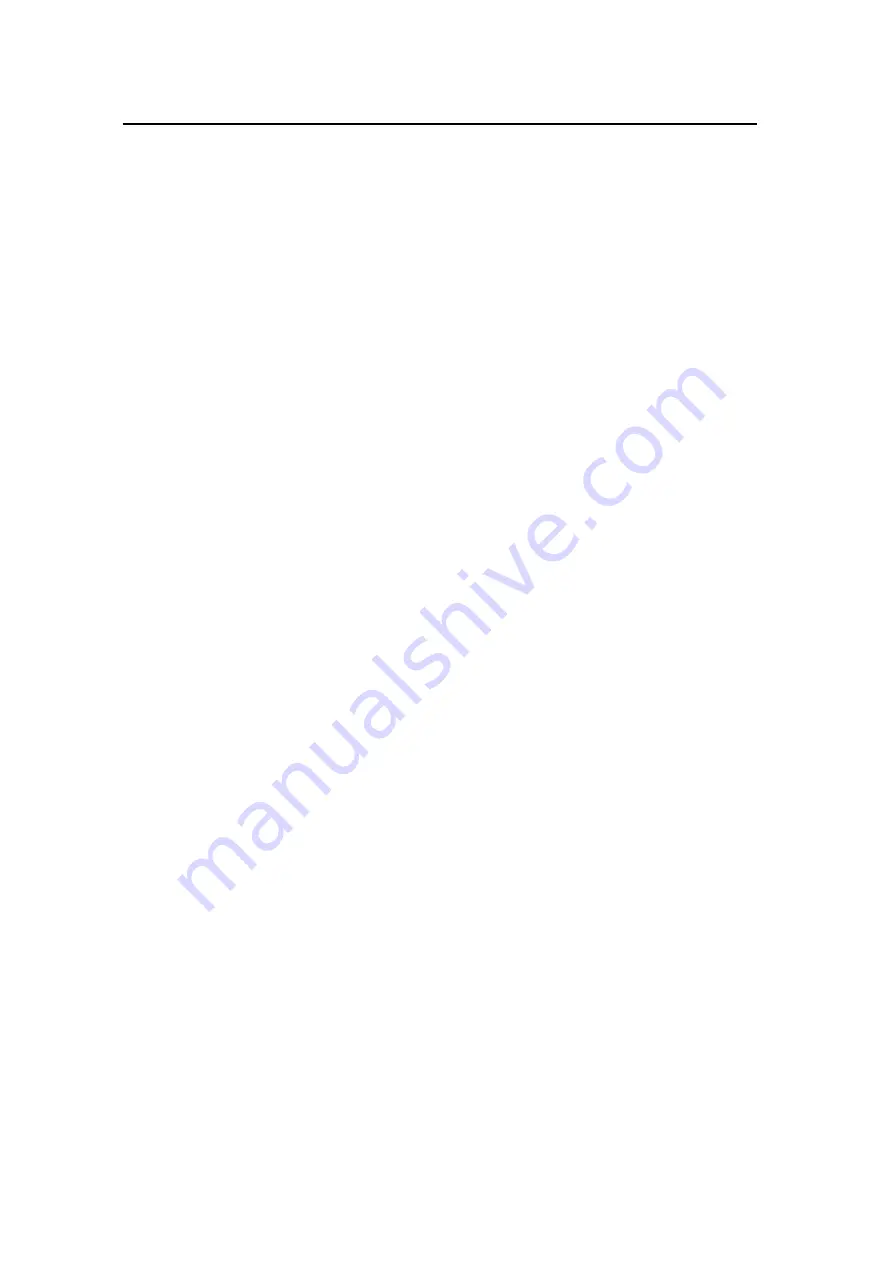
IMPORTANT SAFETY INSTRUCTION
READ ALL INSTRUCTIONS AND WARNINGS BEFORE USING THIS TOOL
Operator
COMMON SENSE AND CAUTION ARE FACTORS WHICH CANNOT BE BUILT INTO
ANY PRODUCT. THESE FACTORS MUST BE SUPPLIED BY THE OPERATOR.
PLEASE REMEMBER:
1. When using electric tools, machines or equipment, basic safety precautions should
always be followed to reduce the risk of fire, electric shock, and personal injury.
2. Keep work area clean. Cluttered areas invite injuries.
3. Consider work area conditions. Do not use machines or power tools in damp, wet, or
poorly lit locations. Do not expose equipment to rain, keep work area well lit. Do not
use tools in the presence of flam-mable gases or liquids.
4. Keep children away, all children should be kept away from the work area.
5. Guard against electric shock. Prevent body contact with grounded surfaces such as
pipes, radiators, ranges, and refrigerator enclosures.
6. Stay alert. Never operate if you are tired.
7. Do not operate the product if under the influence of alcohol or drugs. Read warning
labels on prescriptions to determine if your judgment or reflexes might be impaired.
8. Do not wear loose clothing or jewelry as they can be caught in moving parts.
9. Wear restrictive hair covering to contain long hair.
10.Use eye and ear protection. Always wear.
11. Keep proper footing and balance at all times.
12.Do not reach over or across running machines.
Before operations
1. Be sure the switch is OFF when not in use and before plugging in.
2. Do not attempt to use inappropriate attachments in an attempt to exceed the tool”s
capacity. Approved accessories are available from the dealer or machine maker.
3. Check for damaged parts, before using any tool, any part that appears damaged
should be carefully checked to determine that it will operate properly and perform its
intended function.
4. Check for alignment and binding of all moving parts, broken parts or mounting fixtures
and any other condition that may affect proper operation. Any part that is damaged
should be prop early repaired or replaced by a qualified technician.
5. Do not use the tool if any switch does not turn off and properly
Operation
1. Never force the tool or attachment to do the work of a larger industrial tool. It is
designed to do the job better and more safely at the rate for which it was intended.
2. Do not carry the tool by its power cord.
3. Always unplug the cord by the plug. Never yank the cord out of the wall.
4. Always turn off the machine before unplugging.
1
Summary of Contents for JMD-2S
Page 22: ...JMD 2S 1 230V 50Hz 19 ...