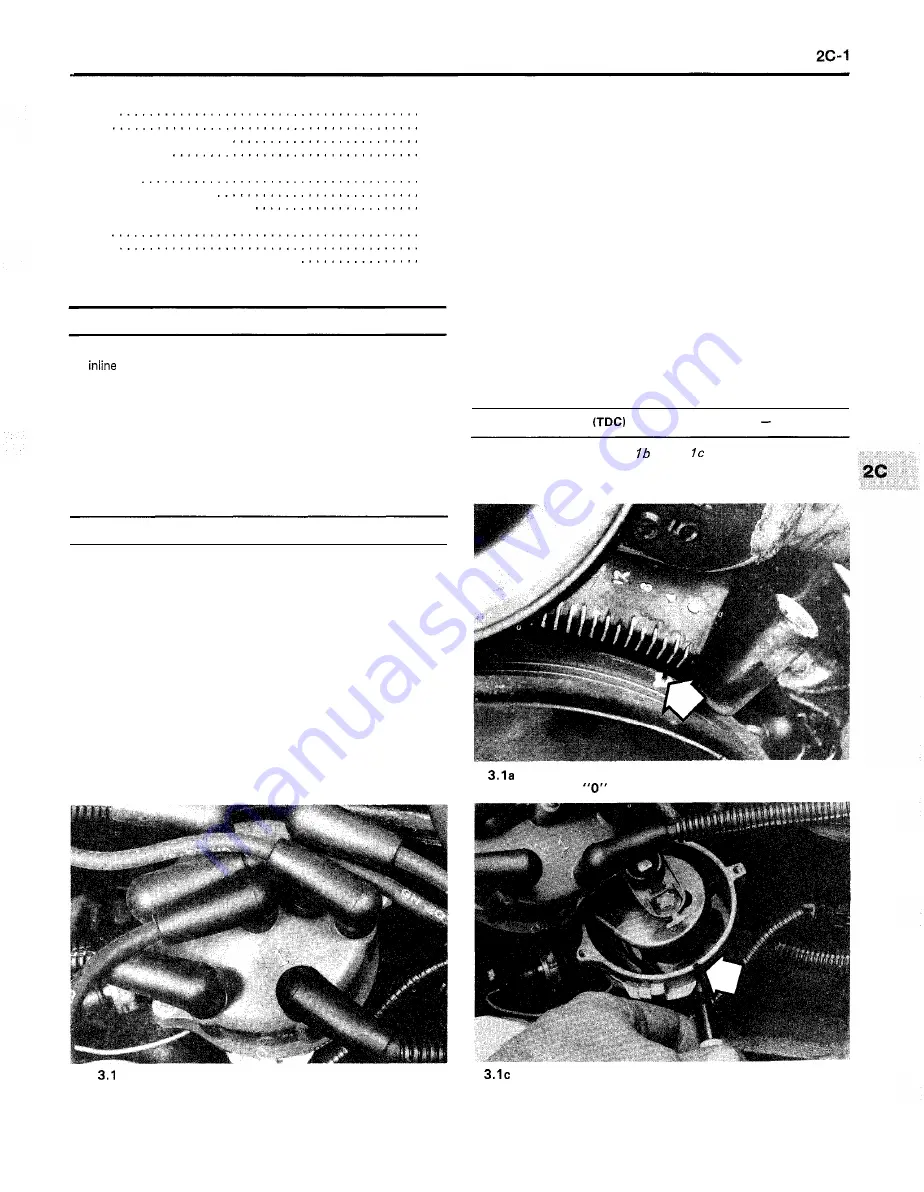
Chapter
2 Part C lnline six-cylinder engine
Oil pump mounting bolt
Short
1 0
Long
17
Rear main bearing cap bolts
8 0
Rocker arm bolts
1 9
Rocker arm cover-to-cylinder head bolts
With RTV
28 in-lbs
With permanent gasket
55
in-lbs
Tensioner bracket-to-block bolts
14
Timing chain cover-to-block
Bolts
5
Studs
1 6
Vibration damper center bolt (lubricated)
80
1 General information
This Part of Chapter
2
is devoted t o in-vehicle repair procedures for
the
six-cylinder engine. All information concerning engine removal
and installation and engine block and cylinder head overhaul can be
found in Part
D of this Chapter.
The following repair procedures are based on the assumption that
the engine is installed in the vehicle. If the engine has been removed
from the vehicle and mounted on a stand, many of the steps outlined
in this Part of Chapter 2 will not apply.
The Specifications included in this Part of Chapter 2 apply only t o
the procedures contained in this Part. Part
D of Chapter 2 contains the
Specifications necessary for cylinder head and engine block rebuilding.
2
Repair operations possible w i t h the engine in the vehicle
Many major repair operations can be accomplished without removing
the engine from the vehicle.
Clean the engine compartment and the exterior of the engine with
some type of pressure washer before any work is done. It will make
the job easier and help keep dirt out of the internal areas of the engine.
Remove the hood, if necessary, to improve access t o the engine as
repairs are performed (refer t o Chapter 11 if necessary).
If vacuum, exhaust, oil or coolant leaks develop, indicating a need
for gasket or seal replacement, the repairs can generally be made with
the engine in the vehicle. The intake and exhaust manifold gaskets,
timing cover gasket, oil pan gasket, crankshaft oil seals and cylinder
head gaskets are all accessible with the engine in place.
Exterior engine components, such as the intake and exhaust
manifolds, the oil pan (and the oil pump), the water pump, the starter
motor, the alternator, the distributor and the fuel system components
can be removed for repair with the engine in place.
Since the cylinder heads can be removed without pulling the engine,
valve component servicing can also be accomplished with the engine
in the vehicle. Replacement of the camshaft and timing chain and
sprockets is also possible with the engine in the vehicle.
In extreme cases caused by a lack of necessary equipment, repair
or replacement of piston rings, pistons, connecting rods and rod bear-
ings is possible with the engine in the vehicle. However, this practice
is not recommended because of the cleaning and preparation work that
must be done t o the components involved.
3 Top Dead Center
for number one piston
locating
Refer to illustrations
3.
la,
3.
and
3.
See Chapter 2, Part A, Section
3
for this procedure, but refer to the
illustrations and specifications included in this Section.
Align the notch (arrow) on the vibration damper w i t h
the
on the timing chain cover
b Locate the number one spark plug terminal on the
distributor cap, make a mark on the distributor housing,
directly under the number one plug terminal,
. . .
. . .
then remove the distributor cap and verify that the
rotor is pointing at the mark (arrow)
The Motor Manual Guy
Summary of Contents for cherokee 1989
Page 2: ...The Motor Manual Guy...
Page 3: ...The Motor Manual Guy...
Page 32: ...The Motor Manual Guy...
Page 191: ...The Motor Manual Guy...
Page 266: ...The Motor Manual Guy...
Page 267: ...The Motor Manual Guy...