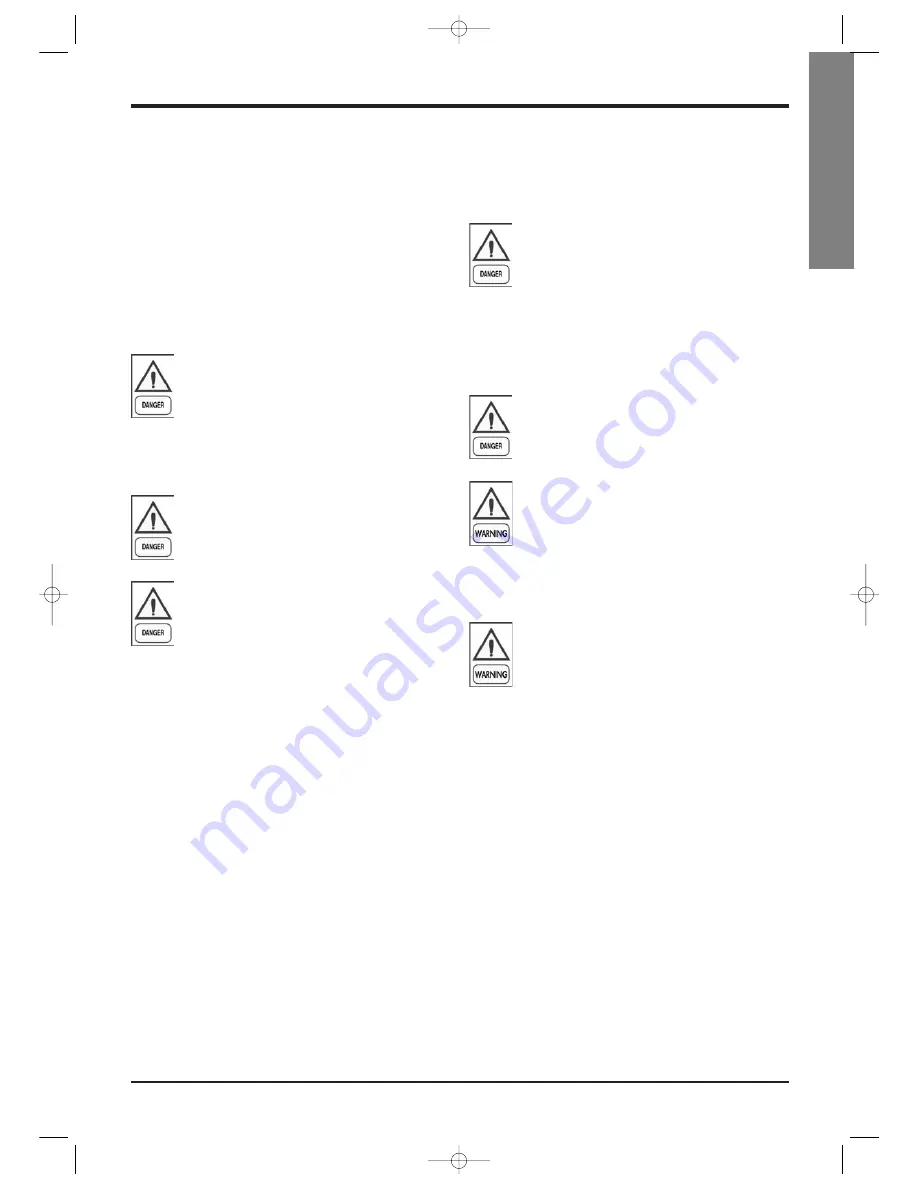
Page 3
English
Safety
2
SAFETY
2.1
Foreword
These units must be installed in conformity with the
provisions of Machinery Directive 98/37/EC, Low
Voltage Directive 73/23/EC, Pressure Vessels Direc-
tive 97/23/EC, Electromagnetic Interference Direc-
tive 89/336/EC, as well as with other regulations
applicable in the country of installation. If these pro-
visions are not complied with, the unit must not be
operated.
The unit must be grounded, and no installa-
tion and/or maintenance operations may
be carried out before deenergising the elec-
trical panel of the unit.
Failure to respect the safety measures mentioned
above may result in electrocution hazard and fire in
the presence of any short-circuits.
Inside the heat exchangers, the compres-
sors and the refrigeration lines, this unit
contains liquid and gaseous refrigerant un-
der pressure. The release of this refrigerant
may be dangerous and cause injuries.
The units are not designed to be operated
with natural refrigerants, such as hydrocar-
bons. Itelco-Clima may not be held liable
for any problems deriving from the replace-
ment of original refrigerant or the introduc-
tion of hydrocarbons.
Itelco-Clima units are designed and manufactured
according to the requirements of European Standard
PED 97/23/EC (pressure vessels).
– The used refrigerants are included in group II (non-
hazardous fluids).
– The maximum working pressure values are men-
tioned on the unit’s data plate.
– Suitable safety devices (pressure switches and safe-
ty valves) have been provided, to prevent any
anomalous overpressure inside the plant.
– The vents of the safety valves are positioned and
oriented in such a way as to reduce the risk of con-
tact with the operator, in the event that the valve is
operated. Anyway, the installer will convey the dis-
charge of the valves far from the unit.
It is the User’s responsibility to ensure that
the unit is fit for the conditions of intended
use and that both installation and mainte-
nance are carried out by experienced per-
sonnel, capable of respecting all the recom-
mendations provided by this manual. It is
important that the unit is adequately sup-
ported, as detailed in this manual. Non-
compliance with these recommendations
may create hazardous situations for the
personnel.
The unit must rest on a base which meets
the characteristics specified in this manual;
a base with inadequate characteristics is
likely to become a source of serious injury
to the personnel.
The unit has not been design to withstand
loads and/or stress that may be transmitted
by adjacent units, piping and/or structures.
Each external load or stress transmitted to
the unit may break or cause breakdowns in
the unit’s structure, as well as serious dan-
gers to people. In these cases, any form of
warranty will automatically become null
and void.
The packaging material must not be dis-
posed of in the surrounding environment or
burnt.
2.2 Definitions
OWNER: means the legal representative of the com-
pany, body or individual who owns the plant where
Itelco-Clima unit has been installed; he/she has the
responsibility of making sure that all the safety regu-
lations specified in this manual are complied with,
along with the national laws in force.
INSTALLER: means the legal representative of the
company who has been given by the owner the job
of positioning and performing the hydraulic, electric
and other connections of Itelco-Clima unit to the
plant: he/she is responsible for handling and prop-
erly installing the appliance, as specified in this man-
ual and according to the national regulations in
force.
OPERATOR: means a person authorised by the own-
er to do on Itelco-Clima unit all the regulation and
control operations expressly described in this manu-
al, that must be strictly complied with, without ex-
ceeding the scope of the tasks entrusted to him.
Manuale CWP 4.11.2005 11:55 Pagina 3