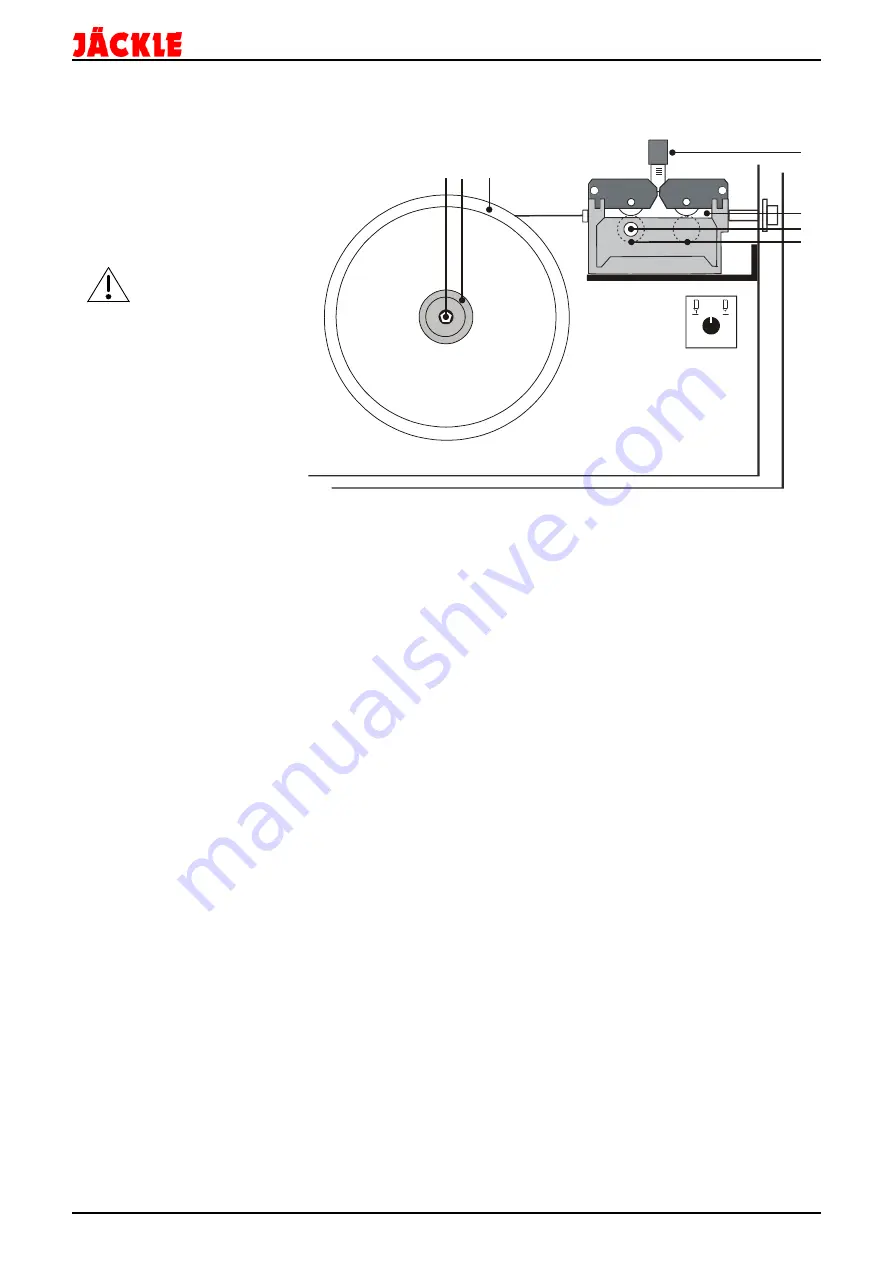
maxiMIG 250/300
Operating manual
Page 22
15. Wire feed unit
Exchange of feed-roller (4)
Depending on the wire used, the
respective feed roller with
matching groove must be set in.
To turn or exchange the feed-
rollers, remove the knurled
screw (5).
Left-hand thread.
Ensure that the groove of the
feed-roller is in true alignment
with the wire guide tube (6).
The
contact pressure exerted by the feed-rollers
is regulated via a star grip (7) in such a way that steady
conveyence of the wire is ensured and, if the wire is
held at the contact tip nozzle, it slides without buckling.
Wire spool brake
The wire-holding arbor (2) includes a spool brake to prevent the wire spool (3) from running on when the wire-
feed motor is stopped. The braking effect is increased by turning the hex socket screw (1) in a clockwise
direction.
Wire conveying inside the torch hose pack
Friction resistance of the welding wire inside the wire guide spiral increases in proportion to the length of the
hose pack. Therefore, the torch hose pack shouldn´t be any longer than necessary.
When working with
aluminum welding wire
, it is advised to replace the wire guide spiral with a Teflon wire
guide core. Length of torch hosepack should not exceed 3 m.
After finishing one coil of wire, it is advised to clean both the wire guide spiral and the wire guide tube by air-
blasting.
The gliding quality of the wire guide spiral deteriorates according to the amount of wire conveyed and the
properties of the wire. If wire conveyance becomes unacceptably worse, change the wire guide spiral.
1 2
3
4
5
6
7
0
1
2
3
4
10
9
8
7
6
5