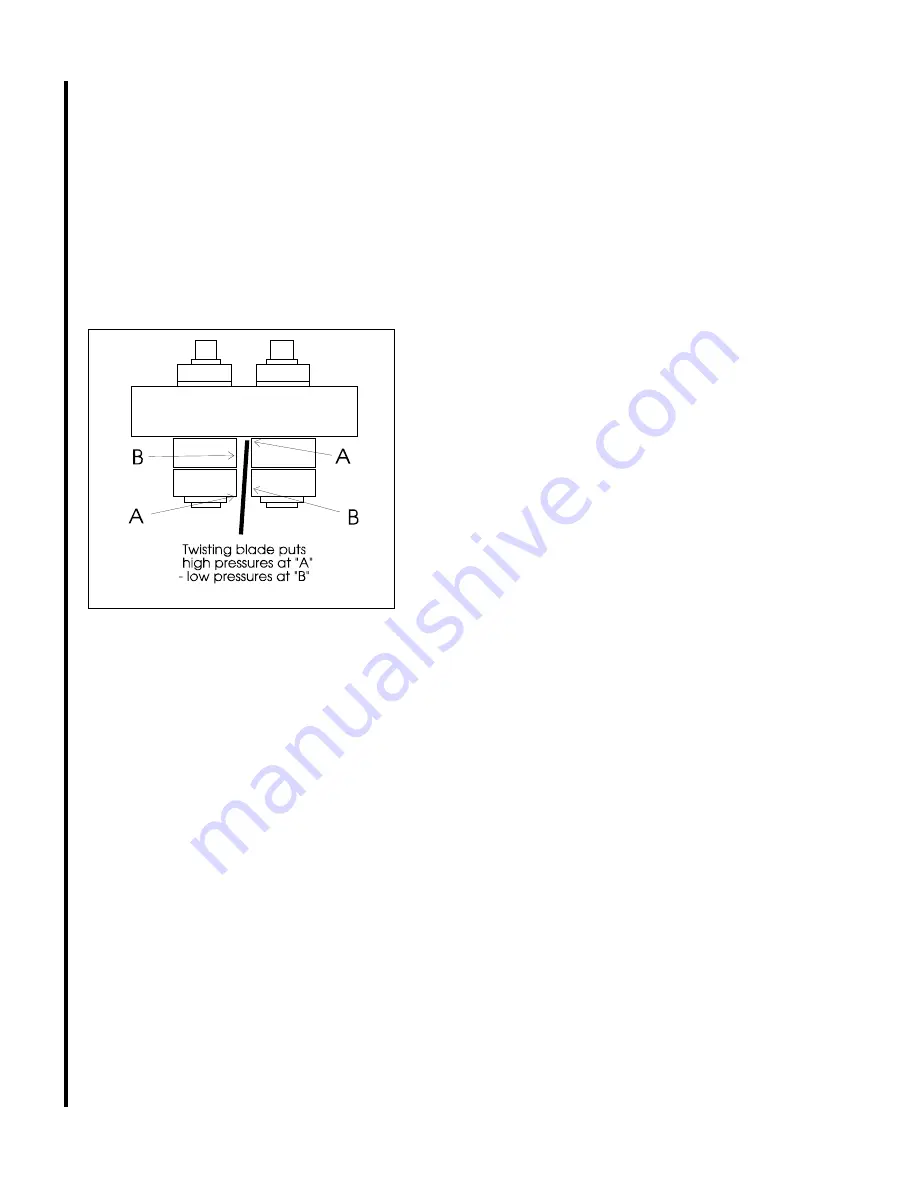
18
Adjusting guide bearings
There are eight side blade guide/support bearings.
These bearings are installed in the bearing seat, and the
seat is attached to the sliding adjustment bracket.
These bearings are stacked, with
two
bearings on
each adjustment eccentric. The width of each pair of
stacked bearings is slightly less than the width of a blade.
The force against each of the bearings in each
stack is not equal. This is because the bearings are
twisting the blade. This puts a much higher force against
the two bearings which are doing most of the twisting.
Look at
Figure 15
for a diagram which shows this effect.
Figure 15: Guide bearing forces. Blade twist and clear-
ance is exaggerated for demonstration. In practice, the
blade will be standing vertical between the bearings when
they are adjusted correctly.
The bearings are adjusted by moving the eccentrics
as required, and by using your fingers to twist the bear-
ings to see if they can rotate, and how difficult it is to
rotate them.
The bearing clearance is correctly adjusted when
the bearings labeled with an "A" in
Figure 15
cannot be
turned at all, and when bearings labeled with a "B" in
Figure 15
can
barely
be turned with your fingers.
If the supporting bearings don't turn at all -- the set-
up is too tight. If they can be turned easily using your
thumb and forefinger -- the set-up is too loose.
To adjust:
1. Put a wrench on the adjustment tang of the bearing set
you want to adjust. This prevents the eccentric from
turning.
2. Use another wrench to loosen the lock nut for the
eccentric bolt.
3. Turn the eccentric using the adjustment tang to loosen
or tighten the bearing set, as needed.
4. Tighten the jam nut.
5. Check bearing tightness on both sides of the blade.
Re-adjust as required until the conditions described in the
above paragraphs is obtained.
Replacing guide bearings
1. Remove the blade as outlined in steps 1
through 6 of
Replacing blades
.
2. Remove the jam nut on the eccentric upon which you
are going to replace bearings.
3. Remove the clip which secures the bearings on the
eccentric shaft.
4. Tap the old bearings off and press the new bearings
on.
5. Replace the snap ring which secures the bearings on
the eccentric.
6. Reinstall the eccentric in its position and tighten the
jam nut loosely on the eccentric.
7. Install the blade according to instructions 7
through 14
in
Replacing blades
.
8. Adjust bearing clearance according to instructions in
the previous section:
Adjusting guide bearings
.
Adjusting blade
back-up bearings
The back-up bearings support the rear of the saw
blade as it takes the pressure of cutting. (Refer to
Figure 11
.)
1. Being careful not to disturb the vertical angle of the
guide bearing seat, loosen the socket head cap screw
which secures the seat.
2. Move the seat downward until the back-up bearing just
barely touches the back of the blade.
3. Tighten the socket head cap screw securely.
4. Perform this same operation on the other back-up
bearing, if required.
After adjusting the back-up bearings, CHECK FOR
BLADE VERTICAL according instructions in
Adjusting
blade vertical
. It is very easy to disturb the vertical plane
of the blade while performing this adjustment, and a blade
which is not vertical will NOT cut straight.