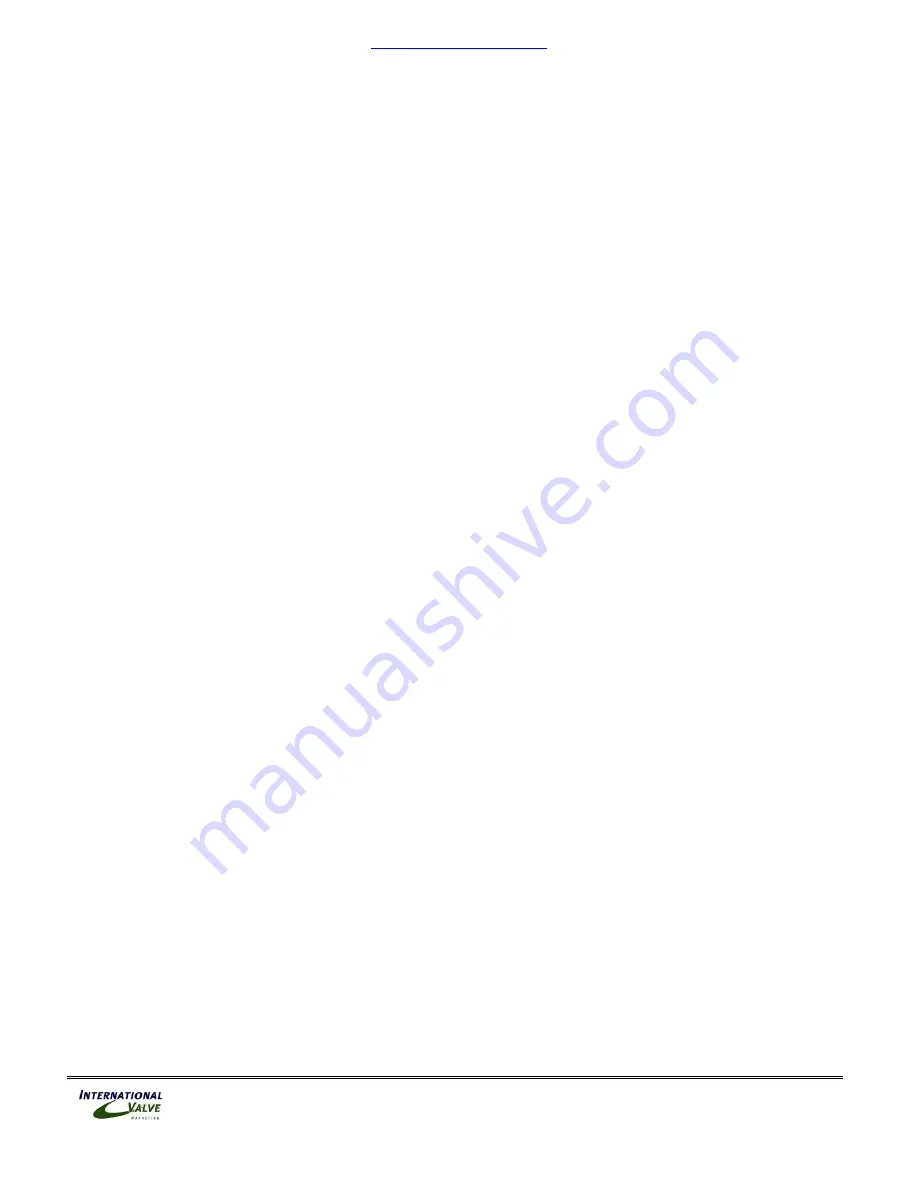
www.internationalvalve.com
INSTALLATION, OPERATION AND MAINTENANCE MANUAL
MODEL SWG, SERIES C, B, V, N
International Valve Marketing, LLC
Page | 9
Last Revision Date: 09/13/2013
(b)
Assembly Procedure
1.
Insert Nozzle Seat (11) in Control Float (6)
2.
Assemble Upper Nozzle Assembly Plate (9), Nozzle (8), and Lower Nozzle Retaining Plate
(10) and attach to Control Float (6).
3.
Assemble Nozzle Float (7) to Nozzle (8). Apply new Teflon tape to Nozzle (8) threads. To hold
Nozzle (8) from rotating, insert a flat screw driver thru the center hole in the Nozzle Float (7)
into the slotted end of the Nozzle (8) OR through one of the slots in the Upper Nozzle
Assembly Plate (9) and attach the Nozzle Float (7). NOTE: The O-Ring on Nozzle Float (7)
should be facing upward.
4.
Insert the assembled Control Float (6) and Nozzle Float (7) inside valve body.
5.
Insert Anti-Surge Float (5) into valve. NOTE: The O-Ring on Anti-Surge Float (5) should be
facing upward, while the multi-orifice Wear Inserts face downward.
6.
Place O-ring in upper Body Flange groove on top of valve body.
7.
Replace top flange assembly of valve (4). NOTE: Do NOT slide flange into place. Place in a
downward motion to align top flange and valve flange bolt holes. Inspect flange mating to
assure O-ring has not moved out of the O-ring groove.
8.
Assemble nuts, bolts and washers.
9.
Tighten nuts, bolts, and washers in a 12 O-clock, 6-O-clock, 3- O-clock and 9-O-clock fashion
by hand until all bolt/nut assemblies are hand tight. Tighten nuts and bolts again with a
wrench. Locate washers on the nut-side of the flange.
10.
Follow standard flange tightening procedures,
11.
Apply sealing tape to side ports and tighten cap, ball-valve or pressure gauge onto valve
ports.
(c)
Maintenance Schedule
Because pipeline conditions vary greatly from installation to installation, a dynamic maintenance
schedule should be implemented to ensure proper valve functioning, to avoid rendering the
valve inoperable due to a buildup of fats, oils, grease and other debris and to prevent valve
leakage. The development of a proper and effective maintenance schedule is accomplished by
periodic inspection and evaluation of the installed valve combined with a corresponding
adjustment to the maintenance interval.
To best determine the appropriate maintenance interval, periodic inspection for proper function
can be performed by placing a listening device or an ear near the valve and/or valve vault at
pipe-line start-up. If audible air release and valve closure is noted, the valve is functioning
properly.
Upon installation, each Vent-Tech valve should be maintained and evaluated by a certified
system maintenance mechanic after 30 days by following the assembly procedures listed in this
section. Depending on the condition of the valve and the requirements of the application, the
maximum maintenance interval can be extended in 30 day increments up to a maximum
maintenance interval of 1-year.