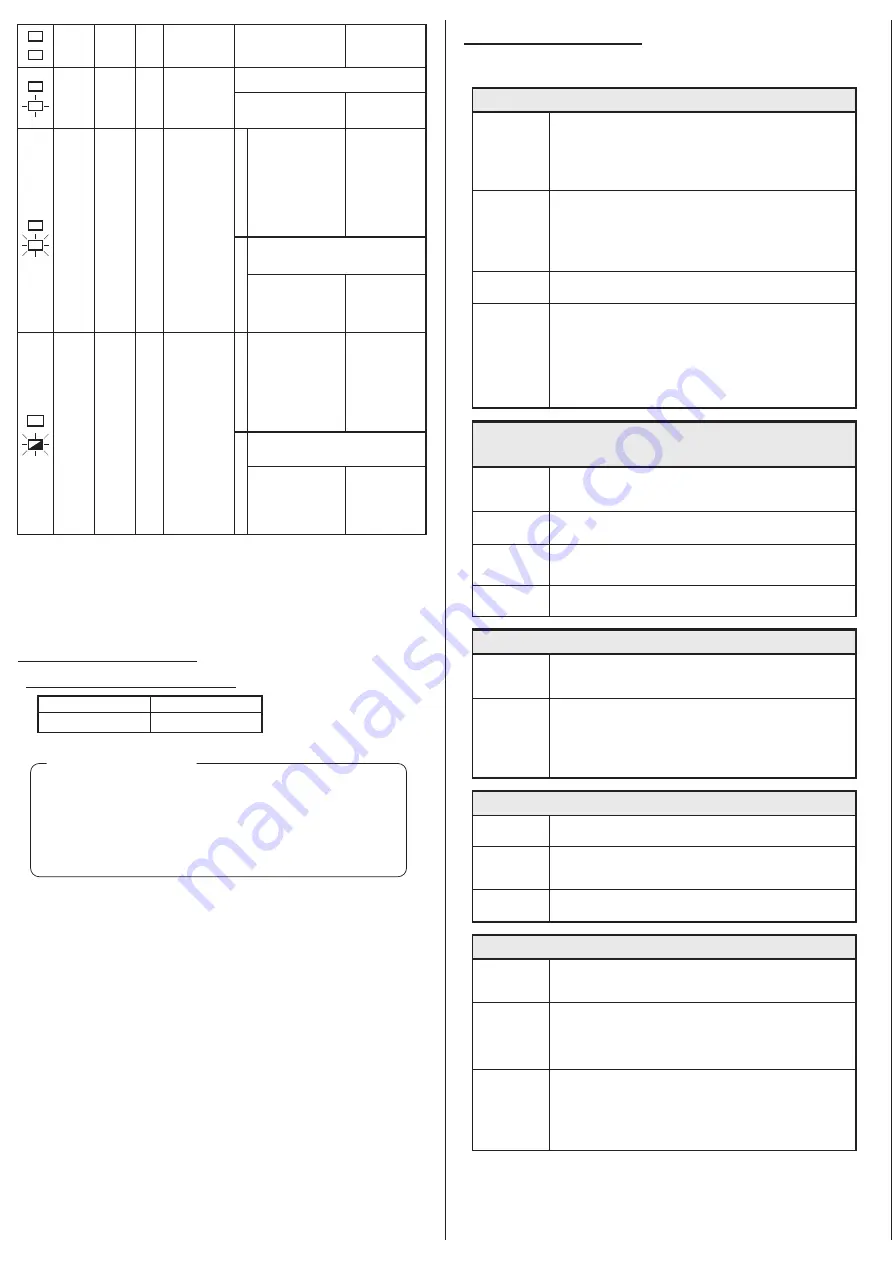
10.
Troubleshooting
Servo Lock Brake torque and current
※
Follow the procedures below without removing plastic cover or modifying the
driver card, in case any problem happened.
9.
Servo Lock Brake
・
Hold Power Moller stop position when the Servo Lock Brake function
is working.
・
Move back to original stopped position when Power Moller force to
be moved by external force.
・
This feature is useful for conveyor where Power Moller is turned by
external force.
(Decline, Incline conveyor...etc)
Symptom 1; Power Moller does not run.
Power
RUN signal
Error
Power Moller
・
Check if only LED1 (Green) illuminates.
・
Check if 24VDC stable voltage is adequately supplied from
the power supply.
・
Check if the wiring to CN1 connector is made correctly.
・
Check if 24VDC cable is adequately wired to the CN1
connector.
・
Check if RUN signal is injected to CN2-1.
・
Check if signal is injected to CN2-1 is proper voltage.
0V for NPN setting, 24VDC for PNP setting.
・
Check if the wiring is adequately made to CN2-1 connector.
・
Check if the 0V injected to CN2-1 is common to 0V injected
to CN1-2.
・
Check if LED2 is illuminating or blinking. If this is the case,
see section 8 and remove the cause of error.
・
Check if the Power Moller is adequately installed and its
shaft are adequately fixed with the supplied mounting
brackets or accessories.
・
Check if the Power Moller end housing is NOT contacting
conveyor frame.
・
Check if the Power Moller’s connector is
properly inserted to the driver card.
・
Check if the belt tension is not too strong.
・
Check if the number of slaved idler rollers are adequate.
Symptom 2; Speed variation is not achieved, or speed is slower
than expected.
Power Moller
SW
1
-2
setting
Power
CN2-3
・
Check if the nominal speed of the Power Moller to se if the
right model is used to achieve the speed variation or to
reach expected speed.
・
Check if the SW1-2 is set properly: ON for external speed
variation and OFF for internal speed variation.
・
In case of external speed variation, check if the 0V is
common to the 0V input to CN1-2.
・
Check if the stable 24VDC is supplied.
・
Check if the wiring is adequately mode to CN2-3 connector.
・
Check if the analog voltage input is made between 0 and 10V
Symptom 4; Error Signal Not Discharged.
SW
1
-4
Voltage
CN2-4
・
Check if the setting is made properly for discharge on
normal or discharge when error arises.
・
Check if the external voltage is 24VDC or less and its 0V is
common to the 0V input to CN1-2.
・
Check if the load(resistor) larger than 1k
Ω
is mounted.
・
Check if the wiring is adequately done to CN2-4.
(
Wired for NPN or PNP)
Symptom 5; Error signal is often discharged.
LED 2(Red)
Environment
Power Moller
・
Check if LED 2 (Red) is blinking. If this is the case, thermal,
lock, low voltage or Back EFM error is arises. See section 8
・
Check if power supply is enough capacity. See section 2
・
Check if the product is used in the ambient temperature
range between 0 and 40
℃
.
・
Check if the driver card back plate is affixed to the metallic
plate face for better heat dissipation.
・
Check if the Power Moller is stalled in the conveyor line.
・
Check if the Power Moller end housing is contacting the
conveyor frame.
・
Check if the Power Moller’s connector is properly inserted to
the driver card.
・
Check if the Roller cable is disconnected, or about to
disconnect.
Symptom 3; Reversing is not achieved.
CW/CCW
SW
1
-3
・
Check if 0V is injected to CN2-2, and it is common to the 0V
input to Cn1-2.
・
Check if the wiring is adequately made to CN2-1.
・
Check if DIP-SW1-3 is not changed during the Power Moller
running.
The Power Moller can not be reversed by DIP SW1-3 during
the Power Moller is running. First stop the Power Moller
and then change DIP SW1-3, or use CN2-2 for reversing
direction.
(
9
)
(
8
)
※
PM486FE-60
type
Error can also be reset by shutting off the power for 2second or over.
※1
High voltage may be generated by turning the Power Moller over speed setting.
※1
Max brake torque
2.0 N
・
m
1
(
A
)
Max current
Servo Lock Brake…
※
Discharge
Open
STOP
Discharge
Open
STOP
Discharge
Open
STOP
Discharge
Open
STOP
See section 5
Automatic recovery setting
Automatic recovery setting
Manual recovery setting
Manual recovery setting
MDR connector
unplugged
Shut off the power off
and re-plug connector
properly.
Motor stall for
4 seconds
Inject signal RUN-STOP-RUN order to CN2-1
to reset the error and restart.
Inject signal ON-OFF-ON
or OFF-ON-OFF order to
CN2-2
Inject signal RUN-
STOP-RUN order
to CN2-1
Supply voltage
less than 18VDC.
(Under voltage
error)
Secure the stable
supply voltage 18VDC
or more.
Restart
immediately
Restart
immediately
First secure the stable supply voltage 18VDC
or over, then inject signal RUN-STOP-RUN
order to CN2-1 for error reset and restart.
First secure the stable
voltage 18VDC or over,
then inject signal ON-
OFF-ON or OFF-ON-
OFF order to CN2-2
Inject signal RUN-
STOP-RUN order
to CN2-1 to restart.
Supply voltage
more then 40VDC
for 2sec or 60VDC
for 0.1sec into the
Power Moller.
(Back EFM error)
The voltage into the
Power Moller is less
than 30VDC.
Inject signal RUN-STOP-RUN order to CN2-1
after the voltage into the Power Moller is les
than 30VDC.
Inject signal ON-OFF-
ON or OFF-ON-OFF
order to CN2-2 after
the voltage into the
Power Moller is les
than 30VDC.
Inject signal RUN-
STOP-RUN order
to CN2-1.