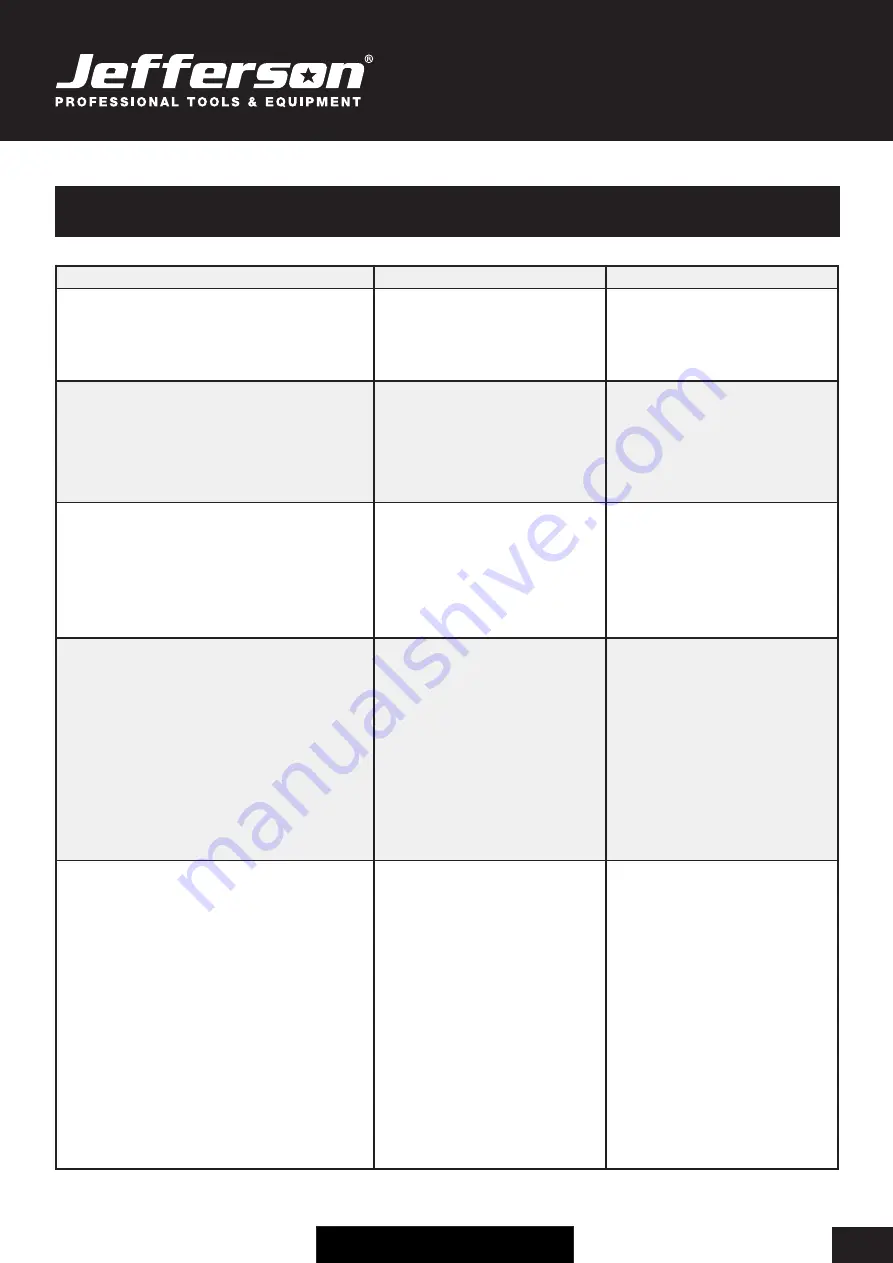
USER MANUAL
JEFARC140M-230
140A
DC INVERTER ARC WELDER • 230V
~
50Hz • 13A
www.jeffersontools.com
11
MMA TROUBLESHOOTING
PROBLEM
CAUSE
SOLUTION
Air pockets or voids in the weld metal (porosity)
1. The electrodes are damp
2. The welding current is too high
3. Presence of surface impurities such
as oil, grease, paint etc.
1. Only use dry electrodes
2. Reduce the welding current
3. Clean the joint before welding
Gaps & voids left in the root of the weld root by the
electrode
1. Welding current is too low
2. The electrode is too large for the joint
3. Insufficient gap
4. Incorrect sequence
1. Increase the welding current
2. Use a smaller diameter
electrode
3. Allow a wider gap
4. Use the correct build-up sequence
Cracks appearing in the weld metal soon after solidifica-
tion commences
1. Pressure on the weld joint
2. Insufficient throat thickness
3. Cooling rate is too high
1. Reposition the weld joint with less
stress / pressure or try using a crack
resistant electrode
2. Travel slightly slower to allow greater
build up in the throat
3. Preheat the plate and cool slowly
Portions of the weld run do not fuse to the surface of the
metal or edge of the joint
1. The electrode is too small for the
welding process and/or used on plate
that is too heavy or too cold.
2. Welding current is too low
3. Electrode is being used at the wrong
angle
4. The travel speed of the
electrode is too fast
5. There is scale or dirt on the joint
surface
1. Use larger electrodes and preheat the
plate
2. Increase the welding current
3. Adjust the angle so that the welding
arc is directed more into the base metal
4. Reduce the travel speed of the weld-
ing electrode
5. Clean the surface before welding
Non-metallic particles are trapped in the weld metal (slag
inclusion)
1. Non metallic particles may be trapped
in any undercut from the previous run
2. Joint preparation was not carried out
correctly or was too restricted
3. Irregular deposits allow slag to be
trapped
4. Lack of penetration from the welding
arc because of slag trapped beneath the
weld bead
5. Rust or mill scale is preventing full
fusion
6. The Wrong electrode for
position in which welding
1. If bad undercut is present clean the
slag out and cover with a run from a
smaller diameter electrode
2. Allow for adequate penetration and
room by cleaning and
removing any slag.
3. Remove the irregular deposits by
chipping or grinding out the irregular
deposits.
4. Use a smaller electrode with sufficient
current to give
5. Clean the joint thoroughly before
welding
6. Use electrodes best suited for the
position in which the welding process is
carried out
Summary of Contents for JEFARC140M-230
Page 1: ...User Manual v 1 1 JEFARC140M 230...
Page 2: ......