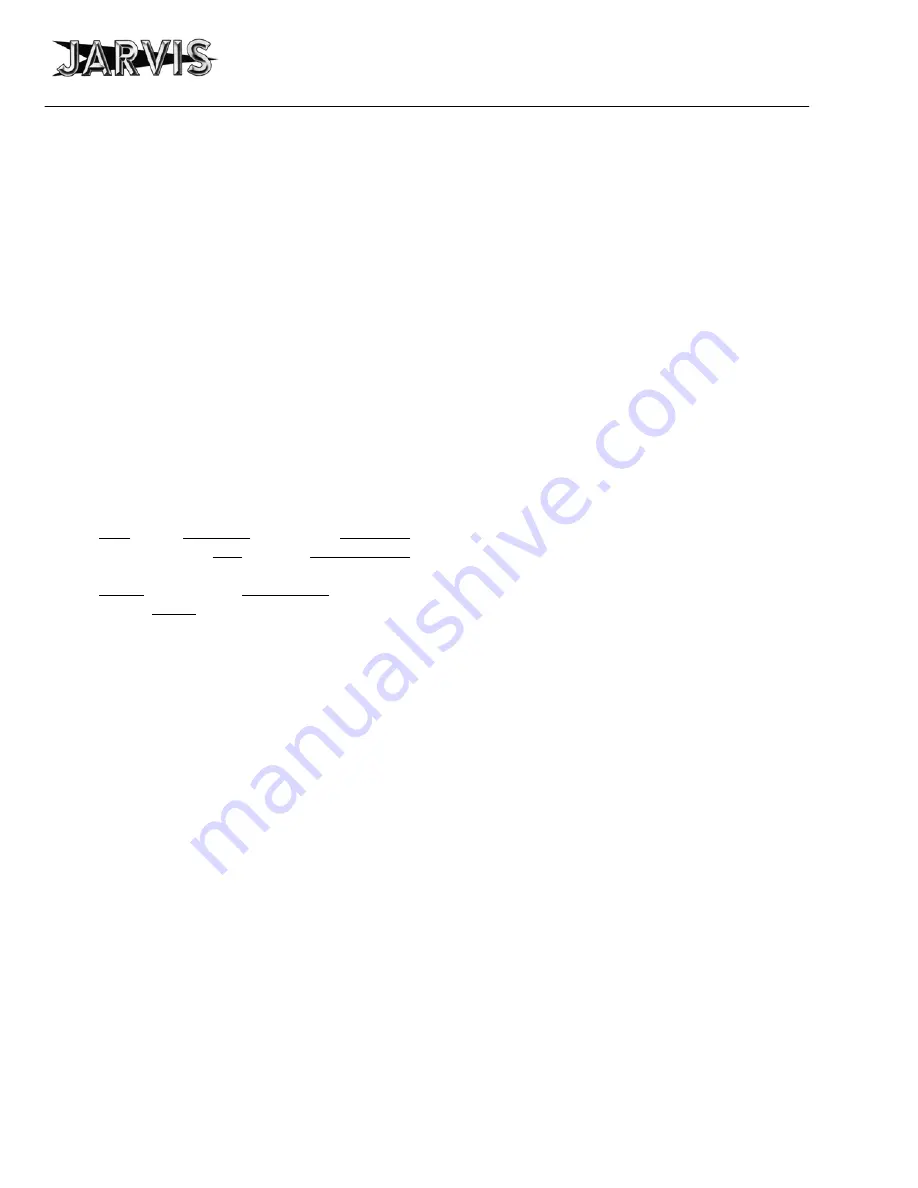
maintenance instructions
Model 1000--FS
page 12 of 16
®
JARVIS
PRODUCTS CORPORATION
33 ANDERSON ROAD, MIDDLETOWN, CONNECTICUT 06457--4926
UNITED STATES OF AMERICA
TEL. 860--347--7271 FAX. 860--347--6978
6207001:::
1.2 Check all fittings for leaks and tighten or replace
as necessary.
1.3 Inspect all electrical cords, cord connectors and
plug assemblies over their entire length for cuts
and abrasions and replace as necessary.
1.4 Check the oil level gage (item 21, Figure D, page
7) on the hydraulic power unit and fill oil reser-
voir if necessary.
1.4.1 Change hydraulic fluid and filter as neces-
sary. Fill the oil reservoir with USDA ap-
proved premium grade hydraulic fluid (vis-
cosity: 200 SUS at 110
°
F / 46 ISO at 38
°
C).
Burnt smelling or foamy fluid should be re-
placed immediately.
1.5 The 1000--FS is equipped with dual anti--tie
down control handles (the front and rear han-
dles). Check for the correct operation of the dual
anti--tie down control handles
daily
:
Depress
each trigger separately and the tool should not
start.
Depress
both triggers simultaneously
(within one second of each other) and the tool
should start.
Release
either or both triggers and
the tool should stop.
If the tool malfunction, re-
pair it or remove it from service immediately.
Always use two hands when starting and stop-
ping the tool. Continue holding the tool firmly
with two hands until the saw blade comes to a
complete stop.
Note: The power supply must be connected to per-
form the above operation only.
1.6 Four times (4) per day, add
Jarvis
1315 White
Grease
to the grease fitting (item 12) located on
gear housing (item 13).
1.7 Thoroughly clean the tool at the end of the day/
shift and spray with an approved mineral oil for
overnight storage.
2 WEEKLY:
2.1 Disassemble, clean and inspect gear housing as-
sembly.
Refer to sections 6 and 7 as a procedur-
al guide.
3 AS NECESSARY:
3.1 Clean and inspect circular blade.
Refer to sec-
tions 4 and 5 for blade removal and installation
procedures.
3.2 Disassemble, clean and inspect motor housing
assembly and motor adapter.
Refer to sections
8 and 9 as a procedural guide.
3.3 Replace the power unit oil filter (item 12, Figure
D, page 7) at regular intervals.
Note:
The hydraulic motor will require only occasional
rebuilding. Do not rebuild the hydraulic motor -- send it
back to
Jarvis
to be rebuilt.
4 CIRCULAR BLADE REMOVAL:
4.1 Remove hex head screw (item 43) and lock
washer (item 42).
Insert an allen wrench or
screwdriver through one of the outer holes in
blade to prevent blade from turning.
4.2 Remove blade retaining flange (item 41).
4.3 Remove circular blade (item 40).
4.4 Inspect all parts for wear and replace if neces-
sary.
4.4.1 Inspect circular blade for wear and sharpen
or replace as necessary.
5 CIRCULAR BLADE INSTALLATION:
5.1 Reverse steps and procedures outlined in section
4.
See notes below. Refer to figure 3 on page 13
as a guide.
5.1.1 To ensure proper fit and safe operation, the
hub of the saw blade (item 40) must face to-
ward and fit securely on the extended lip of
the shaft and pin assembly (item 2).
5.1.2 The holes on the blade retaining flange
(item 41) must align with the four dowel
pins (item 1) on the shaft and pin assembly
(item 2). Make sure the notched areas on the
blade are aligned with dowel pins (item 1).