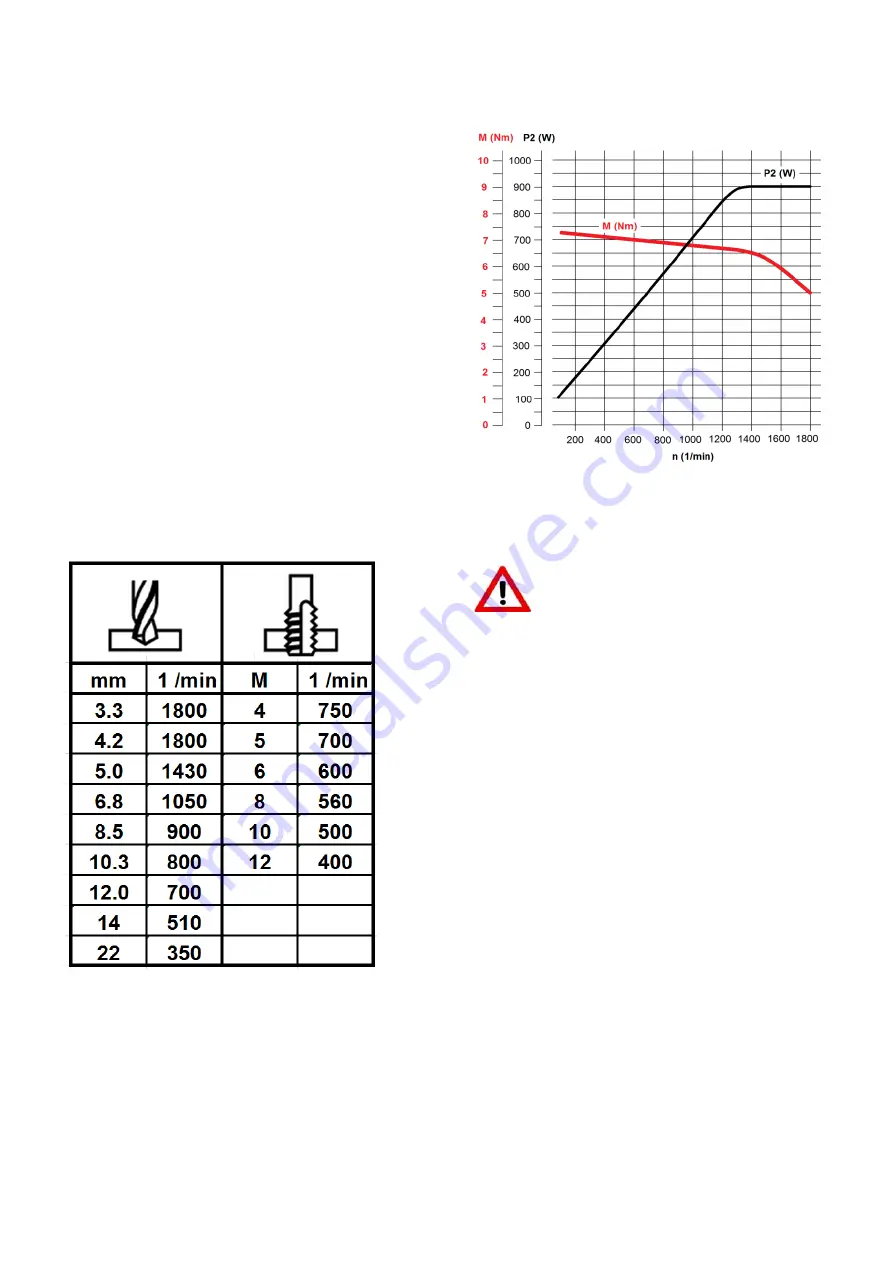
13
8.1
Recommended Speeds
ATTENTION:
Generally speaking, the smaller the drill bit, the greater the RPM
required. Soft materials require higher speeds; hard metals
slower speeds.
Metal is usually drilled at slower speeds and cutting oil is applied.
Recommended speeds for a 10mm HSS drill bit:
Soft Wood: ......................................................... 1800 RPM
Hard Wood: ........................................................ 1500 RPM
Plastic: ............................................................... 1800 RPM
Aluminium: ........................................................ 1800 RPM
Brass: ................................................................. 1000 RPM
Cast iron: ........................................................... 1000 RPM
Mild steel: ............................................................ 800 RPM
High carbon steel: ................................................ 600 RPM
Stainless steel: ..................................................... 300 RPM
Use the speed chart (Fig. 8-1) provided on the machine as a
general guideline for drilling and tapping mild steel.
Figure 8-1: Speed Chart for Mild Steel
The ECD-750BDV drill press is equipped with a highly efficient
Brushless DC Motor.
With direct drive design, low moment of inertia, no belt
transmission losses.
Direction changes are quick, allowing high speed tapping.
High torque (M) and power (P2) are available over a wide spindle
speed range (n).
Figure 8-2: Spindle Speed, Torque and Power Chart
9.0
User-Maintenance
WARNING:
Before any intervention on the machine, disconnect it from
electrical supply by pulling out plug or turning off main
switch at electrical source. Failure to comply may cause
serious injury.
A coat of automobile-type wax applied to table and column will
help keep surfaces clean.
Check that bolts are tight and electrical cords are in good
condition. If an electrical cord is worn, cut, or damaged in any
way, have it replaced immediately.
9.1
Lubrication
All ball bearings are pre-lubricated and sealed, and require no
further lubrication.
Periodically apply grease to:
Rack.
Table elevating mechanism, including worm gear.
Teeth of quill.
Periodically apply light coat of machine tool oil to quill and
column.
The quill return spring should receive SAE 20 oil once yearly.
Apply the oil beneath spring cover (N, Fig. 6-3) using a squirt
can.
Summary of Contents for ELITE ECD-750BDV
Page 1: ...1 ...
Page 15: ...15 13 0 Replacement Parts ECD 750BDV Table Base Assembly breakdown ...
Page 17: ...17 ECD 750BDV Headstock Assembly Breakdown ...
Page 34: ...15 13 0 Ersatzteile ECD 750BDV Stückliste der Baugruppe Tisch Sockel ...
Page 36: ...17 ECD 750BDV Stückliste der Spindelstockbaugruppe ...
Page 53: ...15 13 0 Pièces de rechange Défaillance de la base table ECD 750BDV ...