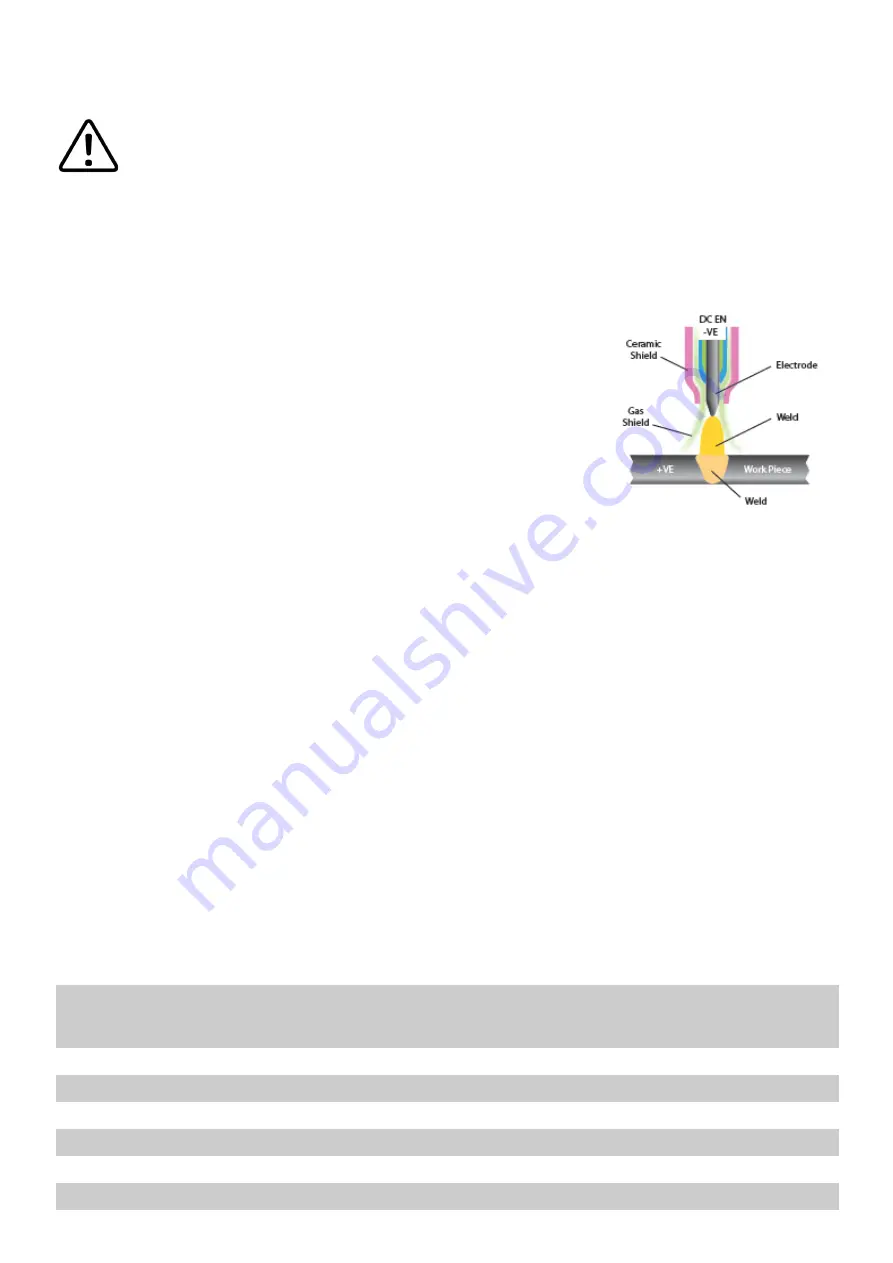
39
GUIDE TO TIG WELDING
Before starting any welding activity ensure that you have suitable eye protection and
protective clothing. Also take the necessary steps to protect any persons within the welding
area.
DC welding
Direct current welding is when the current flows in one direction only. Compared with AC welding the
current once flowing will not go to zero until welding has ended.
The Jasic TIG Series polarity should generally be set up for Direct Current
-
Electrode Negative (DCEN) as
this method of welding can be used for a wide range of materials.
The TIG welding torch is connected to the negative output of the machine
and the work return cable to the positive output.
When the arc is established the current flows in the circuit and the heat
distribution in the arc is around 33% in the negative side of the arc (the
welding torch) and 67% in the positive side of the arc (the work piece).
This balance gives deep arc penetration of the arc into the work piece
and reduces heat in the electrode.
This reduced heat in the electrode allows more current to be carried by
smaller electrodes compared to other polarity connections. This method of connection is often referred
to as straight polarity and is the most common connection used in DC welding.
TIG welding techniques
•
Before welding (especially with mild steel) you should ensure all material being welded are clean, as
particulates can weaken the weld.
•
The torch angle is best kept at 15
-
20 ° (from vertical) away from the direction of travel. This assists
with visibility of the weld area and allows easier access for the filler material.
•
The filler metal should be fed in at a low angle to help avoid touching the tungsten electrode and
contaminating it.
•
The TIG welding arc melts the base material and the molten puddle melts the filler rod, it is important
you resist the urge to melt the filler material directly into the welding arc.
•
For thinner sheet materials, a filler material may not be needed.
•
Prepare the tungsten correctly, using a diamond grinding wheel will give you the best results for a
sharp point. See page 31.
•
For welding stainless steel, be careful of applying too much heat. If the colour is dark grey and looks
dirty and heavily oxidized then too much heat has been applied, this could also cause the material
to warp. Reducing the amperage and increase travel speed may correct this problem, you could also
consider using a smaller diameter filler material, as that will require less energy to melt.
TIG welding amperage guide
Base Metal
Thickness
Mild Steel
DC Current
Stainless Steel
DC Current
Tungsten Electrode
Diameter
Filler Wire Diameter
(If required)
Argon Gas
Flow Rate
(Litres/Min)
Joint Types
1.0mm
40
-
50
25
-
35
1.0mm
1.6mm
5
-
7
Butt/Corner/Fillet/Lap
1.2mm
50
-
60
35
-
50
1.0mm
1.6mm
5
-
7
Butt/Corner/Fillet/Lap
1.6mm
70
-
90
50
-
70
1.6mm
1.6mm
6
-
8
Butt/Corner/Fillet/Lap
3.2mm
90
-
115
90
-
110
1.6mm
2.4mm
7
-
9
Butt/Corner/Fillet/Lap
4.8mm
140
-
165
125
-
150
2.4mm
3.2mm
10
-
12
Butt/Corner/Fillet/Lap
6.4mm
170
-
200
160
-
180
3.2mm
4.0mm
10
-
12
Butt/Corner/Fillet/Lap
Summary of Contents for JT-300P
Page 1: ......
Page 52: ...52 September 2020 Issue 4 ...