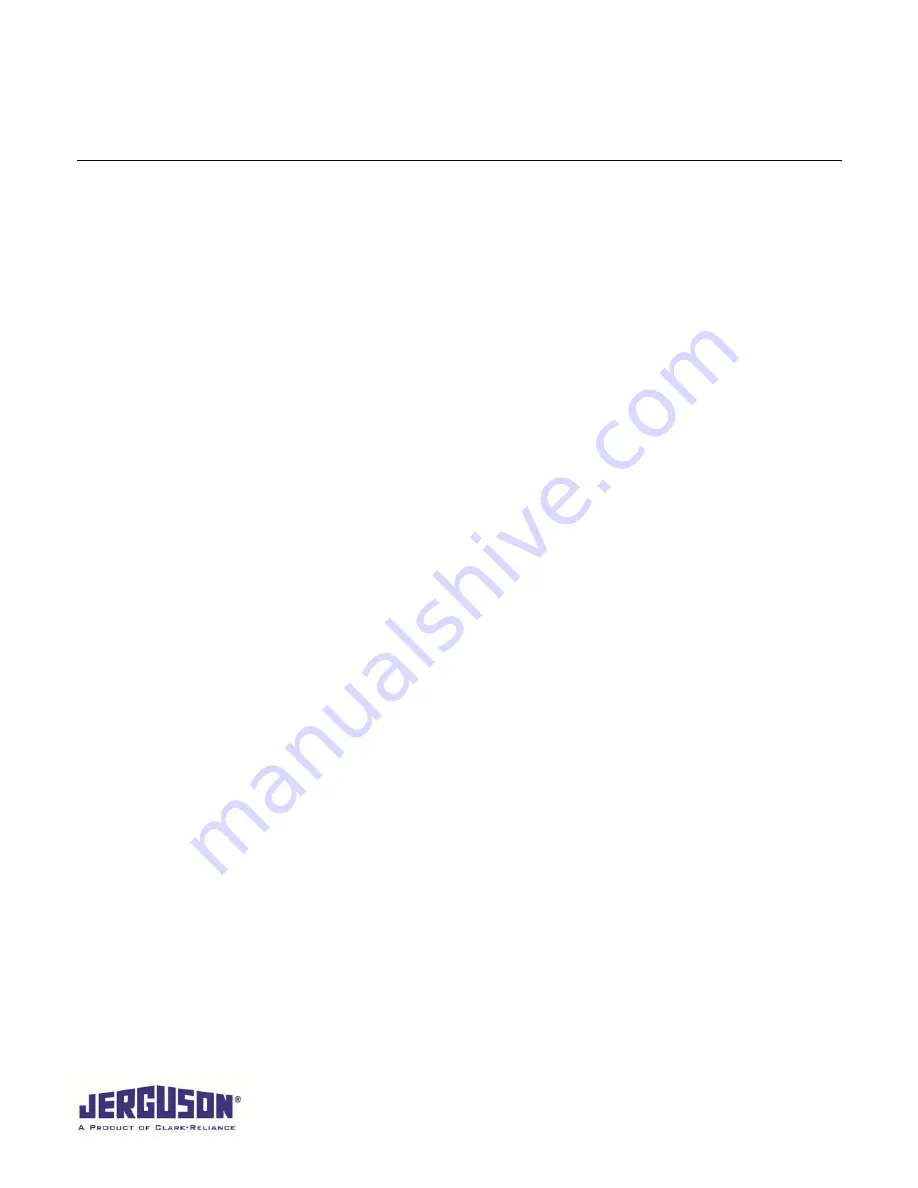
Installation, Operation, & Maintenance Instructions
IOM JS500.03
2016.04
Vertical Float Switches
Putting the Switch into Service
1. Check the tag to ensure that the operating conditions of the application are within the ratings of the switch.
2. Check that any and all valves, plugs, etc. are securely closed. Check torque values for bolting of process connections
and/or switch head flange, if either apply. Values shall be in accordance with manufacturers recommendation based on
bolting, gasket materials, etc. Reference page 14.
3. Slowly bring the switch up to pressure by opening the upper block/isolation valve, or by similar means. Take caution not
to damage the switch if fluid is available to the upper block/isolation valve, or other. As fluid under pressure can be
extremely dangerous.
4. If available, slowly introduce & equalize a liquid level to the switch by opening the lower block/isolation valve, or by
similar means.
Taking the Switch out of Service
1. Isolate the switch from any pressure and/or fluid by closing both the upper and lower block/isolation valves, or by similar
means.
2. Slowly open a vent valve, vent plug, or similar connection to relieve pressure on the switch. If the vent valve or
connection is available to the fluid, take caution as fluid exiting the switch under pressure can be extremely dangerous.
3. Remove any remaining fluid from the chamber using a drain valve, drain plug, or the lowest connection.
Maintenance of the Jerguson
®
Vertical Float Switch
Inspection and maintenance shall be carried out by suitably trained personnel in accordance with all local and
national codes.
1.
Isolate electrical circuits to switch and disconnect wiring as necessary.
a.
Series JB_ _F switches: Continue with step 9.
b.
Series JX_ _F & JD_ _F switches: Continue with step 2.
2.
Take switch out of service, according to the respective section above.
3.
Remove top flange nuts holding switch to chamber/vessel and carefully withdraw switch head and float assembly,
taking care not to bend the float rod.
4.
Separate float assembly from pressure tube by pinching & removing stop clip. (Note: The stop tube, which sits on the
stop clip, may prevent you from pinching the stop clip sufficiently to remove it. Stop tube may have to be moved into
the pressure tube in order to remove.)
5.
Check float, float rod, magnet, sealing surface and gasket for excessive wear and/or damage. Clean and/or replace as
necessary.
6.
Inspect the chamber and remove any deposits.
7.
Fit replacement joint and reassemble, taking care not to bend the float rod. Firmly tighten nuts on top flange, using bolt
torque values given in tables on page 14.
8.
Bring switch into service, according to the respective section above.
9.
Remove the switch head cover and examine the switch mechanism body for any damage. Ensure that wiring is in good
order and that all the screws are tight.
Dismantling of switch mechanism is not recommended and replacement of
the complete switch mechanism will be found to offer the quickest and most economical solution in event of
faulty operation.
See page 15.
10. Check sealing gasket / “O” ring and replace if necessary.
11. Check the cover seals are present and in good condition, and then replace the cover.
a.
Explosion-proof models:
Before energizing
, ensure the cover locking safety grub screw is replaced and
tightened. Do not energize if the cover locking safety grub screw is missing.
b.
Weatherproof models:
Before energizing,
ensure that the fiber sealing washer and hexagon bolt were
reinstalled at the top of the cover.
www.Jerguson.com
●
JergusonApp@clark
‐
reliance.com
●
+1.440.572.1500
11