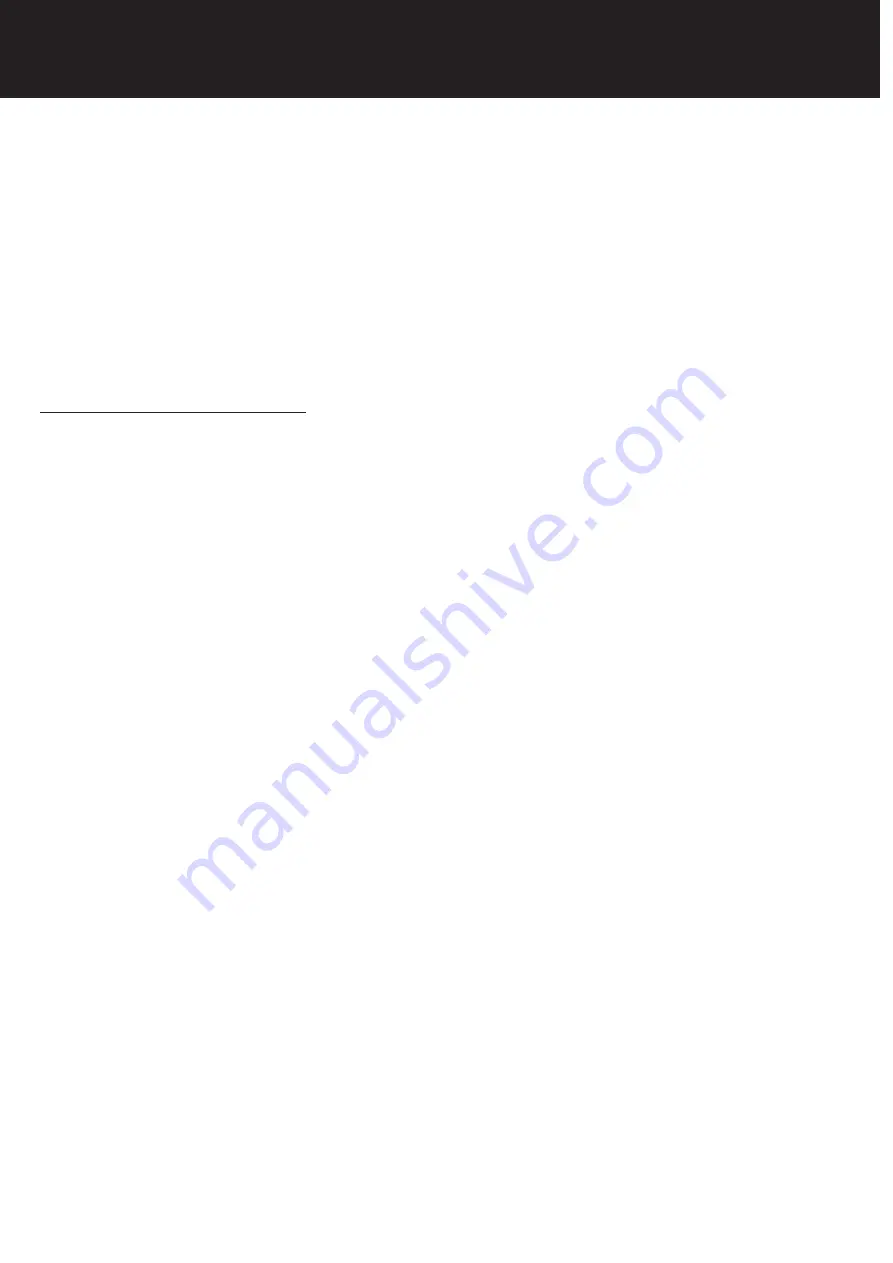
WARRANTY
JASIC Technologies America Inc (‘Us’, ‘We’) warrants that the following products under VIPERMIG supplied by Us and purchased
by you from an Authorised VIPERMIG Dealer throughout the U.S.A & Canada are free of Material and Faulty Workmanship
defects except for those products listed under ‘Warranty Exclusions’.
These terms and conditions supersede and exclude all former and other representations and arrangements relating to any
warranties on these products.
WARRANTY PERIOD
We offer the following ‘Warranty Periods’ from ‘date of purchase’:
An Extended Warranty Period of 6 months total shall apply only to Machinery where offered and warranty
is registered online.
1 Year
(Clause 1)
3 Years
(Clause
4
)
3 Years
(Clause
4
)
3 Years
(Clause
4
)
3 Years
(Clause
4
)
1 Year
(Clause
1
3 Years
(Clause
4
)
1 Year
2 Years
2 Years
3 Months
(Clause 3)
RAZ VIPER WELDING MACHINES
VIPER DIY Series (Power Source Only) VIPERMIG
RAZORWELD JASIC Inverter MIG (Power Source Only) RAZOR RANGE
RAZORWELD JASIC Inverter MIG SWF (Power Source / Separate Wire Feeder Only)
RAZORWELD JASIC Inverter TIG (Power Source Only)
RAZORWELD JASIC Inverter PLASMA (Power Source Only)
RAZORWELD Water Cooler
RAZORWELD JASIC Series (Power Source Only)
UNI-FLAME Regulators Argon/ Acetylene / Oxygen / LPG / Bobbin Flowmeter
UNI-FLAME Automatic Welding Helmet
RAZORWELD Automatic Welding Helmets
TORCHES -GMAW, GTAW, MMAW, PLASMA, EARTH LEADS,
INTERCONNECTING CABLES, GAS HOSE
(Clause 1)
1
year warranty on transformers, inductor and rectifier. 1 year warranty on PCB,
and all other components.
(Clause 2) Gas Hose, Flashbacks are subject to and covered by the Manufacturer’s Individual Warranty, Contact the manufacturer
for details
(Clause 3) This only Covers Manufactures defaults on all accessories for the first three months after date of
purchase.
It does not cover operator a
b
use or
mistreatment of the torch
(Clause 4) 3 years
w
arranty on tran
sformer , i
nductor and Recti
fier
,
1 year on
PCB
and all other co
m
ponents
:D
oes not cover
operator a
buse or mistreatment of the machine
• SELLER MAKES NO WARRANTIES EXPRESSED OR IMPLIED, INCLUDING BUT NOT BY WAY OF LIMITATION, ANY IMPLIED WAR-
RANTY OF MERCHANTABILITY AND ANY IMPLIED WARRANTY OF FITNESS FOR A
PARTICULAR PURPOSE, ON ANY ORDER EXCEPT THAT SELLER WARRANTS TITLE TO ALL GOODS FURNISHED BY SELLER AND
EXCEPT THAT SELLER WARRANTS FOR A PERIOD OF ONE YEAR FROM THE DATE MARK
LOCATED ON THE SELLER’S IDENTIFICATION TAG THAT ALL GOODS DESCRIBED ON SELLER’S
ACKNOWLEDGMENT OF PURCHASER’S PURCHASE ORDER WILL BE MANUFACTURED IN ACCORDANCE WITH THE SPECIFICA-
TIONS, IF ANY, SET FORTH IN SAID PURCHASE ORDER AND EXPRESSLY ACCEPTED IN
SELLER’S ACKNOWLEDGMENT SUBJECT TO SELLER’S STANDARD MANUFACTURING VARIATIONS AND
PRACTICES. IN THE CASE OF COMPONENTS OR ACCESSORIES FURNISHED BY SUPPLIERS TO SELLER, PURCHASER’S WARRANTY
FROM SELLER SHALL BE LIMITED TO THE WARRANTY OF THE COMPONENT OR ACCESSORY SUPPLIER. THE FOREGOING WAR-
RANTIES ARE THE SOLE AND EXCLUSIVE WARRANTIES
APPLICABLE TO THE GOODS DELIVERED, AND ALL OTHER WARRANTIES, EXPRESS OR IMPLIED, INCLUDING WITHOUT LIMITA-
TION ANY WARRANTY OF MERCHANTABILITY, ARE HEREBY EXPRESSLY DISCLAIMED AND NEGATED. WITHOUT LIMITING THE
GENERALITY OF THE FOREGOING, PURCHASER ACKNOWLEDGES THAT SELLER’S PRODUCTS ARE NOT PACKAGED OR PROTECT-
ED FOR LONG PERIODS OF STORAGE AND THUS MAY CORRODE OR RUST OVER TIME..
25503 74th Ave S Kent WA 98032 USA
Phone:
+1 253-859-6277
+1 253-859-6278
FAX:
+1 253-859-6286
EMAIL: [email protected]
VIPER
MIG
35