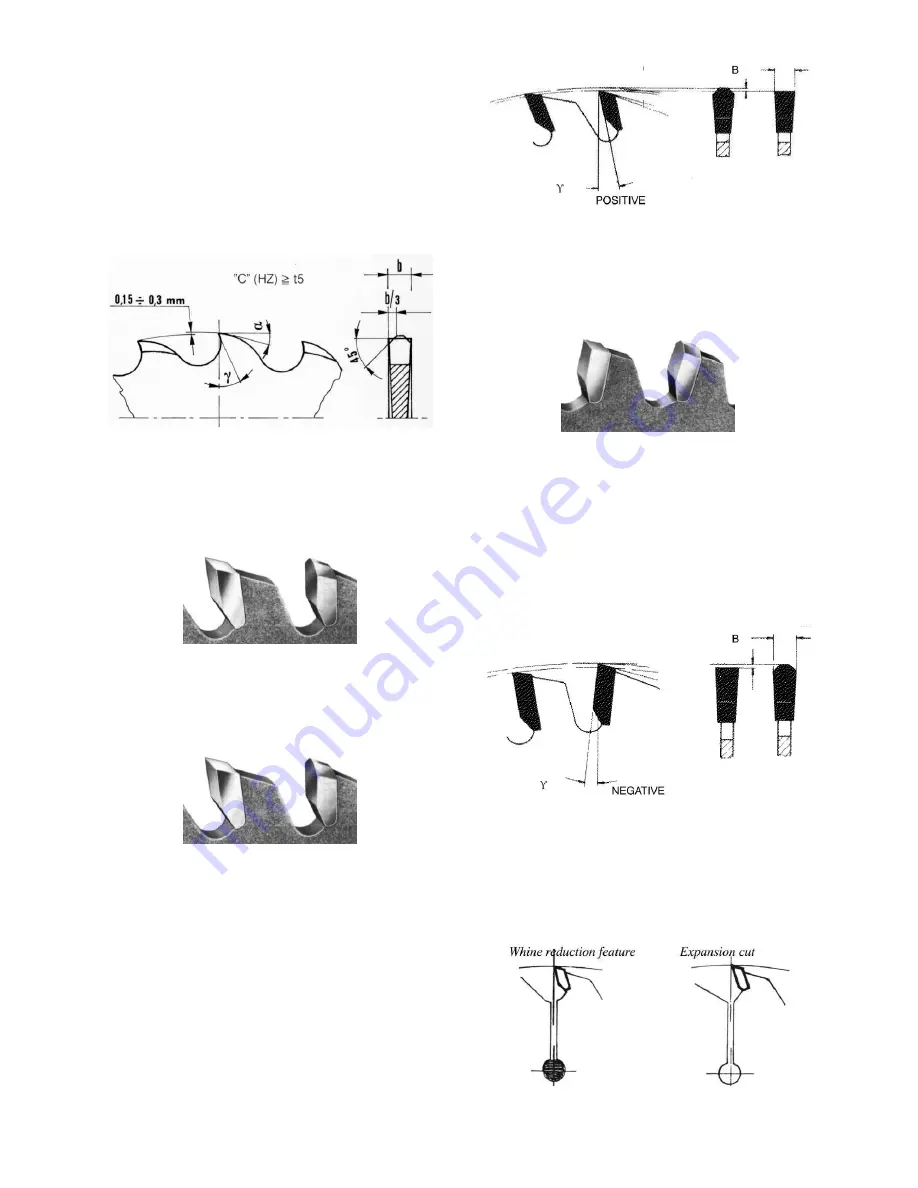
13
Teeth Shape
”C” TYPE SHARPENING (HZ)
Coarse toothing with roughing tooth raked on
both sides and non--raked finishing tooth – The
roughing tooth is about 0.3 mm higher.
Coarse toothing with roughing tooth and
finishing tooth – Used in saws with pitch greater
than or equal to 5 mm for cutting ferrous and
non-ferrous materials with solid or solid-profiled
sections.
Figure 16
”BW” TYPE SHARPENING DIN 1838--UNI 4014
Coarse toothing with teeth alternately raked to
the right and left – Toothing generally used on
cutting-off machines for cutting ferrous and alloy
materials with tubular and profiled sections.
Figure 17
POSITIVE AND NEGATIVE CUTTING ANGLES
The cutting angle
may vary from positive to
negative depending on the cutting speed, the
profile and the type of material to be cut.
Figure 18
A positive angle determines better penetration of
the tool and hence lower shear stress and
greater ease of sliding for the swarf over the
cutting edge. On the other hand, the cutting
edge has lower mechanical resistance, so as the
breaking load of the material to be cut increases,
the cutting angle decreases from positive until it
becomes negative so as to offer a cutting edge
with a larger resistant section.
Figure 19
Short swarf material such as brass, bronze,
aluminum and hard cast iron require smaller
cutting angles because the swarf becomes
crushed immediately and the rake angle has
little effect during the cutting stage.
Figure 20
The J-CK350 uses discs with positive cutting
angles for cutting solid materials and with
negative cutting angles for cutting hollow
profiles. This is because, as a result of the high
cutting speeds (3400 rpm), even with
non-ferrous materials the tool ”strikes” against
the wall of the profile to be cut several times,
thus requiring a cutting edge with a larger
resistant section.
Figure 21
Circular saws can also be characterized by other
parameters such as the whine reduction feature,
which cuts down noise at high speeds, or
expansion, which compensates for the pushing
of chips inside the cutting edge, thus reducing
the thrust on the walls of the material to be cut.
Figure 22
Summary of Contents for J-CK350-4
Page 17: ...17 15 1 2 Stand Assembly Exploded View...
Page 19: ...19 15 2 2 Head Assembly Exploded View...
Page 21: ...21 15 3 2 Base Assembly Exploded View...
Page 23: ...23 15 4 2 Manual Vise Assembly Exploded View...
Page 25: ...25 15 5 2 Guard Assembly Exploded View...
Page 27: ...27 15 6 2 CK350 Mist Coolant Assembly Exploded View...
Page 31: ...31 16 0 Wiring Diagram...
Page 32: ...32 427 New Sanford Road LaVergne Tennessee 37086 Phone 800 274 6848 www jettools com...