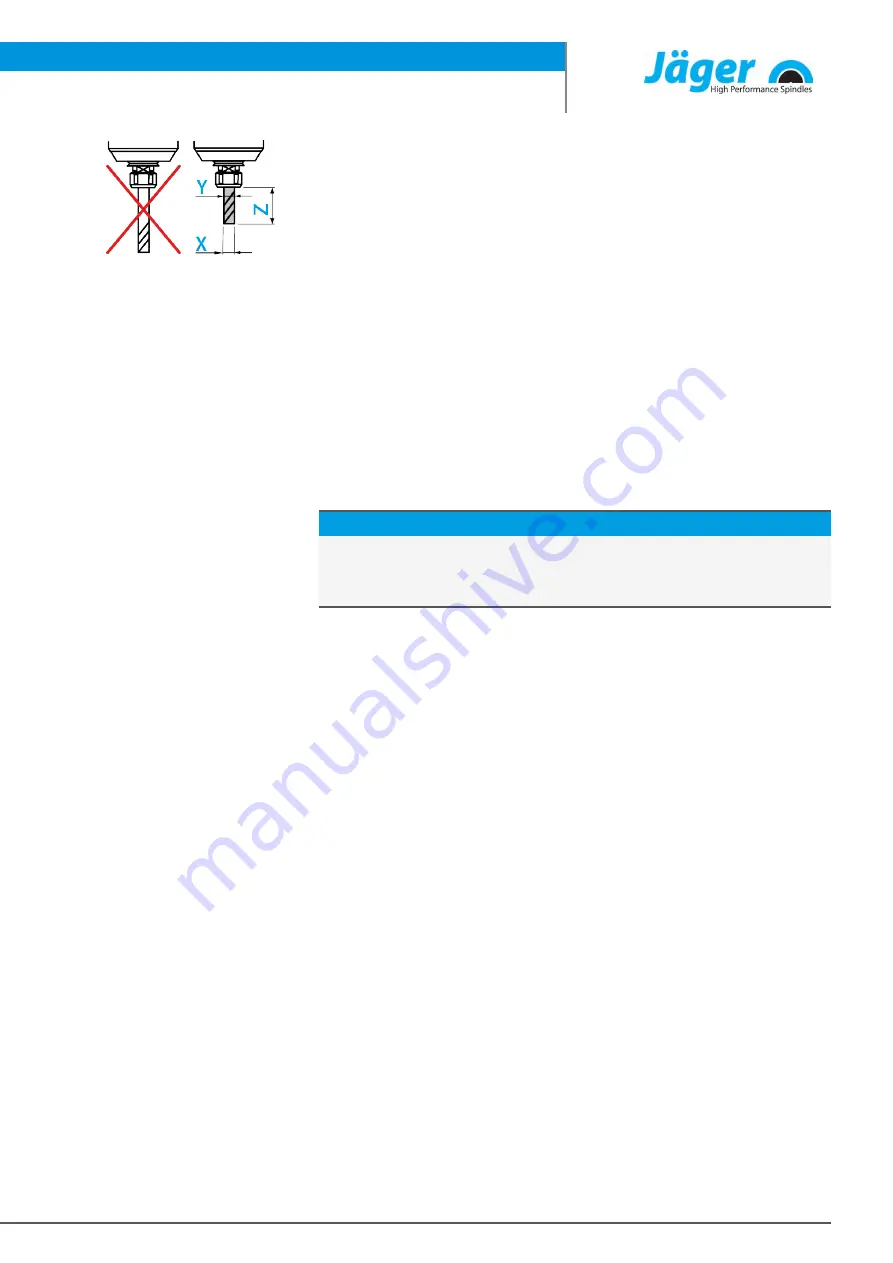
Safety instructions
Item no. 10304014, Revision 02
11 ( 40 )
The tool cutting diameter (X) must not be greater than the maximum
clamping range (Y).
Ü
Always clamp the tool so that it is as short as possible.
Ü
Keep the dimension (Z) small.
Ä
(Y) See section: Technical Specifications
4.2
Shutdown of HF spindle
The procedure for shutting down the high frequency spindle for installation
and maintenance work is as follows:
Ü
Completely disconnect the power supply.
Ü
Completely disconnect the media supply (air and liquid).
Ü
Make sure that the shaft of the HF spindle has come to an absolute stand-
still.
If the HF spindle is being shut down to be cleaned:
Ü
Reconnect only the sealing air.
Tip: Forward the data to the controller.
u
Use the option on the frequency converter of detecting the shutdown
signal from the shaft and forwarding this to the machine controller for
evaluation.
4.3
Installation and maintenance
Ü
Carry out installation, cleaning, and maintenance work only after shutting
down the HF spindle and after the shaft has come to a standstill.
Ü
Install all safety and protective devices of the machine immediately after
completing work.
4.4
Modification and repair
Modifications or alterations to the HF spindle are only permitted after prior
consultation with
Nakanishi Jaeger GmbH
.
Only the service partners listed in the “Service and repair
” section are
authorized to open and repair the HF spindle.
Only approved accessories have been tested for operational safety and func-
tionality.
4.5
Improper operation
The high frequency spindle is only safe to operate for its designated use.
Ü
Observe the safety instructions in all sections of the manual to prevent
hazards to persons, the environment, the machine, or the HF spindle itself.
Failure to observe the safety instructions may invalidate any warranty claims
and compensation claims for damages.