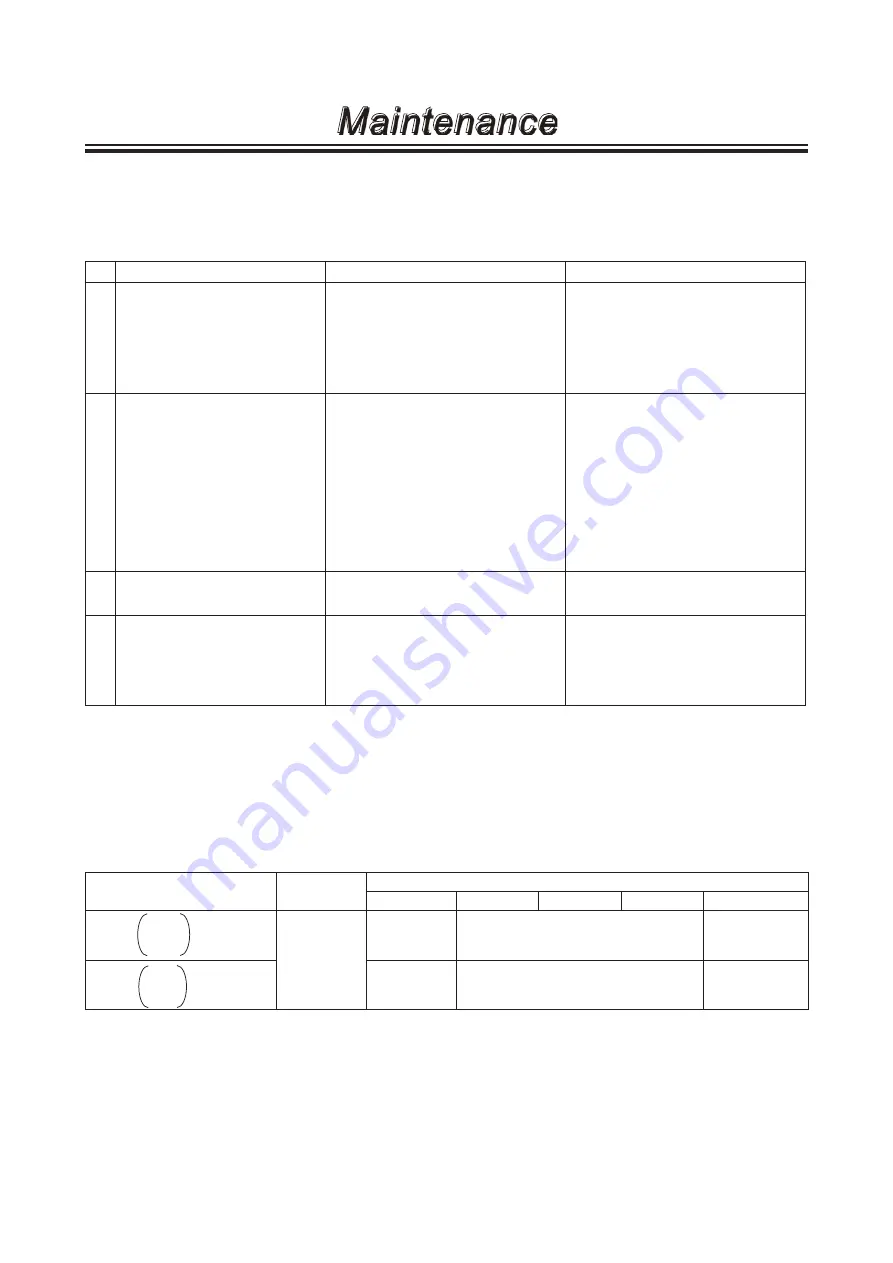
- 26 -
2. Maintenance & Inspection
■ Daily inspection
Pay attention to the following items during operation. Stop operation on sensing danger and solve problems
on the Troubleshooting section.
No.
States
Points to be checked
How to check
1 Operation
● If air is pumped.
● If the suction and discharge
pressure are normal.
● If power voltage and current are
normal.
● Air flow meter, pressure gauge
or visual inspection
● See a spec label.
2 Starting
● If abnormal noise or vibration
occurs. They are signs of abnor-
mal operation.
● A baseplate, if installed, under
the pump may resonate with
operation, making a mechanical
noise. Insert a rubber cushion as
necessary to reduce resonance.
● Visual or audio inspection
● Visual or audio inspection
3
Air leak or ingress from pump
head joints and a suction line
● Tighten a loose joint.
● Air flow meter, pressure gauge
or visual inspection
4
Pump and motor surface tem-
perature rise
● Pump and motor surface tem-
perature should be at or below a
total of ambient temperature plus
50°C.
● Thermometer
■ Wear parts
If pump performance has remarkably reduced, replace diaphragms and valves with new ones.
Wear part duration varies with the pressure, temperature and characteristics of liquid.
The estimated life below is calculated based on continuous operation with clean water at ambient tempera-
ture (Room temperature range is 0-40°C.).
Model
Load range
Estimated life
Valve
Diaphragm
Seat
Gasket
Filter (Option)
450
APN- P450 NAT-NATX
S450
All range
8000
4000
4000
450
APN- P450 NST-NSTX
S450
8000
4000
-
Maintenance
Summary of Contents for APN-450
Page 17: ... 15 Installation 1 Before installation 16 2 Installation Tubing Electrical wiring 19 ...
Page 24: ... 22 Operation 1 Before operation 23 2 Pump operation 23 ...
Page 26: ... 24 Maintenance 1 Troubleshooting 25 2 Maintenance Inspection 26 3 Wear part replacement 27 ...
Page 34: ... 32 ...
Page 35: ... 33 ...