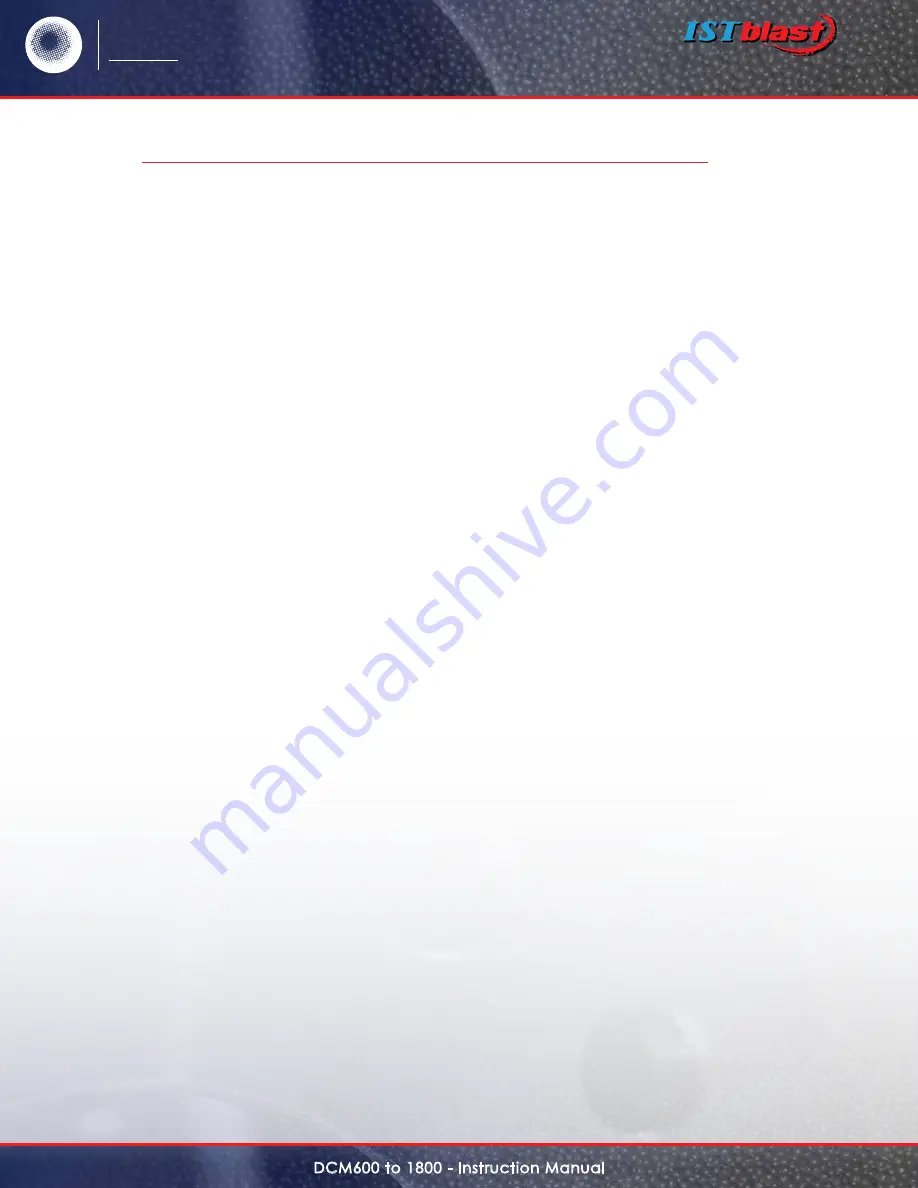
T
he
reference
in
surface
TreaTmenT
International
Surface
Technologies
i s t s u r f a c e . c o m
34
DCM600 to 1800 - Instruction Manual
we’ve made it easy to navigate the DCT1000. Menu items can be accessed simply by pressing the “SELECT”
button. The menu item that you are currently accessing is indicated by the illumination of an LED. To change
menu items, all you have to do is push “UP” to increase a value or push “DOwN” to decrease a value. There are
no keystrokes that you need to memorize, special combinations, or passwords that are required. The master
controller is equipped with an on board display and programming information center. The controller will
power-up with the process indicator illuminated. If a pressure module is installed, the display will indicate the
measured pressure in inches of water (w.c.); otherwise it will normally be blank
2.1 — last output
The Last Output setup selects the last channel to be activated. when first selected, the display will flash the last
output available in the system. with single board installations, this will be the number of channels installed,
typically 6, 10 or 22. This value becomes more important when multiple modules are installed. The last output
value flashed will be the sum of all channels available in the system.
After the last available channel indication has completed, the currently programmed last channel value is
displayed. This value may be changed using the “UP” and “DOwN” buttons. The minimum value is one while the
maximum value is the maximum number of installed channels, including all expansion modules. The default
value is the maximum number of channels. Pressing “SELECT” will change the setup mode to Time Off Setup.
2.2 — Time Off (Sec.)
Time off defines the period of time between solenoid activations when no channels are enabled. This may be
set between one second and 255 seconds. The factory default is 10 seconds. The display will show the current
time off setting when the time off setup mode is entered. The value may be changed using the Up and Down
buttons. Pressing both “UP” and “DOwN” simultaneously and holding for approximately four seconds will restore
the default value of 10.
2.3 • Time On (millisec. )
Time On Setup sets the solenoid on time. The display will indicate the currently programmed time on setting.
This is measured in milliseconds. Using the “UP” and “DOwN” buttons, the value may be changed. The value may
be set between 10 millisec. and 600 millisec. in 10 millisec. increments. Pressing the “UP” and “DOwN” buttons
simultaneously for approximately four seconds will restore the factory default value of 100 millisec. . Pressing
the “SELECT’ button will advance the setup mode to the High Limit setup if the pressure module is installed.
with no pressure module, it will step to Cycle Delay Setup.
2.4 • High Limit [Only available when DCP connected]
The High Limit Setup, available only with a pressure module installed, sets the pressure at which the cleaning
cycle will begin. This value may be between zero and the pressure module full scale pressure. Normally, the
High Limit should be above the Low Limit. If, however, the High Limit pressure is set below the Low Limit, the
cleaning cycle will begin when the High Limit is exceeded and stop when the pressure falls below the High
Limit. The Low Limit in this case will have no effect. Pressing “SELECT” will change the system to the Low Limit
Setup mode.
2.5 • Low Limit [Only available when DCP installed]
The operation of the Low Limit, available only with a pressure module installed, is identical to the High Limit
except this value sets the pressure where the cleaning cycle will end. The upper settable value is the calibration
pressure of the pressure module and the lower limit is zero. Pressing “SELECT” will change the system to the
High Alarm Setup mode.
2.0 — PrograMMing tHe dCt1000 Master Controller