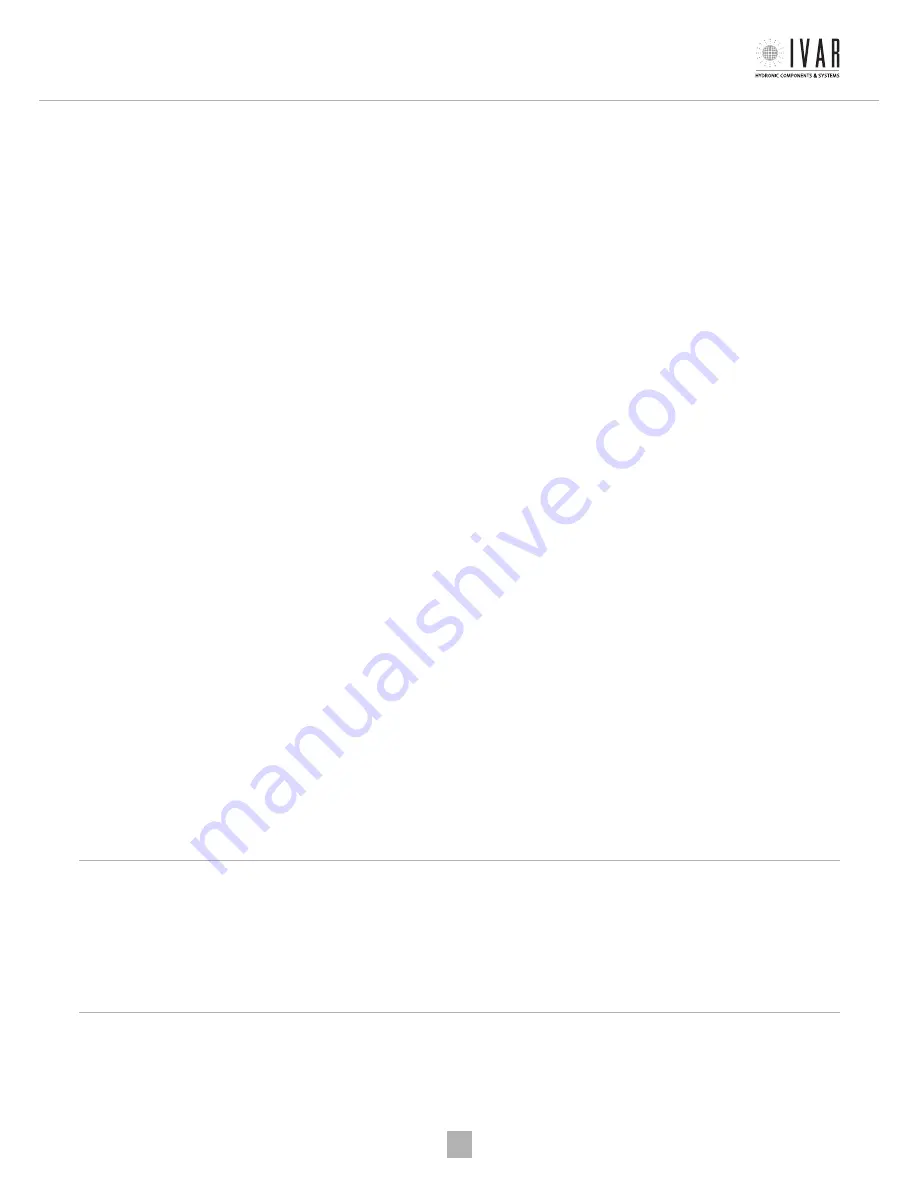
5. Enter the chart or the table in Fig. 8 by the Kv
b
value obtained at the previous step, and obtain the correct number of turns from closure position.
The secondary by-pass is equipped with double micrometric adjustment with position memory in case of temporary closure. With reference to Fig. 6, proceed
as follows:
1. Remove the plug;
2. Use a screwdriver to unscrew and extract the notched screw located within the hexagonal key-way;
3. Use a 5 mm Allen key to close the valve (Fig. 6a);
4. Screw the notched screw all the way back in. Then mark the adjustment reference point with an ‘x’ (Fig. 6b);
5. Align the screwdriver with the ‘x’. Then loosen the screw (Fig. 6c) by the proper number of turns, previously estimated;
6. Fully open the by-pass valve until mechanical stop (Fig. 6d). The pre-setting is now complete and it will not be altered in case of repeated opening and
closing with the Allen key;
7. Put the plug back.
Secondary by-pass rough adjustment
As an alternative to accurate pre-setting, it is possible to make a rough adjustment of the secondary by-pass by proceeding as it follows:
1. Drive the 3-port mixing valve completely open without mounting the actuator;
2. Open the balancing secondary by-pass completely (B8 in Fig. 2);
3. Check that the boiler water temperature stabilises above the design flow temperature of the heating system;
4. Let the water flow through the system and monitor the users’ flow temperature through the flow thermometer.
One of three cases can occur:
A If the flow temperature is close to the design temperature, the setting is complete;
B If flow temperature is below the design temperature, gradually close the secondary balancing by-pass (B8 in Fig. 2), while monitoring changes in the
flow temperature, until it stabilises to the design value;
C If flow temperature is above the design temperature, the boiler temperature should be reduced until the flow temperature reaches the design
temperature; repeat the procedure if necessary.
Mounting the mixing valve actuator
Once the secondary by-pass has been adjusted, the mixing valve control actuator can be mounted. The device will react dynamically to any change in
heating load. The mixing valve can be controlled either with fixed point regulation, performed by means of a thermostatic head with capillary sensor, or with
weather-compensated regulation, by means of an electric actuator and a suitable controller. With reference to Fig. 5, thermostatic head (2) or servomotor (3)
are mounted on the 3-port mixing valve (1).
• In case of fixed point adjustment, immersion sensor (4) of the head must be put into the dedicated pocket (5). Thermostatic head T5011U is included
in
MULTIMIX-C
units having ‘T’ in product code (e.g. 508134PETC).
• In case of electronic control, a contact sensor is usually fastened directly to the flow manifold or to the flow pipe (if it is in metal), according to the
instructions reported in the controller’s manual.
MULTIMIX-C
versions having ‘M’ in the product code (es. 508134PEMC) are ready for modulating
adjustment with electronic servomotor (not included).
Working limits
For a good operation of the system, it is strongly recommended that the following limits are not exceeded:
1. Max primary flow rate through separator/manifold: 3000 l/h
2. Max secondary flow rate through distribution kits: 1700 l/h
In cooling applications,
MULTIMIX-C
should not be used with fluid temperature below 16
◦
C to prevent condensation.
Design information
The charts of the flow coefficients of the different components of the booster kits are reported in Fig. 8 and Fig. 9. Kv values are expressed in m
3
/h/bar
0.5
.
Each kit is supplied with variable-speed electronic pump, whose characteristic curves can be found in Fig. 7.
9
300427-7-2016