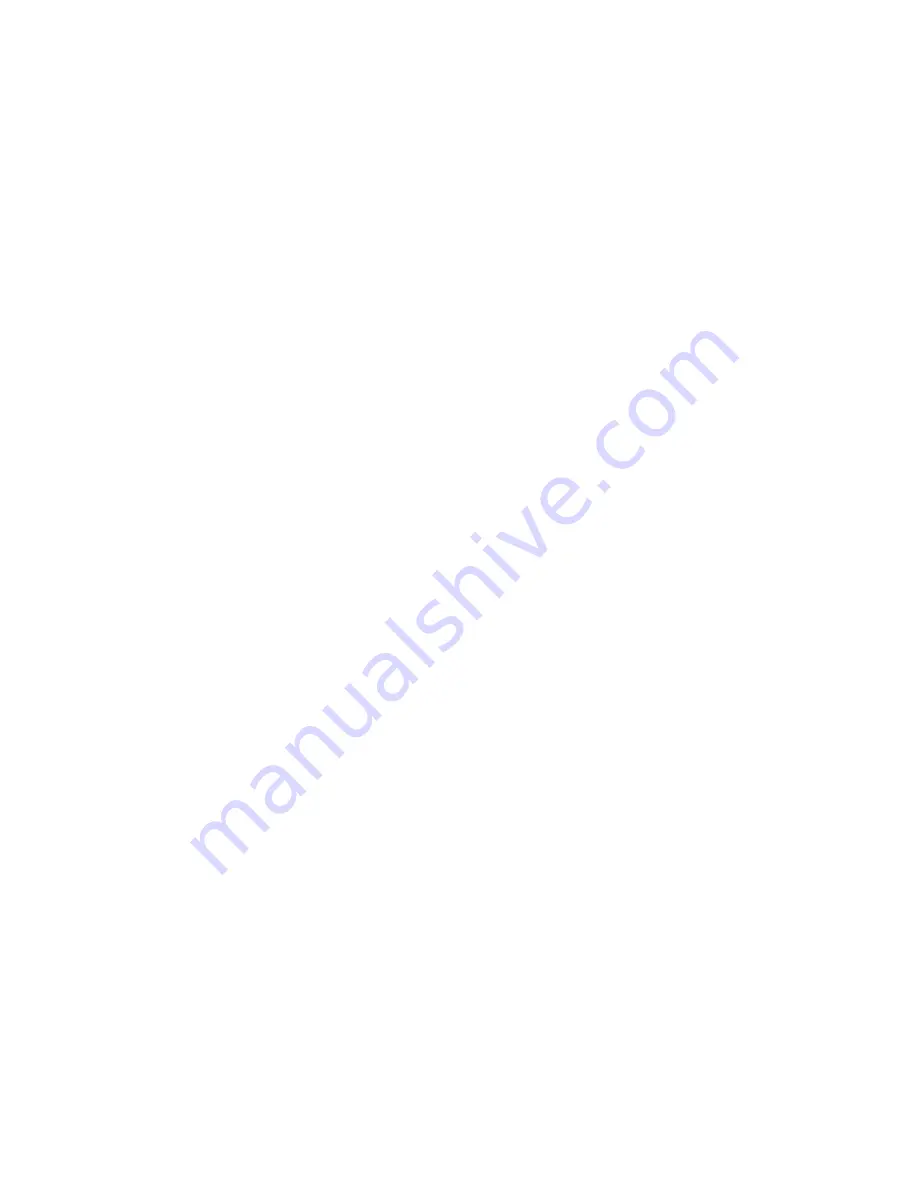
18
4. Manually turn fine feed handwheel. Quill and
spindle will move downward or upward
(depending upon which way you turn hand-
wheel and the direction the spindle is turning)
until you stop turning handwheel.
8.14
Tapping operations
1. Determine most efficient tapping speed
(spindle speed) by consulting appropriate
machinist's tables, the tap supplier, coolant
supplier and/or work piece supplier.
2. Make certain screw tap is mounted securely
within spindle.
3. Set feed rate control knob to “N” (neutral). See
sect. 8.9.
4. Turn on spindle motor. Also, turn on coolant
pump if coolant is being used.
5. Rotate feed levers slightly counterclockwise,
then move arm/spindle control lever to
SPDL.FOR.
6. Rotate feed lever to move tap into its pilot hole
until tap makes its initial thread cut and is
engaged in the work piece.
7. Allow tap to "self-feed" into pilot hole until it
has completed its tapping operation.
8. Move arm/spindle control lever to
neutral
position and allow spindle to stop completely.
9. Move arm/spindle control lever to SPDL.REV
until tap withdraws completely from hole.
10. Move arm/spindle control lever to neutral.
8.15
Power ON/OFF
If your J-720R was connected to its service branch
correctly, there will be a service disconnect with an
external power cutoff lever or switch which
disconnects the drill press from the service branch.
This is your ultimate protection against accidental
machine start-up when clamping work pieces or
inserting and removing tooling. Always be certain
you have turned off power at this disconnect before
beginning such procedures.
8.16
Power ON light
Whenever machine is receiving electrical power,
the indicator light on the switch box (Figure 7-1)
will
be illuminated.
8.17
Coolant control
The flood coolant system is controlled by the
switch on front of switch box (Figure 7-1). If coolant
has been turned on, but does not flow, check pump
rotation by observing the pump shaft. It should be
rotating in the direction of arrow on pump casting. If
rotation is incorrect, see
sect. 6.4.3.
Open coolant valve at rear of machine (#27, Figure
5-2). The nozzle can be adjusted to any angle
above the work piece.
8.18
Spindle motor controls
Power to spindle motor is controlled as follows:
1. Cutout box control lever must be in ON
position.
2. Motor speed control switch must be in either
HI or LOW position.
3. Emergency Stop button must be disengaged
(rotate clockwise).
4. Arm/spindle control lever must be engaged for
selected rotation. See
sect. 8.21
.
8.19
Turning off spindle drive
To turn power OFF to spindle drive motor, do one
of the following:
1. Put arm/spindle control lever in neutral, or
2. Push red E-Stop button, or
3. When servicing tooling or other machine
components, put service disconnect lever in
OFF position.
Once E-stop has been pushed (item #2 above)
none of the other switches on the panel can be
used to control power to spindle drive motor or
coolant pump, until E-stop has been reset (rotate
button clockwise until it disengages).
8.20
Using load ammeter
An ammeter on the switch box is used to monitor
the load on the spindle drive motor. It is connected
into one of the three power lines which supply the
main spindle motor.
When the drive motor is ON and up to speed, and
there is no tooling being used to drill, tap or bore a
hole, the ammeter should read approximately 2.5
amps. If it exceeds this value there is a problem
internally (such as lack of lubrication in the
gearboxes, bad bearings, etc.). You should turn off
the machine and determine the cause of any
excessive free-running load.
Monitor the ammeter during machining operations.
The ammeter should stay below 9 amps of current
draw during machining. You should adjust spindle
speed, feed rate and coolant use to maintain full
load current draw below the 9 amp value.
If you exceed 9 amps current draw a thermal
overload switch in the electrical control panel will
trip. If this occurs, locate and reset the thermal
switch.
Summary of Contents for J-720R
Page 9: ...9 General Features and Terminology cont Figure 5 2 ...
Page 14: ...14 7 0 Operating Controls J720R Figure 7 1 Operating Controls ...
Page 23: ...23 Figure 12 1 Figure 12 2 Figure 12 3 Figure 12 4 Figure 12 5 ...
Page 27: ...27 13 3 1 Base Column and Arm Assemblies Exploded View ...
Page 30: ...30 13 4 1 Gear Box Assembly Exploded View ...
Page 34: ...34 13 5 1 Rear Gear Box Assembly I Exploded View ...
Page 35: ...35 13 5 2 Rear Gear Box Assembly II Exploded View ...