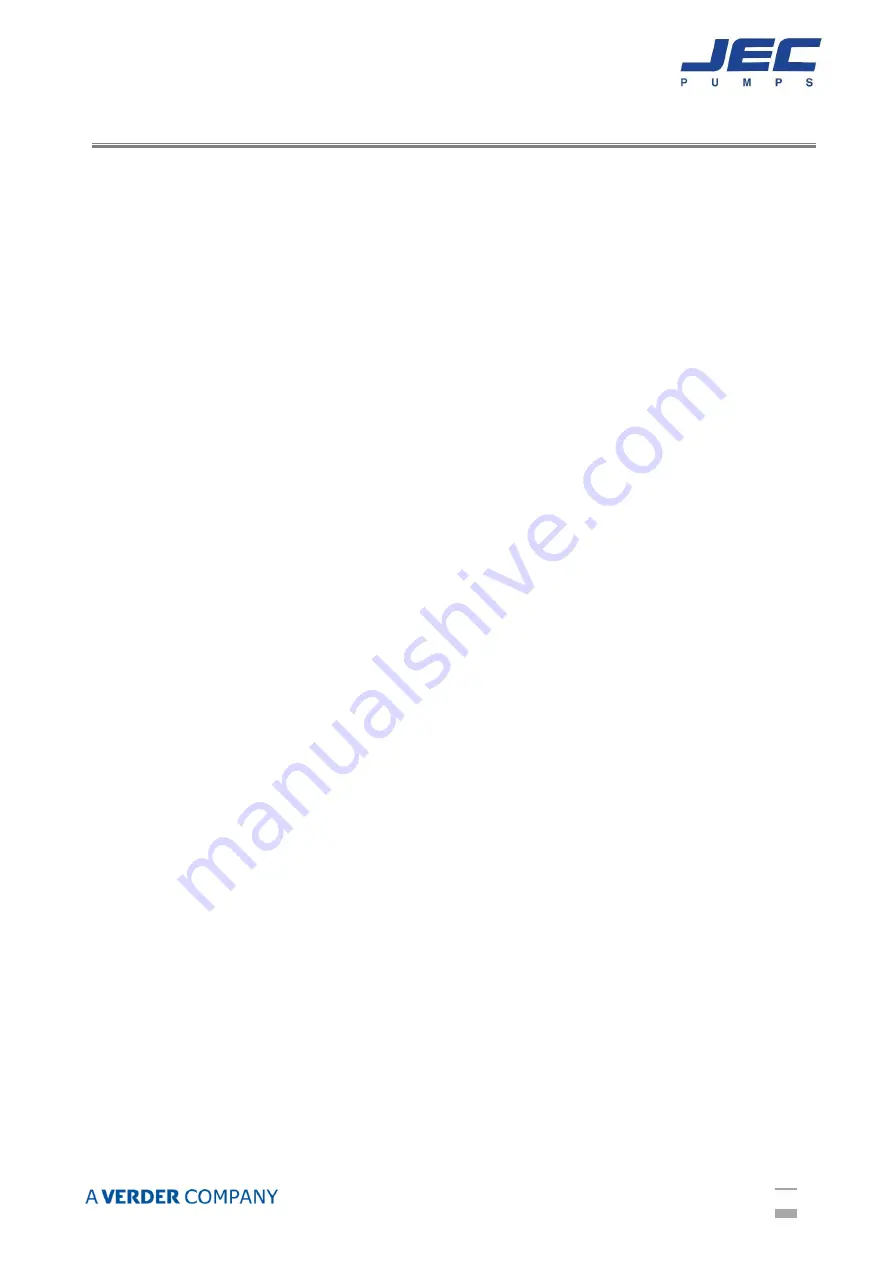
13
INSTALLATION
INSTALLATION
1.
Mounting surface should be flat and level.
2.
Ensure at least 0.5m clearance around the pump.
3.
Normally, pump and drive unit are configured with common bed. If you want other way,
feel free to contact JEC.
4.
To check the direction of rotor’s rotation, start and stop the motor for a short time.
5.
Before connecting pipelines, check the location of suction and discharge.
6.
Ensure the pipelines are connecting correctly and tightly.
7.
The suction line should be kept as short as possible and present minimum friction loss.
8.
To check working condition correctly, we recommend installing flow open valve and
pressure gauge at discharge line.
9.
Suction and discharge lines must be fully supported and installed so that no expansion or
shock forces act on the pump which could lead to distortion.
10.
Ensure sufficient clearance around the motor and pump.
START UP
1.
Before connecting the suction and discharge pipe work the entire system must be
thoroughly cleaned to prevent damage from welding, grinding and other residues.
2.
Before starting, bump the motor to check if the motor fan is rotating clockwise or
counterclockwise when seen from the motor back. If the motor fan cannot be seen, look
through the pump case adaptor after takeoff motor shroud. (Bump means to momentarily
apply power to the motor and then immediately remove power).
3.
Direction of rotating must only be checked with a completely filed system. Where double
mechanical shaft seals are installed the flush supply must be operational. Any dry running
will result in seal damage.
4.
The motor rating plate should be checked to ensure that it is in accordance with the
available electrical supply. It is essential that the full load current is not exceeded to
prevent motor overload.
5.
Before start up any safety guards required by local statutory regulations should be fitted.
Pay attention to circumstances that could indicate pump cavitation;
1.
Low pressure in the suction line due to bad suction conditions.
2.
Air in the suction inlet line.
3.
Pumping temperature is too high.
4.
Pump is oversized.
Summary of Contents for JRZL Series
Page 1: ...Operating Maintenance Manual JEC JRZL Series Rotary Lobe Pumps...
Page 6: ...5...
Page 7: ...6...
Page 8: ...7...
Page 9: ...8...
Page 10: ...9...
Page 11: ...10...
Page 34: ...33 PARTS LIST EXPLODED VIEW ZL100 ZL200 AND ZL300...
Page 58: ...57 EXPLODED VIEW ZL400...