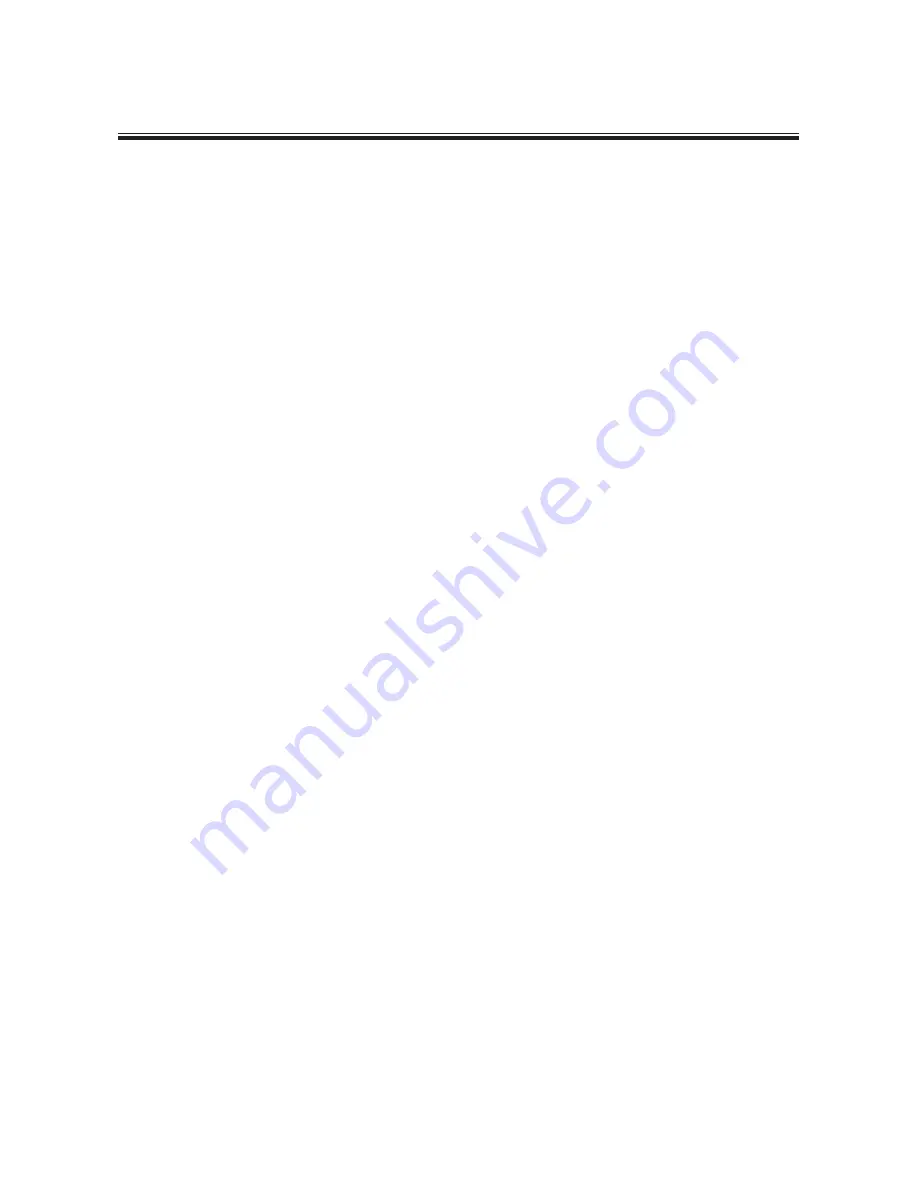
- 35 -
MAINTENANCE SECTION
1. Causes of Troubles and
Troubleshooting ............................... 36
2. Maintenance and Inspection ........... 38
3. Consumable Parts ........................... 39
Handling, maintenance and inspection of the pump shall be limited to the range
covered by and described in this instruction manual. Handling of the pump beyond
the range covered by this instruction manual is prohibited. Iwaki takes no
responsibility for injury to person or damage to assets caused from a failure to
observe this instruction. Contact Iwaki, an Iwaki branch office, or an Iwaki distributor
as necessary.