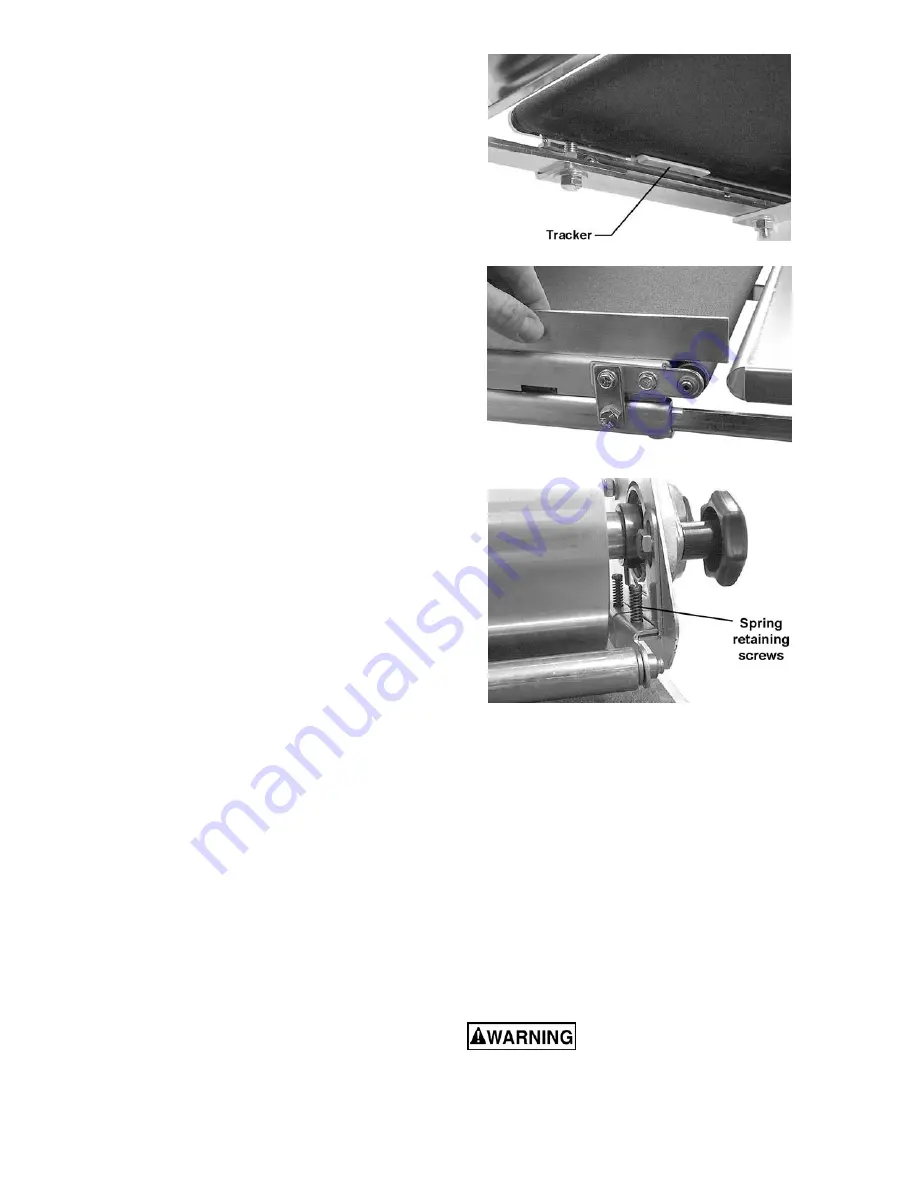
20
Trackers
The sander comes equipped with “Trackers”,
ceramic guides that reduce the amount of
adjustments needed to keep the conveyor belt
tracked (centered) on the conveyor bed (see
Figure 26). These guides have a magnetic backing
to keep them in place. If a Tracker wears through, it
can be reversed by turning it over. The
Tracker Kit
section on page 27 contains more information
about re-setting trackers.
Conveyor Belt Replacement
1. To replace a worn conveyor belt, lower
conveyor table to its lowest position using the
height adjustment handle. Unplug the machine
from the wall receptacle, and unplug the motor
cord from the control box receptacle.
2. Loosen the conveyor take-up screw nuts (see
Figure 25) to relieve belt tension, and slide the
driven roller fully inward.
3. Remove the four bolts that attach the conveyor
table to the table mounting brackets. Lift up the
conveyor table and remove it from machine.
Avoid tearing the belt on any edges underneath
the conveyor bed.
4. Install new belt, and re-install conveyor table.
Take care not to damage the Trackers. Tension
and track new belt.
Note:
If the conveyor belt continually tracks to one
side of the machine, reversing the belt on the
conveyor bed may remedy the problem. To make
sure the conveyor bed is not twisted, place a level
on the conveyor bed. If it is twisted, see page 11 for
instructions on leveling the machine.
If there is still a problem, proceed with the steps
below:
Step 1: Check the conveyor drive roller and the
driven roller to make sure they are parallel to the
surface of the conveyor bed. To do this, first center
the conveyor belt on the bed. Then lay a straight-
edge on the exposed edge of the conveyor bed on
the left (outboard) side, extending it over the roller.
See Figure 27. Note the distance between the roller
and the straightedge.
Step 2: Now repeat Step 1 on the right (inboard)
side of conveyor. Compare the measurements from
side to side. If they are not equal, loosen one of the
brackets that hold the roller in place. Tip this
bracket until the distance between the roller and
the straight-edge are equal from side to side, then
tighten the bracket.
Tension Roller Adjustment
Snipe marks result from too much tension roller
pressure and are identified as a visible line running
across the width of the board approximately 2-1/4”
from the end of the board. If a snipe mark occurs
Figure 26
Figure 27
Figure 28
on the leading edge of the board, adjust the
outfeed tension roller. If a snipe mark occurs on the
trailing end of the board, adjust the infeed tension
roller.
Tension roller pressure can be decreased in one of
two ways:
Method 1 –
Loosen spring retaining screws (Figure
28). Do not disengage screws entirely.
Method 2
--
Raise height of tension rollers as
follows. Repeat
Initial Drum Alignment
procedure
(page 18), using the drum alignment templates
under the drum, except place a few sheets of paper
under the tension roller(s) needing adjustment. Do
NOT place the paper under the drum or alignment
templates. Tighten bolts. Repeat this procedure
until the snipe is eliminated.
Improperly adjusted tension
rollers (i.e. those set too high, rendering them
non-functional) could allow kickback or
slippage of pieces being sanded.
Summary of Contents for 22-44 Pro-3
Page 35: ...35 Stand Assembly...
Page 37: ...37 Drum Head Assembly...