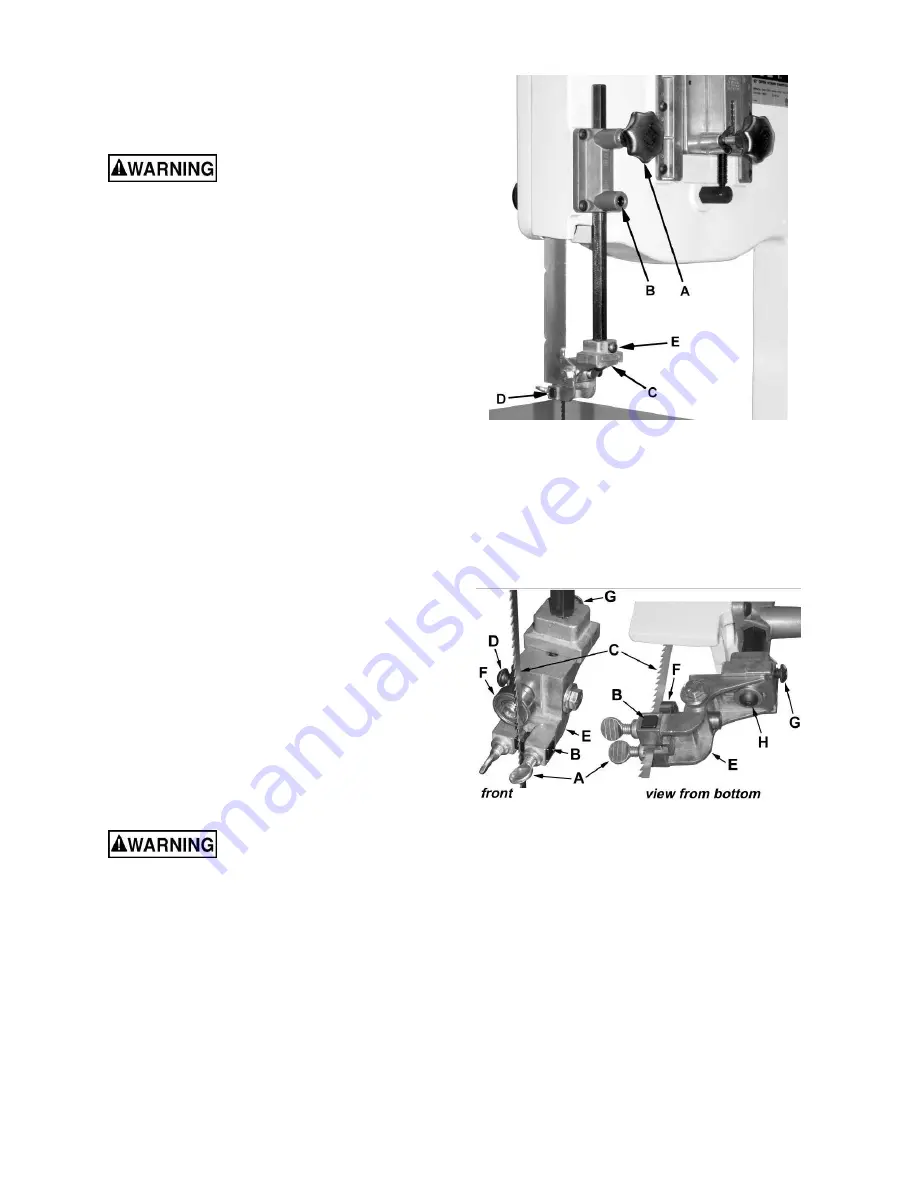
13
Upper Blade Guide Positioning
Refer to Figure 10. The blade guard has been
removed for clarity.
Never operate the Band Saw
without all guards in place and in working
order.
The upper blade guide assembly
should be
adjusted to just above the material being cut. To
adjust:
1. Disconnect machine from power source.
2. Loosen
lock knob
(A) and raise or lower the
upper
blade guide assembly
(C).
3. Tighten
lock knob
(A). Make sure blade
guide
blocks
(D) are still flat to the blade. If
adjustment is necessary, loosen
screw
(E) and
rotate the assembly until the
guide blocks
(D)
are flat to blade.
Upper Blade Guide Tension Adjustment
If the movement of the
blade guide assembly
seems “stiff” when being raised or lowered, it can
be adjusted to slide more easily. This is controlled
by an internal spring and ball that provides varying
degrees of resistance against the guide post.
To adjust tension on the spring:
1. Using a 5mm hex wrench (not provided), tight-
en or loosen the
setscrew
(B) until desired
tension is reached.
2. Reattach and tighten the
knob
(A).
Blade Guide Block Adjustment
This adjustment is the same for upper
and
lower
blade guides. Only the upper blade guide is shown.
Never operate the Band Saw
without all guards in place and in working
order.
Referring to Figure 11:
1. Disconnect machine from power source.
2. Remove the blade guard (upper blade guide
only).
Note:
Blade must already be tensioned and
tracking properly.
3. Loosen
thumbscrews
(A) and move the
guide
blocks
(B) as close to the
blade
(C) as possible
without pinching it.
Figure 10
Figure 11
4. Tighten
thumbscrews
(A).
5. Loosen
screw
(D) (4mm hex wrench) and
move the
guide block bracket
(E) in or out until
the front edge of the
guide blocks
(B) are just
behind the "gullets" of the saw teeth. Loosen
the screw (F) securing the
blade support
bearing
(G) if necessary.
6. Tighten
screw
(D).
7. Replace the blade guard.