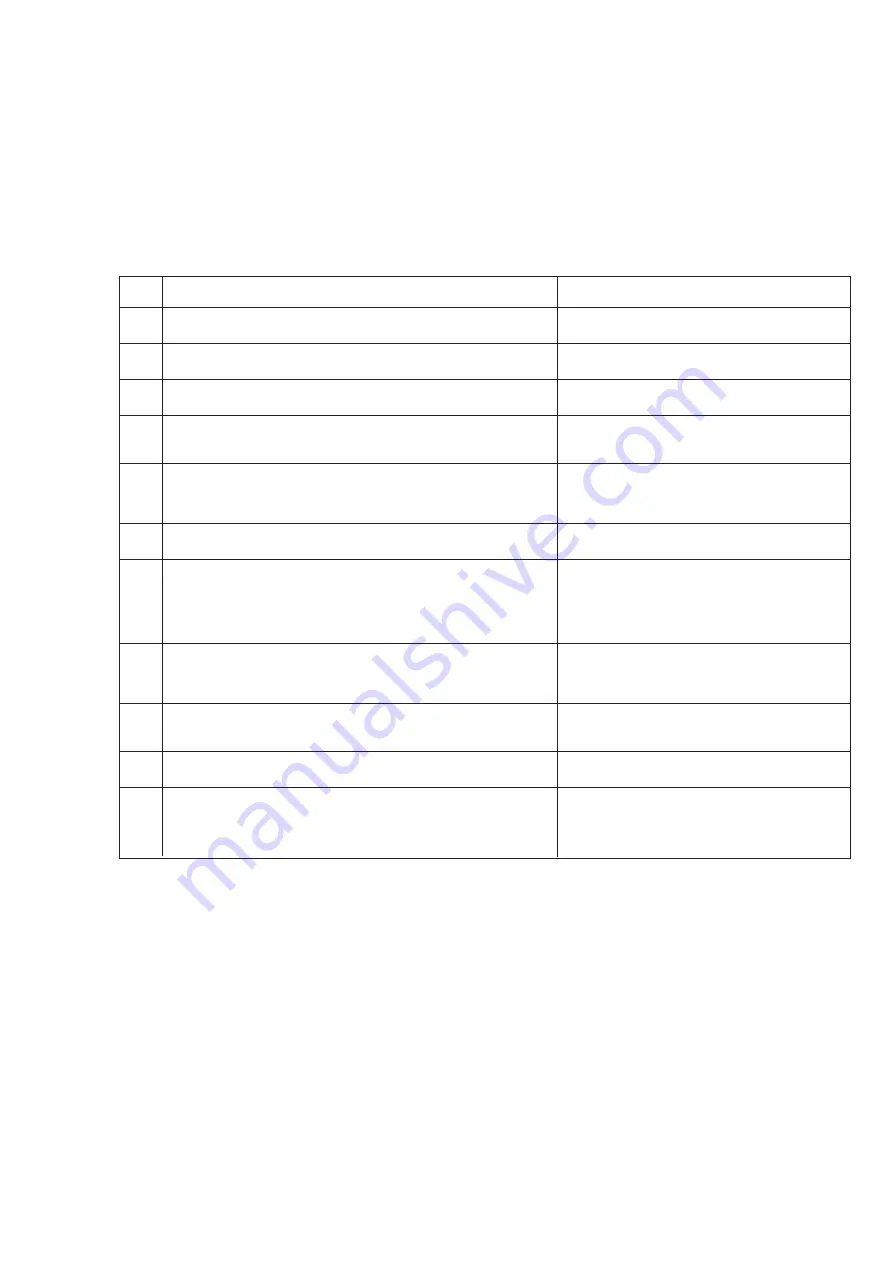
12
8. What if...?
8.1 Error messages
List of possible error messages and their meaning:
This chapter will help you to recognize
malfunctions and take appropriate measures
or, if possible, to perform some repairs.
8.2 Repairs
Repairs may only be carried out by a certified Ivoclar Vivadent Service Center.
Please refer to the addresses in Chapter 10.
If repairs during the warranty period are not carried out by a certified
Ivoclar Vivadent Service Center, the warranty will expire immediately.
Please also read the safety information in Chapter 2.
Error
1
2
3
4
5
6
7
8
9
10
11
Flasks do not close.
The flask covers do not sit on the flask margins.
The model to be invested does not fit in the flask.
The pressure is difficult to be transferred to the flask and/or clamping frame.
Pressure in the clamping frame fluctuates.
Injection plunger enters the capsule and deforms the bottom of the capsule. The material is
extruded at the wrong end of the capsule.
The rod of the injection plunger cannot be moved, even if the connection to the compressed
air source is interrupted. It seems to be stuck.
Injection plunger does not move. The SR Ivocap material is not injected.
The resin flows out of the flask during polymerization.
The locking mechanism is blocked.
The locking mechanism is contaminated with wax.
Capsule reservoir has polymerized after 35 minutes.
Description
Notes for users
Flask margins are not clean; plaster residue on the injection funnel.
The model should be trimmed prior to investment.
Clamping frame is not correctly positioned, i.e. in the centre of the
press.
Compression spring in the clamping frame are old or dirty and cannot
transfer the pressure.
Replace the compression spring or clean the
clamping frame (see Error 12).
The injection plunger is not correctly placed on the capsule. There is
an empty space between the injection plunger and capsule bottom.
Avoid empty space and place the injection plunger evenly on the
capsule bottom.
– No compressed air present
– Capsule cover was not removed
– There is plaster residue or the funnel is blocked, e.g. by plaster
residue
– The injection channels are too narrow.
– The flow properties of the resin are poor because of incorrect
storage
– Leaks as a result of incorrect investment.
– Flask defective.
– Inadequate clamping pressure on the frame.
– A foreign object is stuck between the two flask halves.
The mechanical components are damaged as a result of improper
handling. In case of considerable damage, the mechanical components
must be replaced.
Wax residue in the water bath has contaminated the clamping frame.
Boil out clamping frame with clean, hot water.
– Water level surpasses the marking on the clamping frame.
– An unsuitable polymerization bath was used.
– The system was not placed in cold water immediately after
polymerization.
– Reduce polymerization time by 1–2 minutes if necessary
Negative pressure in the pressure cylinder may prevent the plunger
from moving, open valve
Summary of Contents for SR Ivocap
Page 1: ...Operating Instructions SR Ivocap Equipment System...
Page 2: ...2...
Page 14: ...14...
Page 15: ...15...