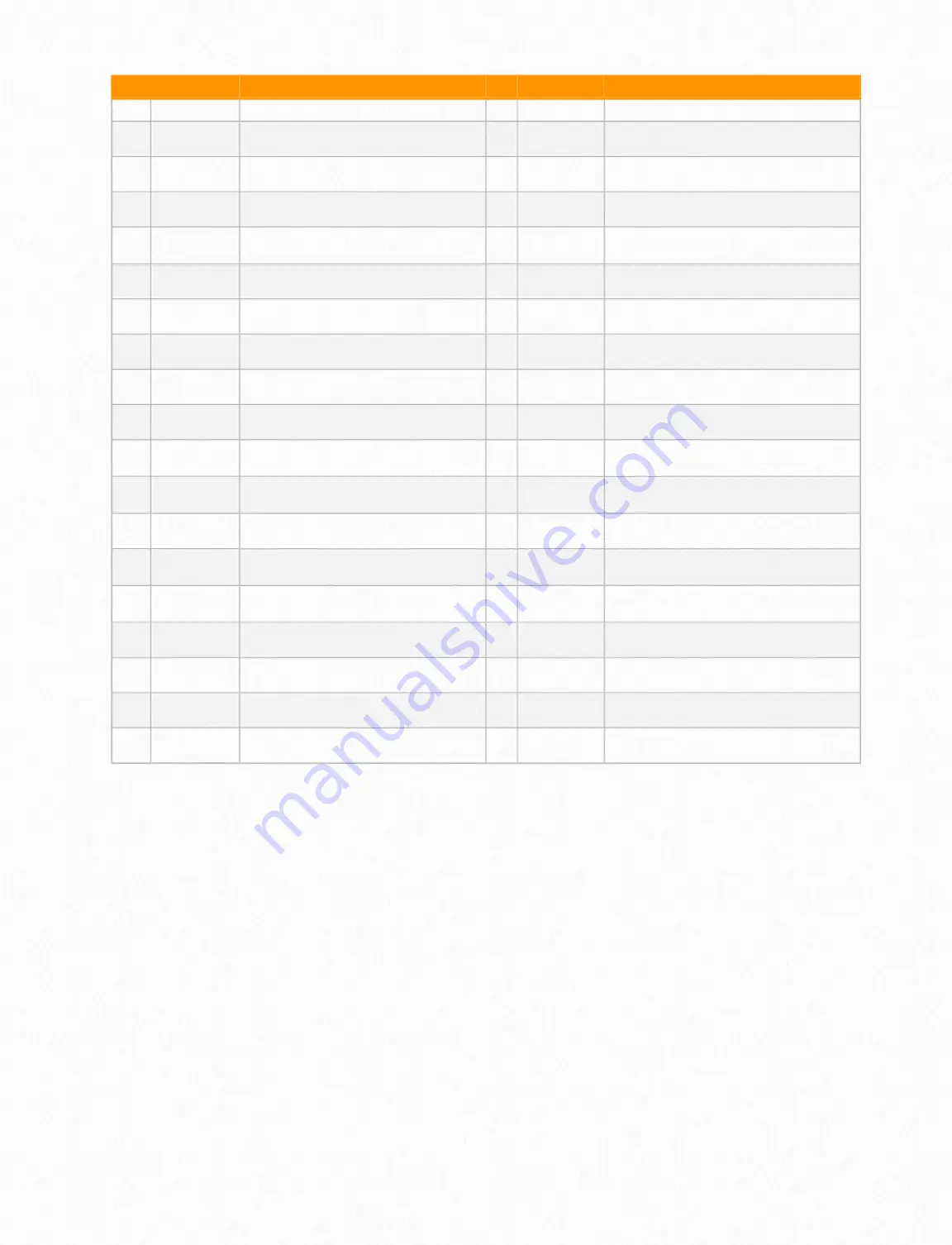
No.
Part no
Description
No.
Part no
Description
1
10004949
Power switch
19
10006282
IRF9Z24N
2
10041432
Power line
20
10006282
IRFZ24N
3
10042342
Connector for input gas
21
10037135
Driver transformer
4
10044009
TIG200P Dual voltage fan
22
10041436
Thermal switch
5
10043460
Back Panel
23
10037134
Switching mode power supply
transformer
6
10043476
Handle
24
10006477
12V Electric reply
7
10043689
Louver
25
10037146
TOP266KG
8
10042320
Bottom panel
26
10006673
KA7915
9
10041327
Isolation transformer
27
10040667
Solenoid value
10
10021853
Quick socket
28
10037078
Pin insulation cover
11
10043469
Front Panel
29
10038719
TIG200P Dual voltage electrolytic
capacitor
12
10042335
Knob
30
10037485
TIG200P Dual voltage silicon bridge
board
13
10042994
Display panel
31
10029693
TIG200P Dual voltage IGBT
14
10040688
EPC connection between hose and
gas connector
32
10042989
TIG200P Dual voltage control board
15
10040709
Hose
33
10041725
T I G 2 0 0 P D u a l v o l t a g e h i g h
frequency transformer
16
10004684
Air socket
34
10041326
Arc Coil
17
10042323
Machine Cover
35
10037431
Rectifier board
18
10006474
Electric Relay
36
10041436
Thermal resistor
37
100044483
Hall sensor
Summary of Contents for TIG 200P
Page 16: ...Electrical schematic 7 15 ...
Page 17: ...Parts list 8 16 ...