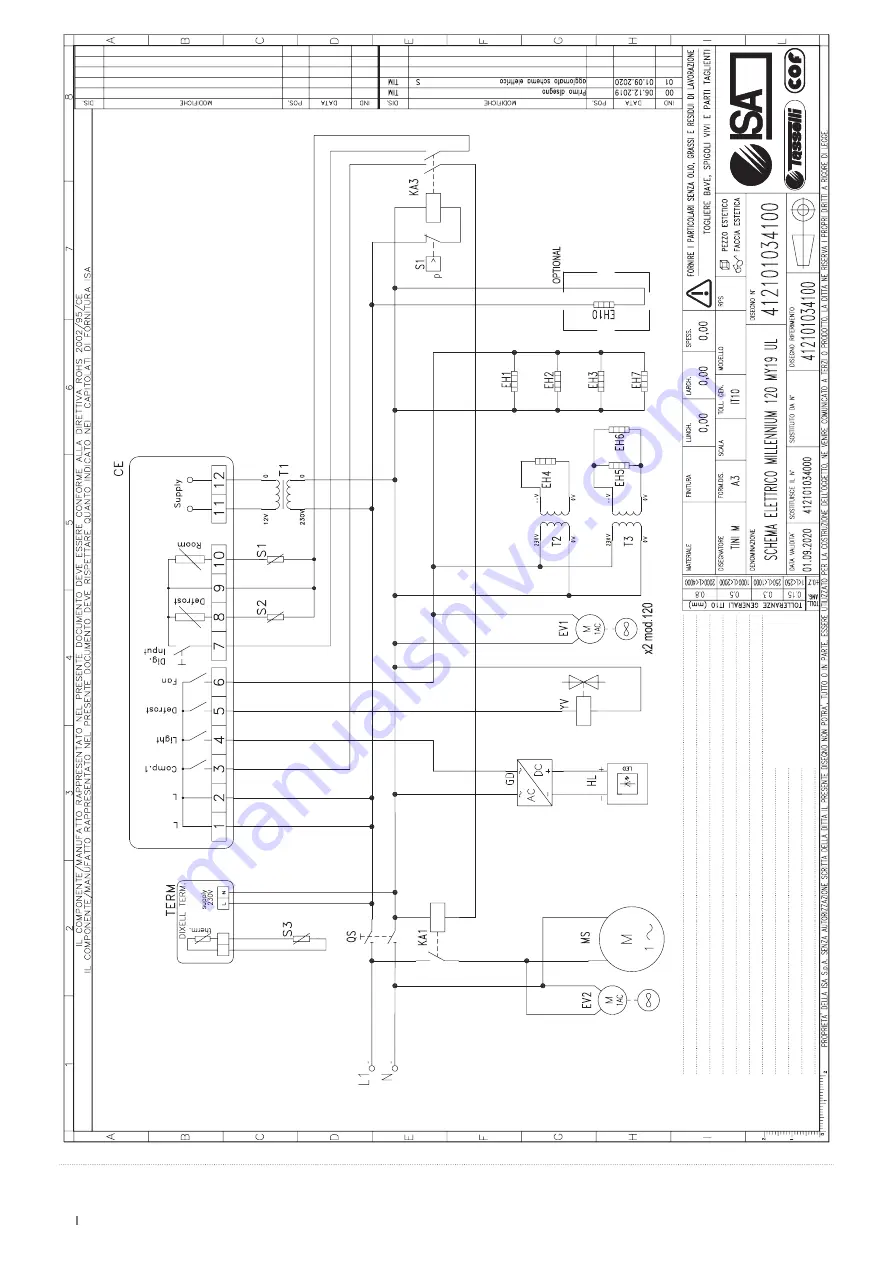
WIRING DIAGRAM
45
MILLENNIUM
EN 428001275137
Use and maintenance manual
S1
TEMPERA
TURE PROBE
EH10
DRIP DEFROSTING HEA
TING RESIST
OR
TERM
THERMOMETER
S2
DEFROST PROBE
EV1
EV
APORA
TOR F
AN
CE
ELECTRONIC C
ONTROL BO
ARD
S3
THERMOMETER PROBE
EV2
CONDENSER F
AN
KA1
COMPRESSOR RELA
Y
EH1
HEA
TINGRESIST
OR W
ORKING SURF
ACE
GD
LED PO
WER SUPPL
Y
KA3
PRESSURE SWIT
CH RELA
Y
EH2
SIDE HEA
TING RESIST
OR
HL
LED LAMP
S1
PRESSURE SWIT
CH
EH3
SIDE HEA
TING RESIST
OR
MS
COMPRESSOR
QS
MAIN SWIT
CH
EH4
HEA
TED FRONT GLASS
T1
TRANSFORMER C
ONTROL
EH5
HEA
TED GLASS SIDE
T2
TRANSFORMER
EH6
HEA
TED GLASS SIDE
T3
TRANSFORMER
EH7
RESIST
ANCE OF FRONT
AL HEA
TING
YV
DEFROST SOLENOID V
AL
VE