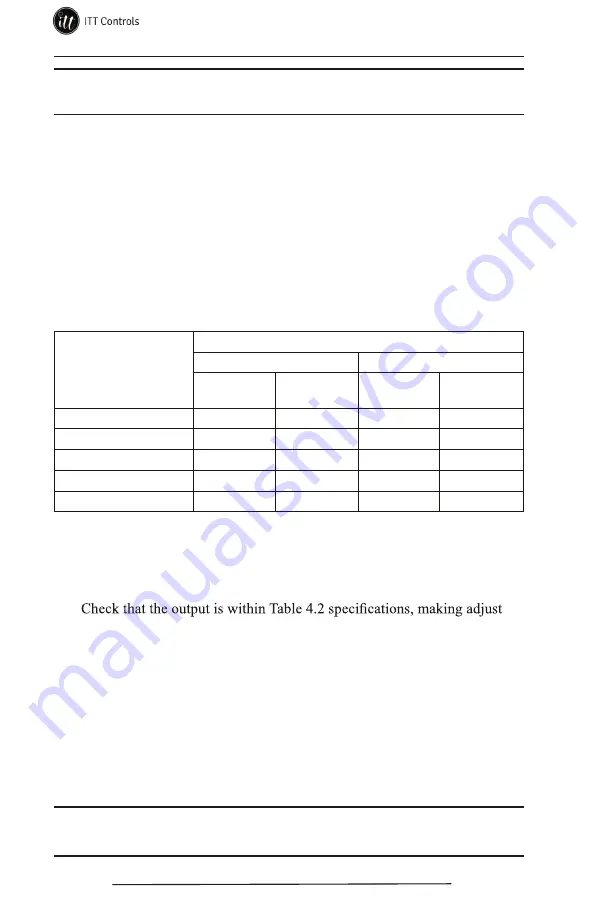
20
Section 4
Model 763A Gage Pressure Transmitter
IMPORTANT: If there are no calibration access plugs in the cover, the cover must be
removed to adjust calibration (see Transmitter Cover Removal,
page 21
).
3. Connect the electrical readout device to the transmitter as shown in
Figure 3.5,
page 17
for either current or voltage readout. If the transmitter
is equipped to an EGS Quick Disconnect connector assembly, secure the
two mating connectors with the bayonet ring (see
page 22
for details).
4. With minimum calibration pressure applied, check the output signal.
Table 4.2 presents the transmitter output values in current or voltage,
along with the associated tolerance, for both the 4-20 mA and 10-50 mA
variations.
5. If the output signal is not the required reading, adjust the zero control
potentiometer in the compensating direction.
Table 4.2—Calibration Checkpoints
Applied Calibration
Pressure Checkpoint
(% of Full Scale)
Output*
4-20 mA Transmitter**
10-50 mA Transmitter***
Current
(±0.08 mA)
Voltage
(±0.04 Vdc)
Current
(±0.2 mA)
Voltage
(±0.04 Vdc)
0%
4 mA
2 Vdc
10 mA
2 Vdc
25%
8 mA
4 Vdc
20 mA
4 Vdc
50%
12 mA
6 Vdc
30 mA
6 Vdc
75%
16 mA
8 Vdc
40 mA
8 Vdc
100%
20 mA
10 Vdc
50 mA
10 Vdc
*This value includes the effects of conformance (non-linearity), deadband, hysteresis, and repeatability.
**This value was obtained using a 500-Ohm load resistor.
***This value was obtained using a 200-Ohm load resistor.
6. Repeat steps 4 and 5 at eight or more checkpoints (pressures) from
minimum to full-scale calibrated pressure and back to minimum pressure.
-
ments to zero and span potentiometers as required.
7. Replace the calibration access plugs as follows (or if the cover has no
calibration access plugs and was removed, see
page 21
for instructions on
replacing the cover).
a. Replacement of the calibration plug O-rings is recommended (coat
with a small amount of silicone grease). If the O-rings cannot be
replaced, verify that the ring surfaces have no damage and coat them
with a small amount of silicone grease before reinstalling.
b. Install the calibration plugs.
c. Tighten the plugs until they are snug (no applicable torque values).
IMPORTANT: The plugs should be tightened only to prevent loosening due to vibration
without interfering with zero and span potentiometer adjustments.
www.ittcontrols.com