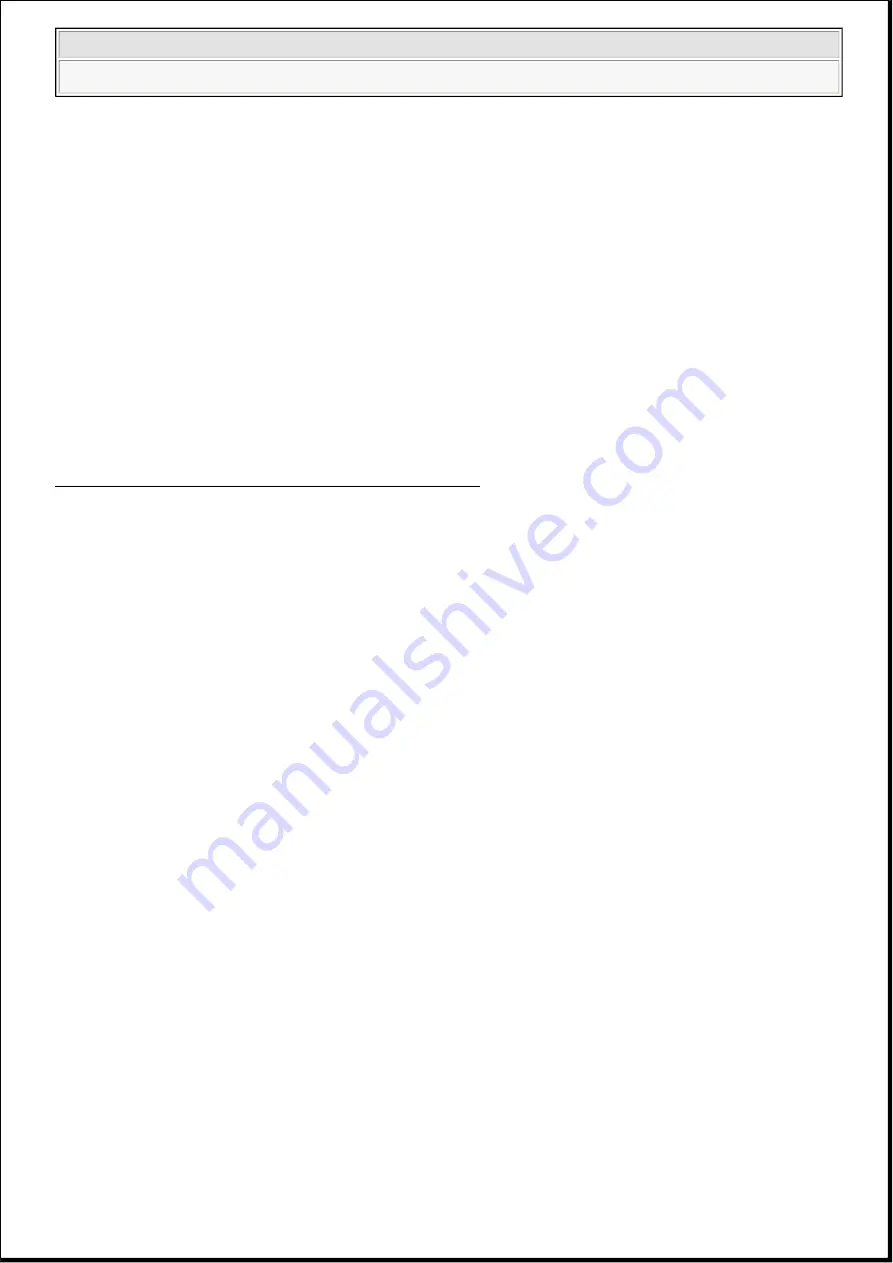
2014 SUSPENSION
Tires & Wheels - Service Information - Compass & Patriot
DIAGNOSIS AND TESTING
DIAGNOSIS AND TESTING - TIRE AND WHEEL VIBRATION
Tire and wheel imbalance, runout and tire road force variation can cause vehicles
to exhibit steering wheel vibration and/or seat vibration.
VISUAL INSPECTION
Visual inspection of the vehicle is recommended prior to road testing or
performing any other procedure. Raise and support the vehicle. Refer to
HOISTING, STANDARD PROCEDURE
.
Inspect for the following:
Verify correct (OEM) wheel and tire, as well as presence of wheel weights.
Inspect tires and wheels for damage, mud packing and unusual wear; correct
as necessary.
Check and adjust tire air pressure to the pressure listed on the label attached
to the driver's door opening.
ROAD TEST
Road test vehicle on a smooth road
at and near the designated speed
where
legal speed limits allow. Lightly place hands on steering wheel at the 10:00 and
2:00 positions and observe for:
Steering wheel oscillation: clockwise/counterclockwise
Steering wheel high frequency movement: rapid vibration up and down
NOTE:
If a Noise & Vibration Analyzer is available, use it to
diagnosis the issue during the road test.
NOTE:
If the vehicle has been sitting for an extended period of
time it is recommended to drive to warm the tires. This
process could eliminate flat spots that can cause
vibration.
2014 Jeep Patriot Limited
2014 SUSPENSION Tires & Wheels - Service Information - Compass & Patriot
2014 Jeep Patriot Limited
2014 SUSPENSION Tires & Wheels - Service Information - Compass & Patriot
Tuesday, July 19, 2016 10:01:58 AM
Page 1
Tuesday, July 19, 2016 10:02:00 AM
Page 1
1