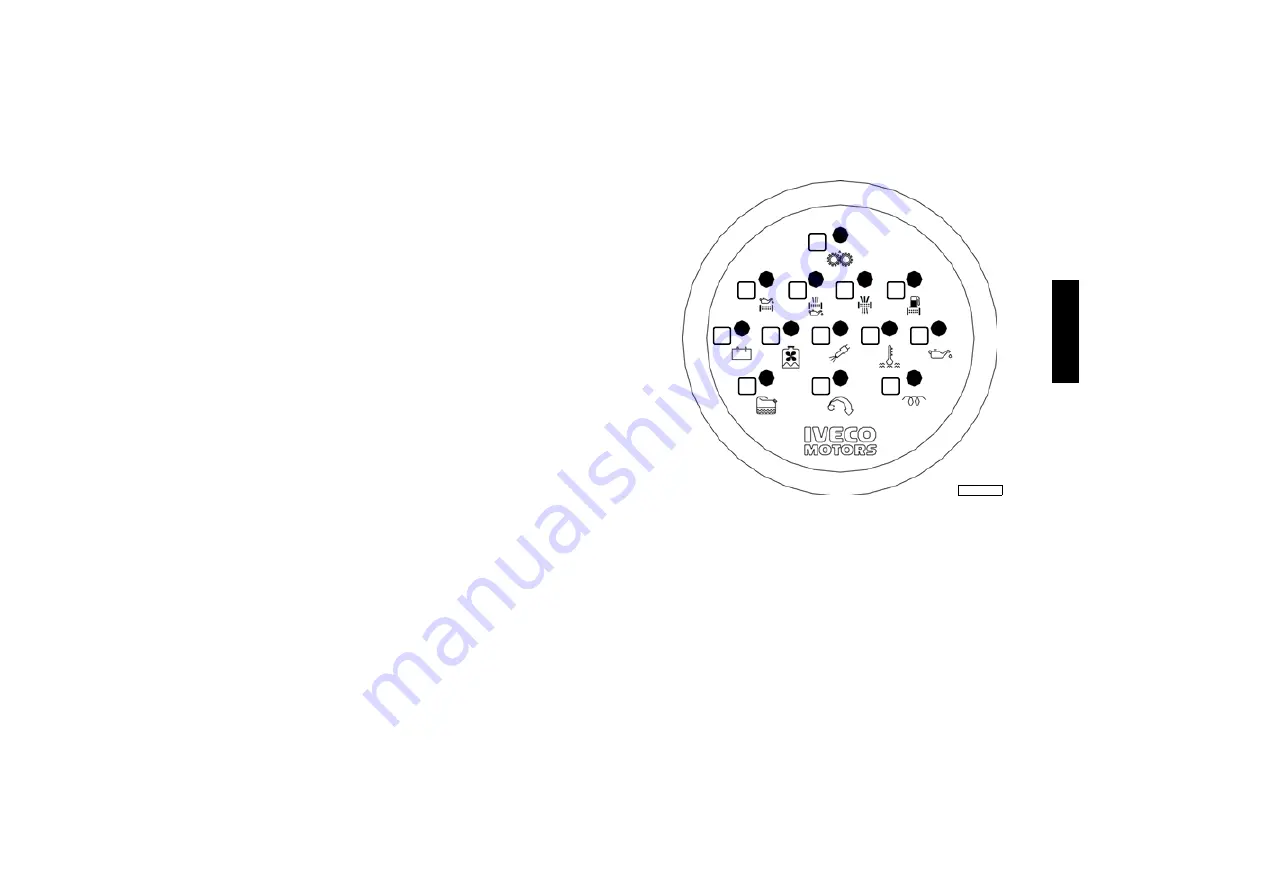
15
ENG
L
ISH
RECOGNISING ALARMS
IVECO MOTORS on-board control panels with analogue instruments
are fitted with an electronic module that includes the indicator lights
and the interface, timer and alarm storage circuits.
The figure illustrates the dial and the key indicates the meaning of the
alarm signals sent by all the indicator lights; some types of engine and
relevant equipment only make some of the above mentioned
functions available.
If the Boatyard uses different technical options there may also be
changes to the above.
Operation
When the key switch is turned to position
8B
the signals and alarms
module will perform an efficiency test on all the indicator lights, lasting
5 seconds, with the exception of the “Pre-lubrication”, “Pre-post
heating”, “EDG system malfunction” indicators, and simultaneously the
beeper sounds.
It is possible to stop the beeper before the end of the test, by pressing
the relevant button.
During start-up and for the following 15 seconds, all alarm functions
are disabled; after this period, each alarm detected by the sensors
provided on the engine will result in the relevant indicator flashing and
a simultaneous warning sound from the beeper. If the beeper is
disabled by pressing the relevant button, the indicator light will turn on
without flashing and the alarm will be stored until the engine is next
stopped.
1. Maximum allowed rotation speed exceeded (on request) - 2.
Water in the fuel pre-filter - * 3. Engine coolant level low - 4.
Alternator malfunction - *5. Oil filter blocked - *6. Oil vapour filter
blocked - *7. Pre-lubrication in progress - 8. Air filter blocked -
*9. Fuel filter blocked - 10. Coolant temperature high - 11. Oil
pressure low - *12. Pre-post heating - *13. Malfunction in EDC
electronic injection system.
*Alarm functions not available with standard setup.
1
2
12
11
10
13
3
4
5
6
8
9
7
04_234_N
Summary of Contents for N45 MNA M10.00
Page 1: ......