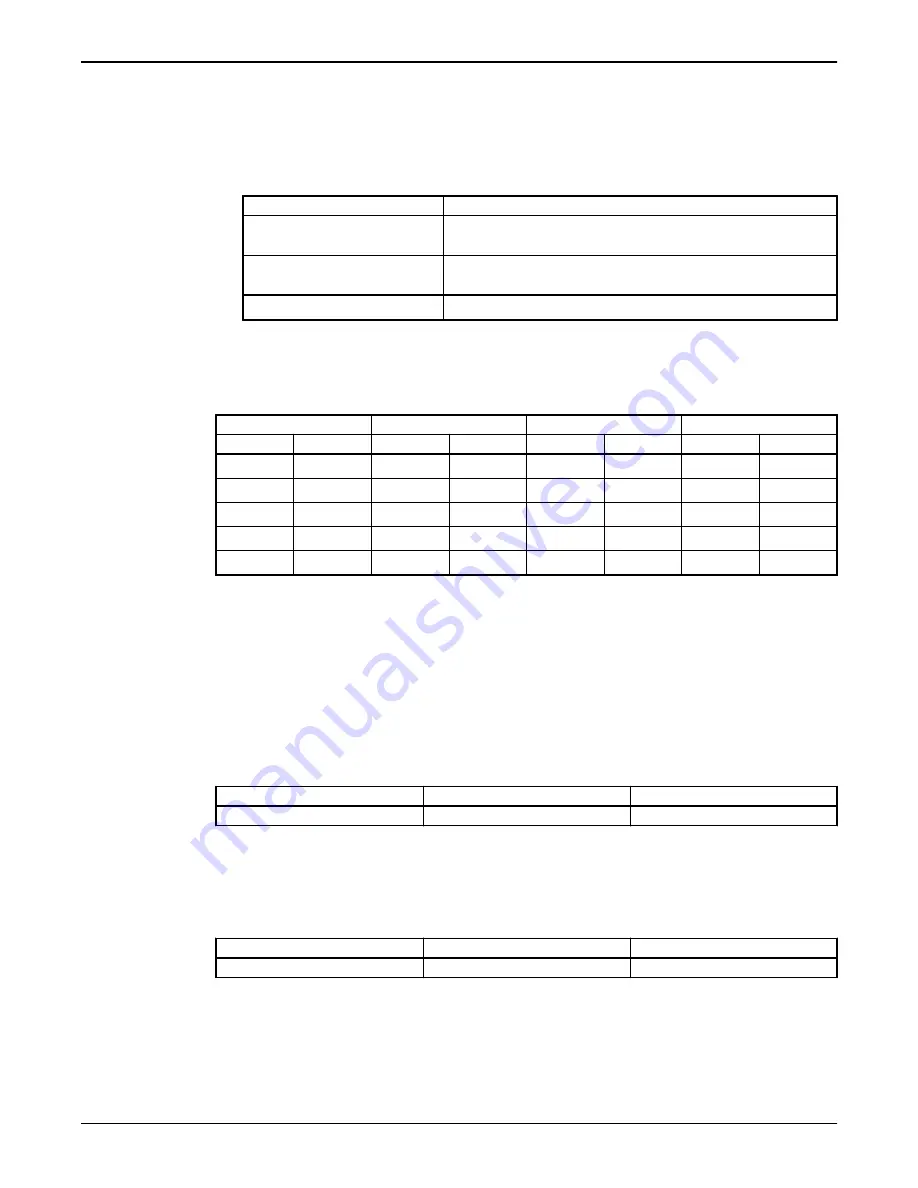
For more information, see Fastener torque table for valve body to topworks in this manual.
4. Make multiple crisscross passes to build up torque to the final table value. Make additional crisscross
passes using final table values to evenly tighten each fastener to within 5% of torque value.
5. Retighten the bonnet fasteners as noted above at ambient conditions after the system has cycled
through operating pressure and temperature.
6. Monitor the valve for leakage:
If leakage ...
Then ...
Occurs at the body/bonnet
flange sealing area
Depressurize the system and retighten the bonnet fasteners as
noted above.
Continues
Depressurize the system and retighten the bonnet fasteners as
noted above. (maximum 3rd re-torque)
Continues
Replace the valve diaphragm.
For more information, see Replace the valve diaphragm in this manual.
Fastener torque table for valve body to topworks
Values given are for lubricated fasteners.
Valve size
Bolt size
PTFE diaphragm
Elastomer diaphragm
Inch
DN
Imperial
Metric
in-lb
N-m
in-lb
N-m
0.50
15
1/4"
M6
25-60
2.8-6.8
20-40
2.3-4.5
0.75
20
1/4"
M6
50-65
5.7-9.1
20-50
2.3-5.7
1.00
25
5/16"
M8
65-90
7.4-11.3
45-70
5.1-7.9
1.50
40
3/8"
M10
200-225
23-25
75-130
8.5-14.7
2.00
50
7/16"
M12
225-275
25-31
100-180
11-20
Guidelines
• Minimum values given will provide a longer diaphragm cycle life for valves in non-autoclave and low
thermal cycle conditions.
• Maximum values given may be necessary for autoclave conditions and for high thermal cycle
conditions.
• Torques should be applied at near ambient conditions (less than 100ºF (38ºC)).
Actuator operating pressure
Maximum permitted air supply pressure
psig
bar
kPA
90
6.2
620
Actuator pressure rating
The actuator will withstand pressures well in excess of the rated pressure without risk of bursting.
Maintaining operating pressure at or below the pressure rating will ensure optimum life of the operating
components, such as the actuator diaphragm. However, operation at pressures up to 100 psig (6.9 bar), for
limited periods of time, will not noticeably affect the life of these components.
psig
bar
kPA
90
6.2
620
Set the adjustable opening stop
These instructions are for series 3, 5, 8, 16 actuators.
1. Remove the switch package, if present.
2. Using air pressure and a bleed type regulator, open the valve to the desired position.
Installation
Advantage
®
Actuator 2.0 Installation and Operation Manual
13