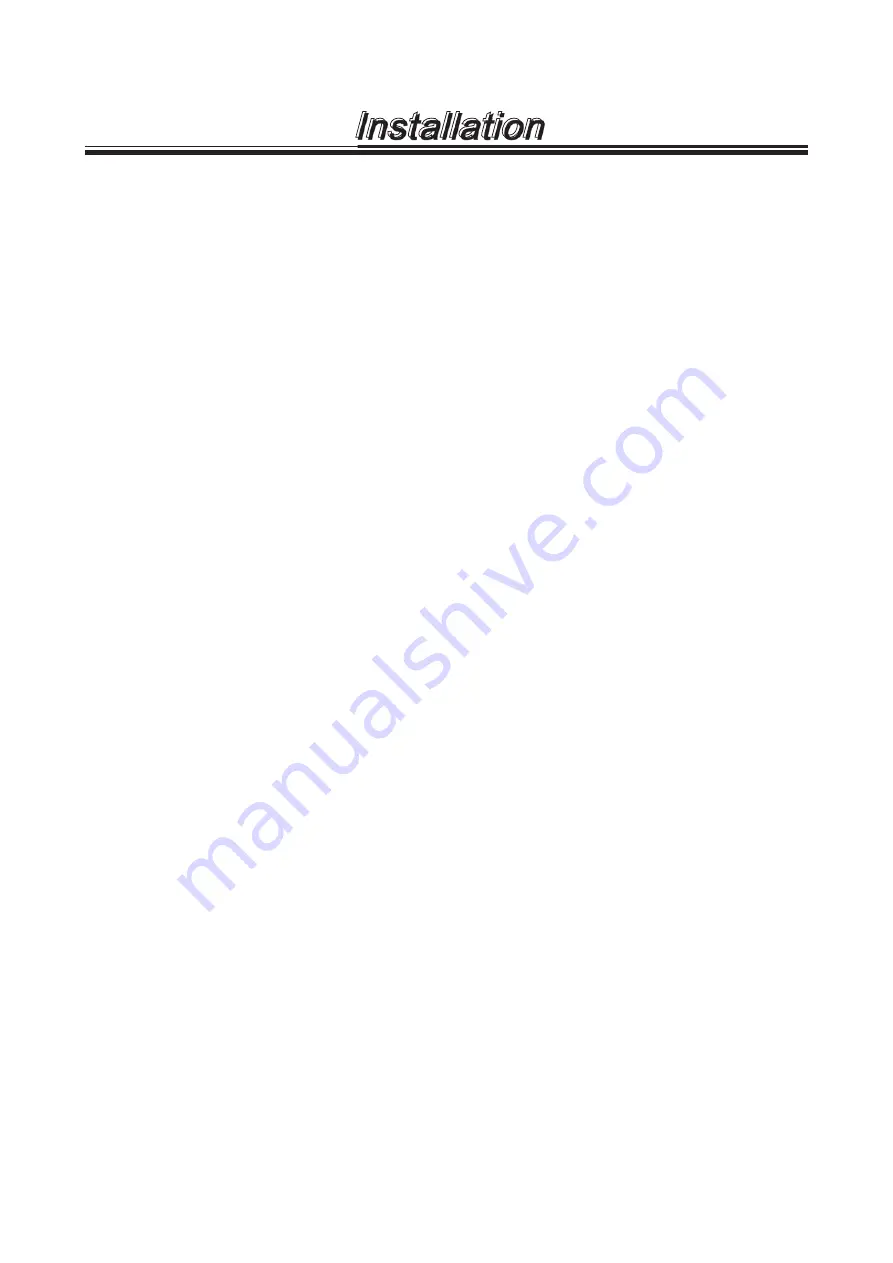
- 13 -
Installation
■
Discharge piping
1. Discharge piping bore
When the discharge piping is long but the piping bore is equal to the pump outlet bore, the specified
performance may not be obtained because pipe resistance becomes high. Calculate pipe resistance in
advance to decide a discharge piping bore.
2. Discharge valve installation
Install a discharge valve on the piping about 1m away from the pump. The air bleed piping should be pro-
vided near the discharge valve in order to prevent the air from remaining.
3. Gate valve installation
Install a gate valve on the discharge piping to adjust flow rate and to protect the motor from overload. If a
check valve is installed, the optimum installation order is : Pump
→
Check valve
→
Gate valve.
4. Pressure gauge
A pressure gauge is required on the discharge piping to check operating conditions such as discharge
capacity and head.
5. Check valve
A check valve is required in the following cases.
• Discharge piping length is between 15 and 20 meters.
• Actual head is higher than 15 meters.
• The distance between the liquid level in the tank and the top end of discharge piping is 9 meters or more.
• Two pumps run in parallel.
6. Air vent
Install an air vent on the discharge piping when the horizontal piping length is between 15 and 20 meters.
7. Drain
Install a drain valve when draining of liquid is required (to protect the pump from freezing, etc.).
8.
Piping support
Support the piping by pipe supports so that the piping weight does not totally weigh the pump.
9. Priming piping
A priming line is required on the discharge piping when piping is not flooded suction.