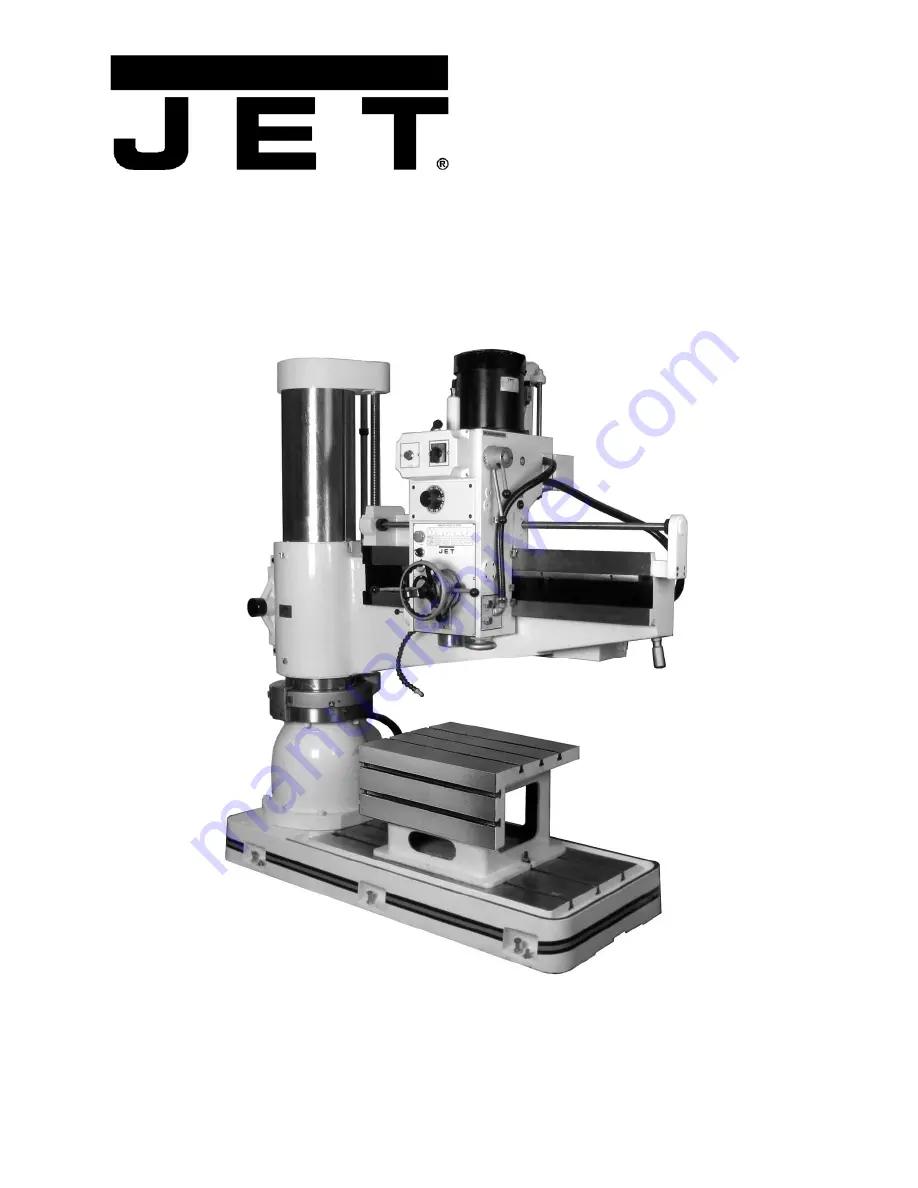
1
Operating Instructions and Parts Manual
4-ft. Radial Arm Drill Press
Models J-1230R, J-1230R-4
WALTER MEIER (Manufacturing) Inc.
427 New Sanford Road
LaVergne, Tennessee 37086
Part No. M-320036
Ph.: 800-274-6848
Revision B
07/2011
www.waltermeier.com
Copyright © 2011 Walter Meier (Manufacturing) Inc.
Summary of Contents for J-1230R
Page 11: ...11 General Features and Terminology cont Figure 4 Figure 5 ...
Page 16: ...16 7 0 Operating Controls Figure 10 Operating Controls ...
Page 27: ...27 Figure 17 Figure 18 Figure 19 Figure 20 Figure 21 ...
Page 30: ...30 13 2 1 Column and Base Exploded View ...
Page 32: ...32 13 3 1 Arm Front Exploded View ...
Page 34: ...34 13 4 1 Arm Rear and Clamping Gearbox Exploded View ...
Page 38: ...38 13 6 1 Gearbox Assembly Head Exploded View ...
Page 42: ...42 13 7 1 Rear of Head I Exploded View ...
Page 45: ...45 14 0 Electrical Connections for J 1230R ...
Page 47: ...47 ...