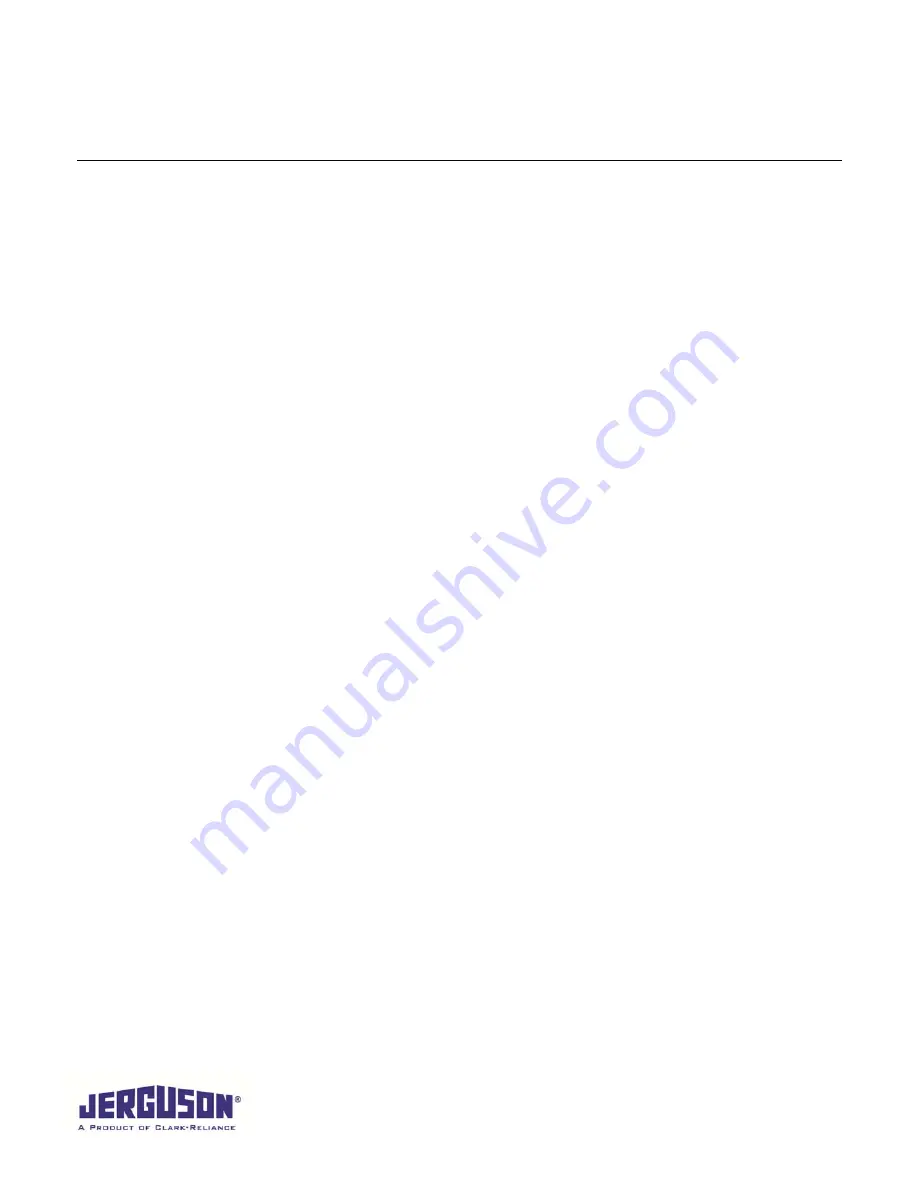
Installation, Operation, & Maintenance Instructions
IOM JS500.03
2016.04
Vertical Float Switches
General Installation Instructions – Part 1: Switch Assembly
Installation shall be carried out by suitably trained personnel in accordance with all local and national codes.
For hazardous area installations, also see ‘Installation Instructions Specific to Hazardous Areas’ section, page 10.
1. Remove all packaging and inspect each switch assembly upon receipt and prior to installation. Careful handling is
required at all times to ensure that any and all electrical enclosure(s), chamber(s), process connection(s) (flange facing,
threading, etc.), exposed float(s) and/or rod(s) are not dirty, damaged, or bent.
2. Check the tag to ensure that both the operating conditions and electrical requirements of the application are within the
ratings of the switch.
3. It is recommended that block/isolation valves be used, installed between the vessel and the switch assembly chamber,
when provided with a chamber.
4. Mount the switch assembly to the process connection(s), ensuring that its’ central line axis is vertical to the eye. Use
suitable gaskets and/or seals for each connection and/or joint, if required, and as dictated by the application.
Note (Series
JD_ _F):
If float cannot fit through mounting/process connection, it must be unthreaded from the unit prior to installation.
Thread float back onto the unit, using a permanent thread locker, inside of the vessel after the head has been mounted, via
an access panel or similar.
Switch trip point locations.
a) Series JB_ _F & JX_ _F: Refer to page 12 for default switch trip points. Refer to any applicable
documents (purchase order, order acknowledgement, drawings, etc.) for switch assemblies ordered with
non-standard switch trip points.
b) Series JD_ _F: Switch trip points are customer specified. Refer to any applicable documents (purchase
order, order acknowledgement, drawings, etc.) for switch trip points.
Enclosure Cover Removal:
Allow for room above the switch assembly to remove enclosure cover. Actual distance
varies by enclosure, see page 13. For electrical enclosure type, refer to model code on pages 4-5.
5. Check torque values for all bolted connection(s), if applicable. Values shall be in accordance with manufacturers
recommendation based on bolting, gasket materials, etc. Reference page 14.
6. Remove the cover to the switch assembly’s electrical enclosure to reveal the terminal block(s) to which electrical
connections are to be made.
Explosion-proof models:
Locate and loosen the M5 socket head safety grub screw on the side of enclosure cover,
adjacent to base joint. Place a bar across the top of the cover, locating in the castellations. The cover can now be
unscrewed from the base using the bar as a lever. Secure the base of the switch assembly’s electrical enclosure if
it turns freely with the cover.
Weatherproof models:
Loosen the hexagon bolt at the top and remove enclosure cover. Do not completely
remove the bolt, since a retaining washer on the bolt, inside of the enclosure cover, will reduce the risk of loss. If
bolt is removed, reassemble making sure that the fiber sealing washer sits below the bolt head.
7. Connect electrical wiring via the conduit entries using a suitable cable gland. Note that the base of the enclosure is
rotatable on the pressure tube to allow the most convenient orientation of the conduit entry.
Refer to wiring notes on page 6 (all locations), & if applicable, page 7 (hazardous locations) .
8. The lugs of the tab washer directly underneath the base must now be bent over to locate on the most appropriate flats of
the hexagon union. This prevents further rotation of the electrical enclosure base, which protects the integrity of the wiring
and terminal connections, particularly when the electrical enclosure cover is removed or re-fitted.
9. Switch point adjustments may now be made if necessary, see page 13.
10. Check that cover seals in the enclosure base are present and in good condition, and then replace the cover.
Explosion-proof models:
Before energizing
, ensure the cover locking safety grub screw is replaced and
tightened. Do not energize if the cover locking safety grub screw is missing.
Weatherproof models:
Before energizing,
ensure that the fiber sealing washer and hexagon bolt were reinstalled
at the top of the cover.
www.Jerguson.com
●
JergusonApp@clark
‐
reliance.com
●
+1.440.572.1500
8