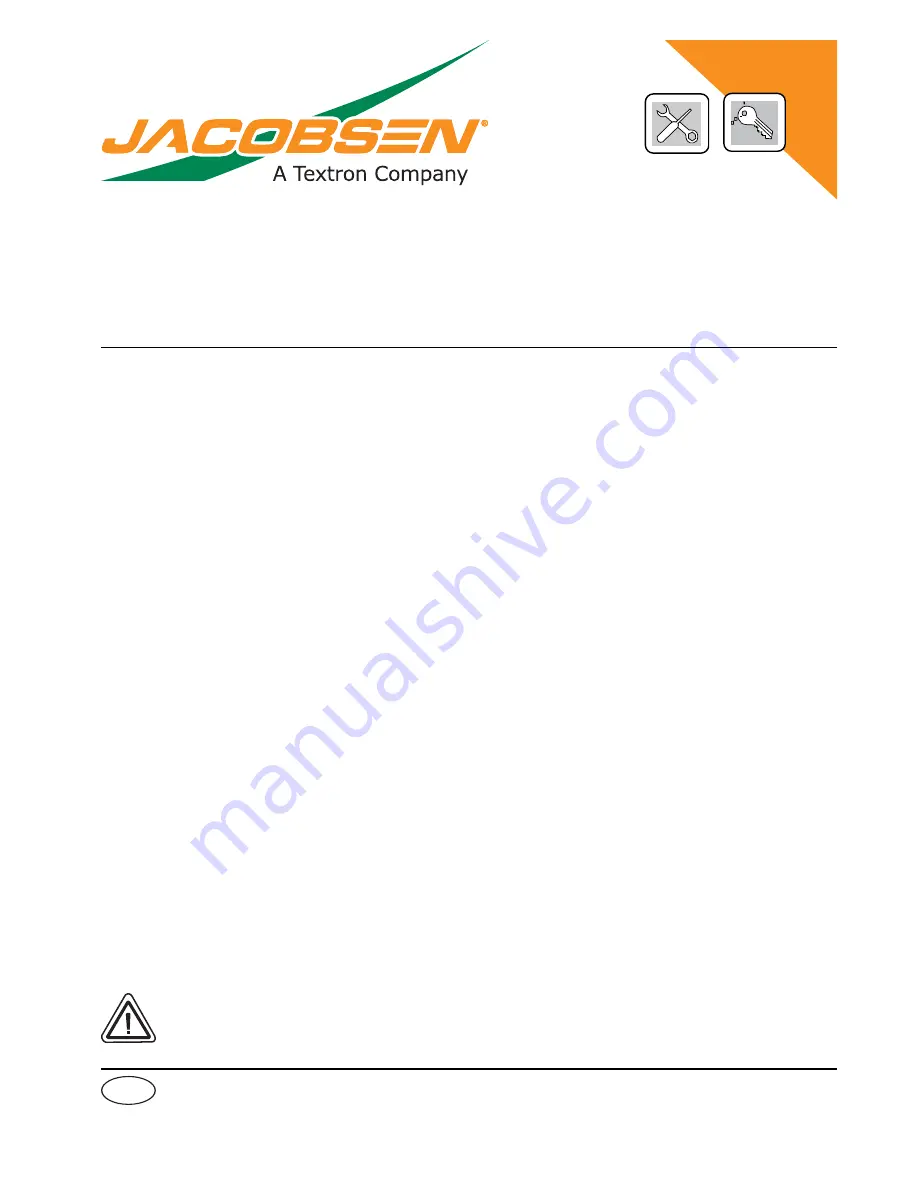
Safety, Operation & Maintenance Manual
WARNING: If incorrectly used this machine can cause
severe injury. Those who use and maintain this machine
should be trained in its proper use, warned of its dangers and
should read the entire manual before attempting to set up,
operate, adjust or service the machine.
GB
United
Kingdom
RJL 100 February 2010
Series: EK
Product code: AR30001
Series: FZ
Product code: AR30002
Series: GX
Product code: AR30003
Jacobsen AR3
24715G-GB (rev.4)
Summary of Contents for AR3
Page 2: ...2010 Ransomes Jacobsen Limited All Rights Reserved...
Page 33: ...en 33 JACOBSEN AR3 SAFETY OPERATORS MAINTENANCE MANUAL 8 MAINTENANCE LUBRICATION...
Page 63: ...en 63 JACOBSEN AR3 SAFETY OPERATORS MAINTENANCE MANUAL 11 TROUBLESHOOTING...
Page 64: ...en 64 JACOBSEN AR3 SAFETY OPERATORS MAINTENANCE MANUAL 12 1 HYDRAULIC CIRCUIT 12 SCHEMATICS...
Page 74: ......
Page 75: ......