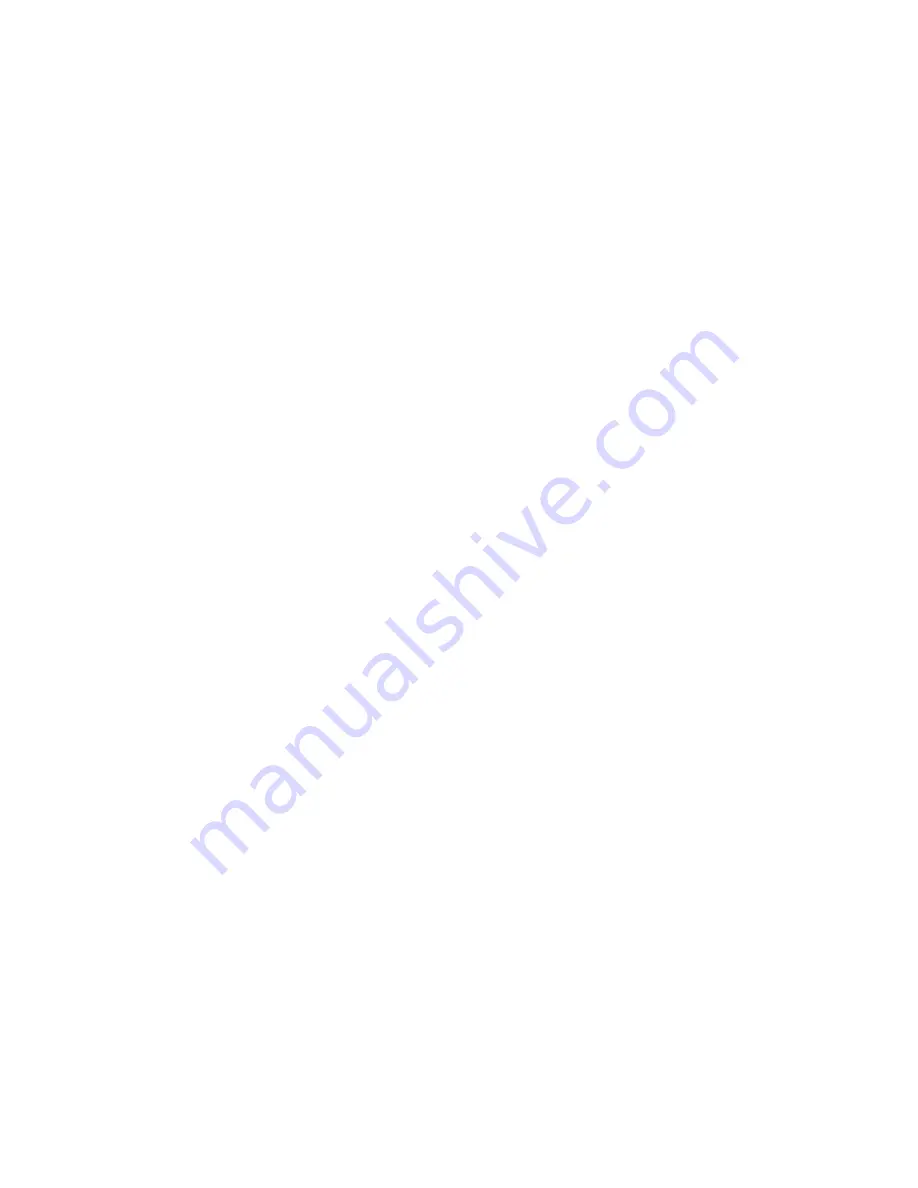
5
BOILER INTRODUCTION
When introducing the boiler, it should be ensured that the system is filled with water and air is
removed. The tightness of the piping should also be checked to avoid leaking damage to the
system.
The manometer must be observed in conjunction with the usage of the apparata. In coated
expansion container systems the pressure should be above 0,5 bar (but below 1,5 bar when
hot). Furthermore, check that the opening pressure of the safety valve is 1,5 bar.
Burner choice
All modern oil burners that are equipped with pre-heating and designed for 1.4-2.3 kg of oil/h,
are suitable. These values are reached at 0,5 US gall/h with a 60° nozzle when oil pressure is
6-14 bar.
Burner installation
An installation and usage manual is delivered with the boiler and it should be followed at all
times.
Burner adjustment
The exit gas values, required for burner adjustment, are measured from the analysis hole in
the duct connection piece. The analysis is taken on the first time of usage and the burner is
adjusted accordingly. Thus unnecessary smutting is avoided if ventilation is not sufficient. The
final adjustment is performed when boiler water r75 °C.
In oil usage the adjusted values are appropriate when the smut value is 0-1 in the bachrah
scale, O
2
% 3,5…4,5, CO
2
> 12 % and CO < 30 ppm.
Once the burner is correctly adjusted, the boiler needs sweeping approx. once a year!
NOTICE! Incorrect burner adjustment can damage the burner hatch and exit gas controls.
In normal boilers the exit gas temperature is approx. 140 °C. If this temperature is too low for
the chimney material, the temperature can be raised by removing some of the hindermost
plates of the exit gas controls (nr. 4, figure 3) in the convection part. Removing one plate is
equivalent to approx. a 10 °C rise in exit gas temp erature.
Wood part gear
damper (nr. 7, figure 1) according to instructions.
Suitable burners include e.g. Oilon Junior Pro LJ 10, (LF-1) and Riello B10.
The burner can only be installed by a person qualified for the job.
The traction control is installed in the traction control connection (nr. 5, figure 1) and the
WWW.JASPI.UK