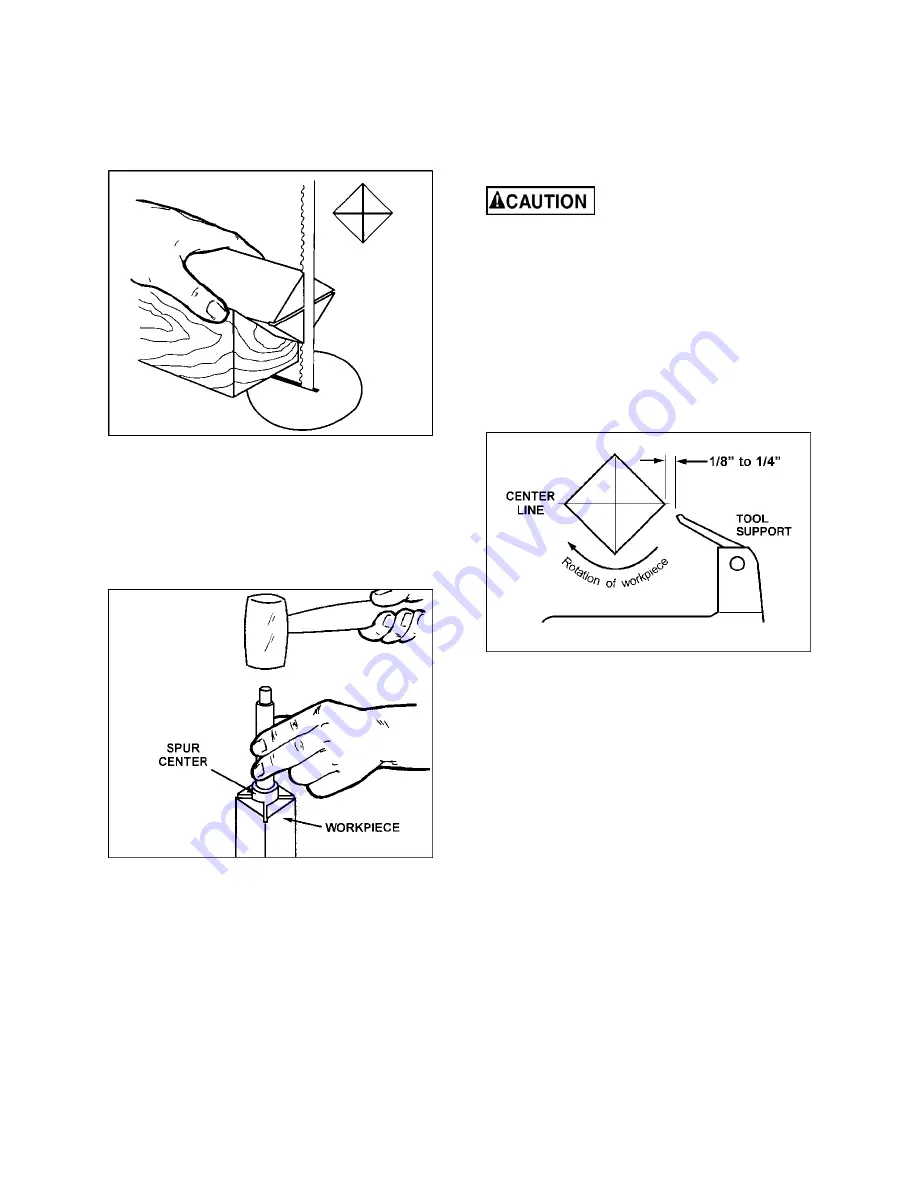
15
Put a dimple in the stock with an awl or nail, or
use a spring-loaded automatic center punch.
2. Extremely hard woods may require kerfs cut
into the ends of the stock (Figure 20) using a
band saw, so the wood will accept the spur
center and the live center.
Figure 20
3. Drive the spur center about 1/4” into the
workpiece, using a wood mallet or dead blow
hammer as shown in Figure 21. Be careful that
you do not split the workpiece.
Never use a
steel face hammer and never drive the
workpiece onto the spur center while it is
mounted in the lathe spindle.
Figure 21
4. Make sure the headstock is locked to the
Lathe bed.
5. Clean the tapered end of the spur center and
the inside of the headstock spindle.
6. Insert the tapered end of the spur center (with
the attached workpiece) into the headstock
spindle.
7. Support the workpiece while bringing the
tailstock into position about 1” away from the
end of the workpiece. Lock the tailstock to the
bed.
8. Advance the tailstock spindle with the
handwheel in order to seat the live center into
the workpiece. Use enough pressure to secure
the workpiece between the centers so that it
won’t fly off, but do not use excessive
pressure.
9. Tighten the spindle locking handle.
The tailstock ram is capable of
exerting excessive pressure against the
workpiece and the headstock. Apply only
sufficient force with the tailstock to hold the
workpiece securely in place. Excessive
pressure can overheat center bearings and
damage both workpiece and Lathe.
10. Move tool support into position. It should be
parallel to the workpiece, just below the
centerline and approximately 1/8" to 1/4" from
the corners of the workpiece to be turned, as
in Figure 22. Tighten support base to Lathe
bed.
Figure 22
11. Rotate workpiece by hand to check for proper
clearance.
12. Start lathe at lowest speed and bring it up to
the appropriate RPM for the size of workpiece
used. Consult the machine’s digital readout.
11.3.2
Cutting Techniques
Roughing Out
1. Begin with a large roughing gouge. Place the
tool on the tool support with the heel of the tool
on the surface to be cut.
2. Slowly and gently raise tool handle until cutting
edge comes into contact with the workpiece.
3. Beginning about 2” from the tailstock end of
the workpiece, roll the flute (hollowed-out
portion) of the tool in the direction of the cut.
See Figure 23. Make long sweeping cuts in a
continuous motion to rough the piece down to
a cylinder.
4. Keep as much of the bevel of the tool as
possible in contact with the workpiece to
ensure control and avoid catches. NOTE:
Summary of Contents for JWL-1015
Page 8: ...8 6 1 Hole pattern JWL 1015 1015VS lathes Figure 2 Clearance hole spacing for mounting lathe ...
Page 26: ...26 16 2 1 JWL 1015VS Lathe Exploded View ...
Page 29: ...29 17 0 Electrical Connections JWL 1015 JWL 1015VS variable speed model LED Light MAX ...
Page 30: ...30 This page intentionally left blank ...
Page 31: ...31 This page intentionally left blank ...
Page 32: ...32 427 New Sanford Road LaVergne Tennessee 37086 Phone 800 274 6848 www jettools com ...