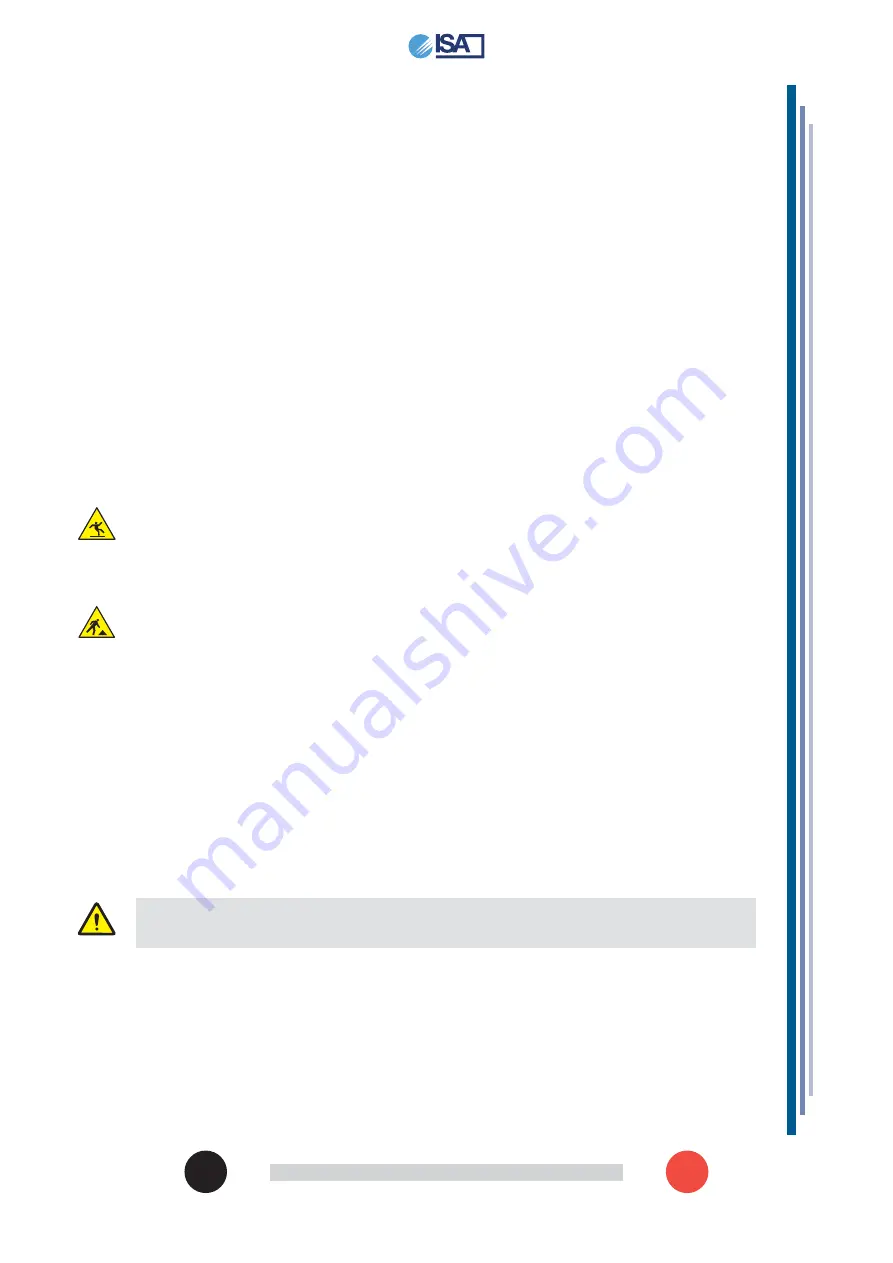
8
ISABELLA LX
USE AND MAINTENANCE MANUAL
428000085137
EN
R404A
2.3.3 Explosive atmosphere
The equipment must not be located in an area classifi ed as an explosion risk according to
1999/92/EC such as:
Zone 0
An area in which there is a permanent, long-lasting or frequently explosive atmosphere
made up of a mixture of air and fl ammable substances in the form of gases, fumes or
steam.
Zone 1
An area in which the formation of an explosive atmosphere, made up of a mixture of air and
fl ammable substances in the form of gases, fumes or steam is occasionally probable during
normal activities.
Zone 20
An area in which there is a permanent, long-lasting or frequently explosive atmosphere in
the form of clouds of combustible dust in the air.
Zone 21
An area in which the formation of an explosive atmosphere in the form of clouds of
combustible dust is occasionally probable during normal activities.
2.3.4 Slipping
Any leaks in the areas surrounding the equipment may cause personnel to slip.
Check that there are no leaks and keep these areas clean at all times.
2.3.5 Tripping
Generally untidy deposits of material may constitute a tripping hazard and a total or partial
obstruction of emergency exit routes.
You should ensure that operating and transit areas and emergency exit routes are free from
obstacles in compliance with current legislation.
2.3.6 Circuit faults
Owing to potential faults, safety circuits may become less effective, which results in lower
safety levels.
You should check the operational condition of the present safety devices regularly.
2.4 Warning signs
(if any)
Owing to the presence of various residual risks identifi ed, the equipment is fi tted with
hazard, warning and obligation signs devised in compliance with regulations relating to
graphical symbols for use on systems.
The signs are located in clearly visible positions.
Attention
It is strictly forbidden to remove the warning signs on the equipment.
The user is responsible for replacing warning signs that, owing to wear, become unreadable.
Summary of Contents for ISABELLA LX 10
Page 26: ......