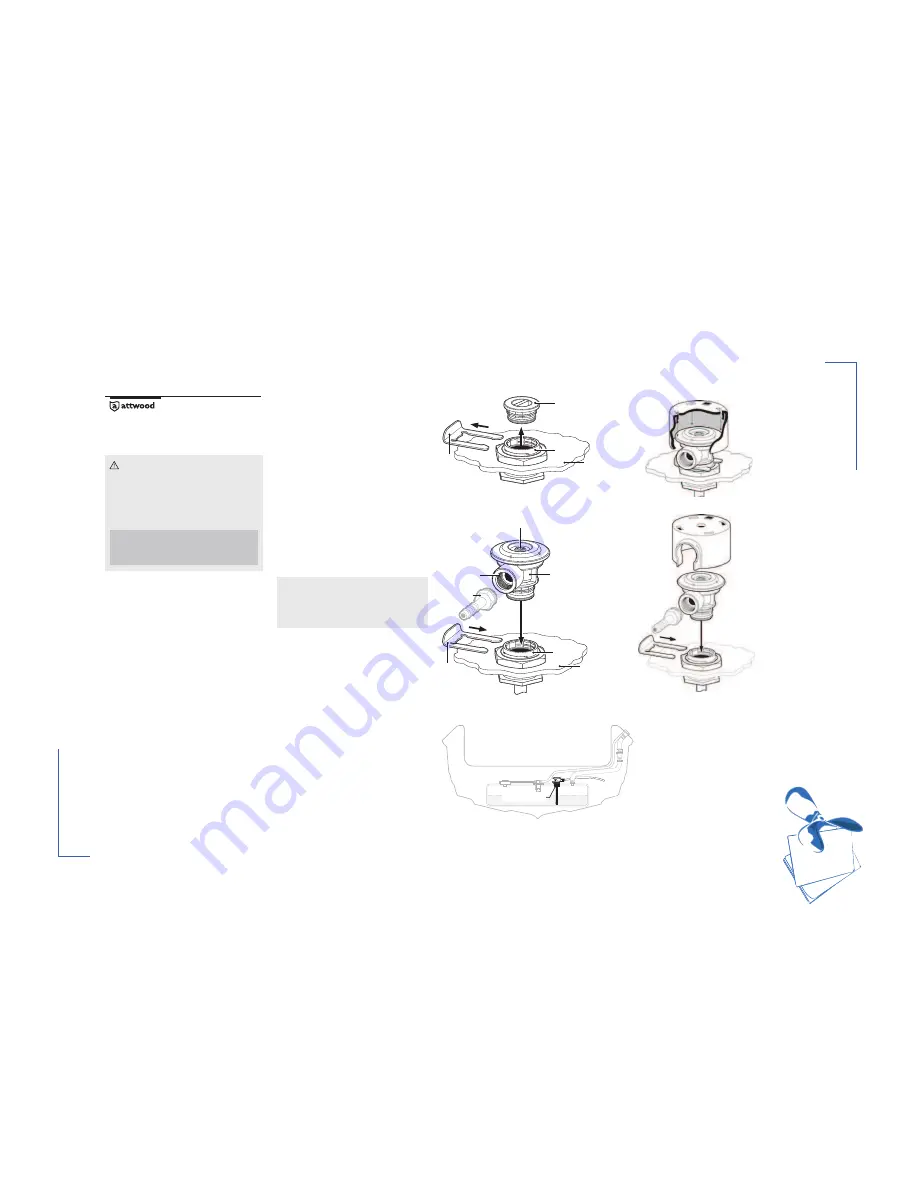
1
0
1
/1
0
4
1
2
INTEGRATED FUEL DEMAND VALVE
99IFDV Series
INSTALLATION INSTRUCTIONS
2/12
69487 Rev. C
SAVE THESE INSTRUCTIONS
CAUTION:
The vessel manufacturer must comply with the
requirements of CFR 40 1060.202. Any questions can be
directed to www.attwood.com
Failure to follow these instructions may result in accidental
fuel system over-pressurization. Users must follow these
instructions to ensure vessel function and operation
EMISSION-RELATED INSTALLATION INSTRUCTIONS
Failing to follow these instructions when installing the Attwood
Integrated Fuel Demand Valves in a piece of nonroad equipment violates
federal law (40 CFR 1068.105(b)), subject to fines or other penalties as
described in the Clean Air Act.
FEATURES:
Attwood’s Integrated Fuel Demand Valve meets EPA regulations. The Fuel Demand
Valve comes in five (5) different heights of anti-siphon shut off protection (0", 10",
15"
, 20
"
and 30
"
) and can be oriented in twelve (12) different positions providing optimal
orientation. The Fuel Demand Valve also has a manual override built into the top.
REQUIRED FOR INSTALLATION
t
Pliers for removal and assembly of retainer clip
t
Appropriate hose fitting (1/2" NPT)
t
Marine-grade urethane-based sealant (Attwood #30106-6 recommended,
DO NOT
USE A SILICONE-BASED SEALANT
)
t
Wrench for fitting
LOCATION
t
Mount of flat surface where risk of torsional loads being applied to the Integrated
Fuel Demand Valve is minimal
t
Locate in position where consumers will not kick or step on the valve
t
A heat shield (99IFDVHS1) is recommended to protect against fire unless the Fuel
Demand Valve passes USCG fire test in the as-installed position. If heat shield is
required, see separate installation sheet.
INSTALLATION INSTRUCTIONS
1. Locate built in Fuel Demand Valve aluminum base on tank
2. Remove clip and transport plug (Figure 1)
3. Install necessary barb fitting (1/2" NPT, not supplied). Use thread sealant.
4. Torque up to 8 ft-lb where applicable. Do not over torque.
Ensure sealing surface (interior of insert) is clean of debris
5. Remove shipping cover from valve assembly.
6. Lubricate O-ring with a petroleum based lubricant such as motor oil. Insert Fuel
Demand Valve to predetermined orientation (Figure 2). Once inserted, apply slight
downward pressure on Valve and install retainer clip fully into slot.
7. Once installed, apply slight upward pressure to Fuel Demand Valve to ensure it is
locked into position.
8. Pressure test tank to ensure connection integrity, per CFR 33 183.580, at pressure
of 3 psi for no less than 10 minutes. Inspect all connections for leak by method
other than pressure decay.
9. If 99IFDVHSI is installed, align top hole with the top of the vent cap and snap in
place. (Figure 3 & 4)
MANUFACTURER REQUIREMENTS
Manufacturer must determine required amount of anti-siphon protection for specific
vessel configuration per CFR 33. Manufacturer must select an Integrated Fuel Demand
Valve with at least that much anti-siphon protection. Manufacturer must ensure that
engine fuel distribution line vacuum requirements are met. See engine manufacturer
for details.
The information below applies only to EPA CFR 40 1060.135. The vessel manufacturer
is responsible to meet all additional regulatory labeling requirements including EPA,
CARB, USCG and others as necessary. The below information is for reference only.
The vessel manufacturer should refer to CFR 40 for complete labeling guidelines.
In order to meet the requirements of CFR 40 1060.135, the vessel must be labeled
with respect to evaporative emissions in the following manner when installing certified
components;
Excerpt from CFR 40 1060.135
(a) You must affix a permanent and legible label identifying each engine or piece of equipment before
introducing it into U.S. commerce. The label must be—
(1) Attached in one piece so it is not removable without being destroyed or defaced.
(2) Secured to a part of the engine or equipment needed for normal operation and not normally
requiring replacement.
(3) Durable and readable for the equipment’s entire life.
(4) Written in English.
(5) Readily visible in the final installation. It may be under a hinged door or other readily opened
cover. It may not be hidden by any cover attached with screws or any similar designs. Labels on
marine vessels must be visible from the helm.
(c) If you produce equipment without certifying with respect to evaporative emissions, the equipment
label specified in paragraph (a) of this section must—
(1) State: ‘‘MEETS U.S. EPA EVAP STANDARDS USING CERTIFIED COMPONENTS.’’
(2) Include your corporate name.
Below is an example of a label specified by CFR40 1060.135 for use with certified
components;
MEETS U.S. EPA EVAP STANDARDS USING
CERTIFIED COMPONENTS
CORPORATE NAME
Please refer to CFR 40 1060.135 to review EPA vessel labeling requirements.
The NMMA has a program to supply OEM builders with labels. Please refer to the NMMA
website below for further information regarding the NMMA label program;
www.nmma.org/certification/products/labelsanddecals.aspx
TWO-YEAR WARRANTY & LIABILITY
Generally:
Attwood Integrated Fuel Demand Valves are covered by a two (2) year limited
warranty from the date of a Vessel’s first retail sale.
Pre-requisites to Warranty Eligibility:
For the warranty coverage described herein to
apply, the following conditions must be met:
t
Component must have been properly installed per Attwood installation instructions; and
t
The component cannot have been altered or abused by Boat Company or its customers.
Warranty Terms for Components:
Attwood warrants that any Attwood Integrated Fuel Demand Valves are free from defects
in materials and workmanship and are designed, built, and equipped to conform at the
time of sale to Boat Company with the 40CFR.1060 requirements. For two (2) years from
the date of a Program Boat’s first retail sale, Attwood will, at its sole option, repair or
replace any components that fail due to a defect in material or workmanship. ATTWOOD
PROVIDES NO WARRANTIES WITH RESPECT TO ANY PART OR COMPONENT NOT
MANUFACTURED BY ATTWOOD, INCLUDING FUEL TANKS. Boat Company is responsible
for the installation of all Systems, whether installed by Boat Company or under its
direction.
A.B.Y.C.
American Boat & Yacht Council
3069 Solomon’s Island Road
Edgewater, Maryland 21037
www.abycinc.org
U.S. Coast Guard
Washington, DC 20460
www.uscgboating.org
E.P.A.
401 “M” Street, SW
Washington, DC 20593 www.
www.epa.gov
ISO
iso.org
National Marine
Manufacturers Association
(NMMA)
231 S. LaSalle Street
Suite 2050
Chicago, IL 60604
www.NMMA.org
Fuel Demand Valve
FIGURE 1
FIGURE 2
Tank
Tank
Clip
Clip
Transport
Plug
Valve
Assembly
Use thread
sealant
For Override
Using a small flat head screwdriver,
press downward through slot
Barbed Fitting
not included
Molded Nut
Molded Nut
©2011 Attwood Corporation
1016 North Monroe Lowell, MI 49331
www.attwoodmarine.com
FIGURE 4
Full Pressure Relief System
FIGURE 3
APPENDIXES
Summary of Contents for MERRY FISHER 855 OFF SHORE
Page 1: ...MERRY FISHER 855 OFF SHORE OWNER S MANUAL 993650 Index B...
Page 2: ......
Page 4: ......
Page 7: ...3 104 HISTORY OF UPDATES Index A 12 2014 Index B 01 2015...
Page 8: ......
Page 10: ......
Page 16: ......
Page 27: ...23 104 SUPPLY VALVE FUEL Location On the fuel tank 2 SAFETY...
Page 29: ...25 104 SCHEMA BILGE PUMP SYSTEM 2 1 2 3 4 5 6 7 8 9 10 11 12 13 14 SAFETY...
Page 33: ...29 104 HULL MAINTENANCE OF THE HULL LIFTING 3...
Page 36: ......
Page 44: ......
Page 48: ......
Page 49: ...45 104 STEERING SYSTEM STEERING GEAR 5...
Page 51: ...47 104 SCHEMA 5 1 2 3 4 5 6 7 8 9 9 OPTION 10 STEERING SYSTEM...
Page 53: ...49 104 INTERIOR INTRODUCTION INTERIOR MAINTENANCE MAINTENANCE OF FABRICS 6...
Page 54: ...50 104 INTRODUCTION DECK SALOON INTERIOR ACCOMMODATION...
Page 58: ......
Page 68: ......
Page 69: ...65 104 ELECTRICAL EQUIPMENT 12 V DC SYSTEM ELECTRICAL CIRCUIT 110 220 V EQUIPMENT 8...
Page 83: ...79 104 ELECTRONIC LAYOUT OF COMPONENTS LEAD LINES LOCH SPEEDO SOUNDER 8 ELECTRICAL EQUIPMENT...
Page 85: ...81 104 ENGINE GENERAL INFORMATION ENGINE FITTING 9...
Page 95: ...91 104 LAUNCHING LAUNCHING RECOMMENDATIONS 10...
Page 96: ...92 104 POSITION OF HOISTING CRADLE AND STRAPS Note Measurements are expressed in mm 1150 4000...
Page 98: ......
Page 99: ...95 104 WINTER STORAGE LAYING UP PROTECTION AND MAINTENANCE 11...
Page 102: ......
Page 103: ...99 104 APPENDIXES 1 12...
Page 107: ...103 104 12 APPENDIXES...
Page 108: ...104 104...